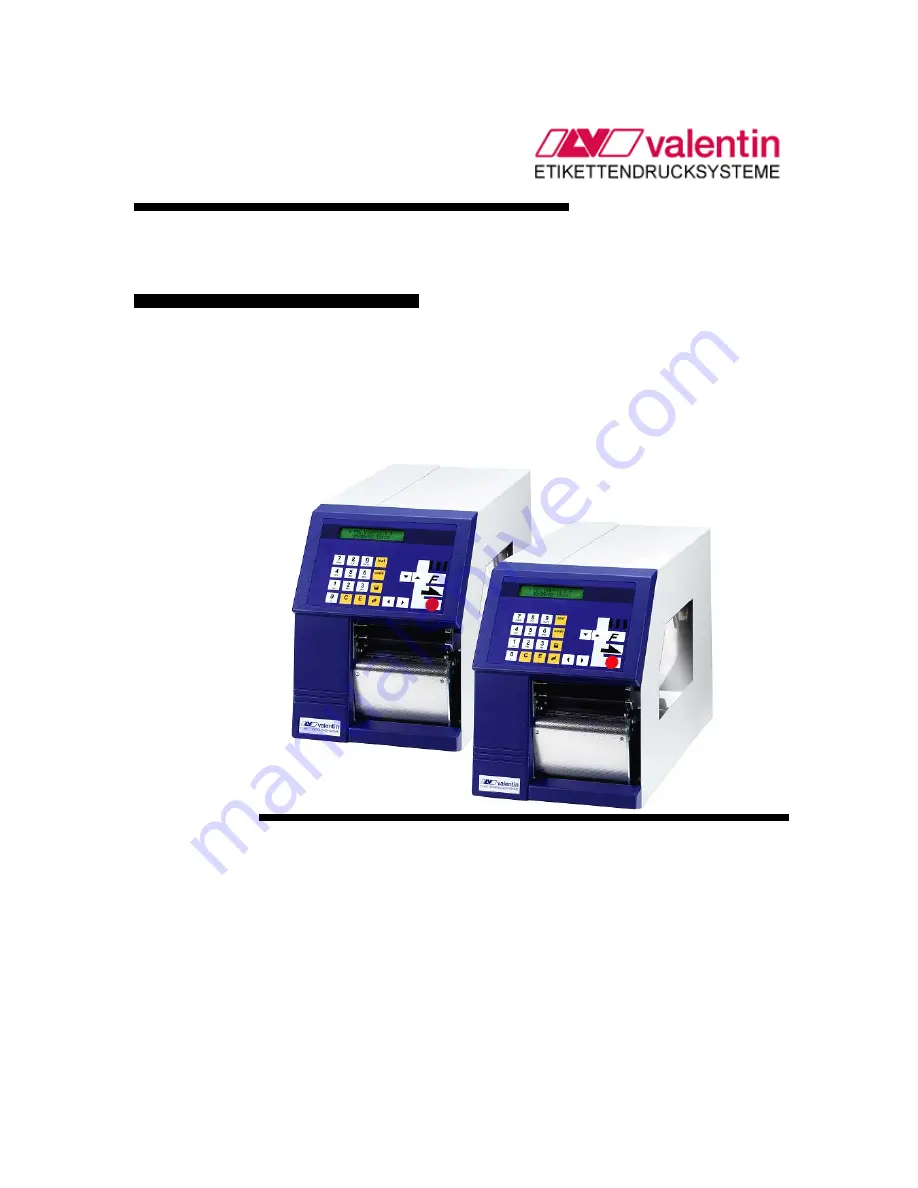
Service Manual - English
Vario II Series
79.55.023 • September 2002
All rights reserved.
Carl Valentin GmbH • Neckarstraße 78 – 82 & 94 • 78056 Villingen-Schwenningen
[email protected] • www.valentin-carl.de
Summary of Contents for Vario II series
Page 2: ......
Page 6: ......
Page 7: ...Service Manual 1 WIRING PLANS Electronics ...
Page 8: ...Service Manual 2 CPU Plan of components ...
Page 11: ...Service Manual 5 MEMORY CARD SLOT Option Plan of components ...
Page 13: ...Service Manual 7 INPUT OUTPUT PLATE OPTION Plan of components ...
Page 54: ......
Page 60: ......