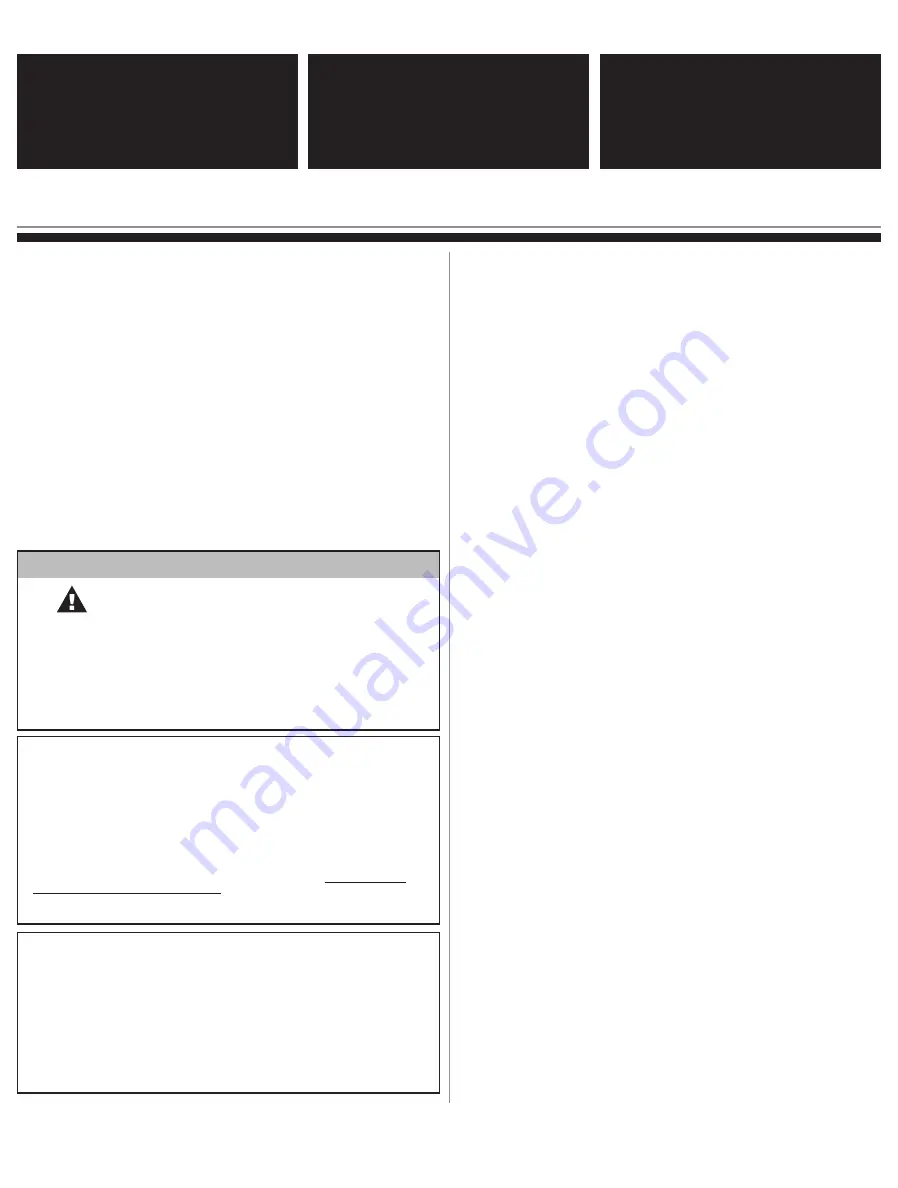
INSTALLATION INSTRUCTIONS
5/16˝, 3/8˝ & 1/2˝
(6 mm, 10 mm and 13 mm)
ENGINEERED PRODUCTS
FOR STAPLE-DOWN, MECHANICALLY FASTENED,
FLOATING AND GLUE-DOWN APPLICATIONS
INSTRUCCIONES DE INSTALACIÓN
5/16˝, 3/8˝ y 1/2˝
(6 mm, 10 mm y 13 mm)
PRODUCTOS PROCESADOS
PARA APLICACIONES GRAPADAS, DE SUJECIÓN
MECANIZADA, FLOTANTES O CON PEGAMENTO
INSTRUCTIONS D’INSTALLATION
6 mm, 10 mm et 13 mm
(5/16 po, 3/8 po et 1/2 po)
PRODUITS DE REVÊTEMENT DE
SOL S’INGÉNIERIE
POUR LES APPLICATIONS FIXÉES MÉCANIQUEMENT OU
À L’AIDE D’AGRAFES, COLLÉES ET FLOTTANTES
GENERAL INFORMATION
Owner/Installer Responsibility
Beautiful hardwood floors are a product of nature and therefore, not perfect. Our hardwood floors are
manufactured in accordance with accepted industry standards, which permit grading deficiencies not to
exceed 5%. These grading deficiencies may be of a manufacturing or natural type. When flooring is ordered,
5% must be added to the actual square footage needed for cutting and grading allowance (10% for diagonal
installations).
• The owner/installer assumes all responsibility for final inspection of product quality. Inspection of all
flooring should be done prior to installation. Carefully examine flooring for color, finish and quality before
installing it. If material is not acceptable, do not install it and contact the seller immediately.
• Prior to installation of any hardwood flooring product, the owner/installer must determine that the job-site
environment and the sub-surfaces involved meet or exceed all applicable standards. Recommendations
of the construction and materials industries, as well as local codes, must be followed. These instructions
recommend that the construction and subfloor be clean, dry, stiff, structurally sound and flat. The
manufacturer declines any responsibility for job failure resulting from, or associated with, subfloor and
substrates or job-site environmental deficiencies.
• Prior to installation, the owner/installer has final inspection responsibility as to grade, manufacture and
factory finish. The installer must use reasonable selectivity and hold out or cut off pieces with deficiencies,
whatever the cause. Should an individual piece be doubtful as to grade, manufacture or factory finish, the
installer should not use the piece.
• Use of stain, filler or putty stick for touch-up and appropriate products for correcting subfloor voids is
accepted as part of normal installation procedures.
Storage and Handling
• Handle and unload with care. Store in a dry place being sure to provide at least a four-inch air space under
cartons which are stored upon “on-grade” concrete floors. Flooring should not be delivered until the
building has been enclosed with windows doors are in place, and cement work, plastering and all other
“wet” work is completed and dry.
• Although it is not necessary to acclimate engineered flooring it is best to store it in the environment in
which it is expected to perform prior to installation. Check adhesive label for adhesive storage limitations.
Subfloor Conditions
• CLEAN − Subfloor must be free of wax, paint, oil, sealers, adhesives and other debris.
• LEVEL/FLAT − Within 3/16˝ in 10´ (5 mm in 3 m) and/or 1/8˝ in 6´ (3 mm in 2 m). Sand high areas or joints. If the
floor is to be glued down, fill low areas with a latex additive cementitous leveling compound of 3,000-PSI minimum
compressive strength Underlayment & Embossing Leveler with Underlayment Additive. Follow the instructions
of the leveling compound manufacturer, but make certain the leveling compounds are completely DRY before
beginning installation. When mechanically fastening the floor down, flatten low spots with a maximum of 6 layers of
15# builders felt, plywood or shims (not leveling compounds). Leveling materials must provide a structurally sound
subfloor that does not affect the holding power of the fastener.
• DRY − Check and document moisture content of the subfloor using the appropriate moisture test. Concrete
subfloors must be a minimum of 30 days old before testing begins.
• STRUCTURALLY SOUND − Nail or screw any areas that are loose or squeak. Wood panels should exhibit an
adequate fastening pattern, glued/screwed or nailed as system requires, using an acceptable nailing pattern.
Typical: 6˝ (15 cm) along bearing edges and 12˝ (31 cm) along intermediate supports. Flatten edge swell as
necessary. Replace any water-damaged, swollen or delaminated subflooring or underlayments.
Avoid subfloors with excessive vertical movement. Optimum performance of hardwood floor covering
products occurs when there is little horizontal or vertical movement of the subfloor. If the subfloor has
excessive vertical movement (deflection) before installation of the flooring, it is likely it will do so after
installation of the flooring is complete.
Subfloors with Radiant Heat
NOTE: Always make certain the product selected is recommended for this type application.
• System must be operational and heated for at least 7 days prior to beginning the installation.
• Use an incremental control strategy that brings the floor through temperature changes gradually which may
include an external thermostat.
• Turn off heat and let subfloor cool down to room temperature 3-4 hours prior to starting the job.
• BEFORE installation begins, ascertain that the heating system is designed and controlled for wood flooring
and that the circuit does not include other floor covering types. Failure to do so may cause excessive heat
damage and shrinkage. NOTE: Refer to radiant heat system manufacturer’s precautions for staple down
installation. Beware of stapling through radiant tubing or mesh.
• After installation, turn the heating system back on immediately. The finished floor surface must not exceed
85°F (29°C) throughout the life of the floor.
• Radiant heating systems normally create dry heat that can lower interior humidity levels. It may be
necessary to add humidity with humidifiers to maintain the recommended levels (35-55%) and prevent
damage to the wood floor.
• The flooring should be end-glued over radiant heat to reduce longitudinal shrinkage. Apply a bead of the
recommended wood glue to the groove end then insert the tongue. Wipe excess adhesive away immediately.
Tools & Accessories Needed
(All Installation Methods)
• Broom • Tape measure • Hammer • Chalk line & chalk • Hand saw or jamb saw
• Recommended hardwood flooring cleaner • Electric power saw • Eye protection
• Recommended wood glue • Moisture Meter (wood, concrete or both)
• Transition and wall moldings • NIOSH-designated dust mask
(Add for Glue-Down Installations)
• Recommended adhesive and adhesive remover
• 1/4˝ x 1/2˝ x 3/16˝ (6 mm x 13 mm x 8 mm) V-Notch trowel • 3M Scotch-Blue™ 2080 tape
• Recommended wood glue for floors exceeding 3-1/4˝ (9.5 cm) in width
• Moisture Retardant System on concrete (if needed). Use with urethane adhesive only.
(Add for Mechanically Fastened/Staple-Down Installations)
• Stanley-Bostich LHF 2025K, LHF 97125-2 or Powernail 20FS
• 1˝ Staples/fasteners (minimum) 20 Gauge • Compressor and hose • Nylon/Plastic tapping block
• In-line regulator • Recommended wood glue for floors exceeding 3-1/4˝ (9.5 cm) in width
(Add for Floating Installations)
• Recommended underlayment • Pull bar • Tapping block • Recommended wood glue
STEP 1: Doorway and Wall Preparation
(All Installation Methods)
Undercut door casings and jambs. Remove any existing base, shoe mold or doorway thresholds.
ATTENTION INSTALLERS
CAUTION: WOOD DUST
Sawing, sanding and machining wood products can produce wood dust. Airborne
wood dust can cause respiratory, eye and skin irritation. The International Agency for
Research on Cancer (IARC) has classified wood dust as a nasal carcinogen in humans.
Precautionary Measures:
If power tools are used, they should be equipped with a dust collector. If high
dust levels are encountered, use an appropriate NIOSH-designated dust mask. Avoid dust contact with eye
and skin.
First Aid Measures in Case of Irritation:
In case of irritation, flush eyes or skin with water for at least
15 minutes.
WARNING:
EXISTING IN-PLACE RESILIENT FLOOR COVERING AND ASPHALTIC
ADHESIVES. DO NOT SAND, DRY SWEEP, DRY SCRAPE, DRILL, SAW, BEADBLAST, OR
MECHANICALLY CHIP OR PULVERIZE EXISTING RESILIENT FLOORING, BACKING,
LINING FELT, ASPHALTIC “CUTBACK” ADHESIVE, OR OTHER ADHESIVE.
These existing in-place products may contain asbestos fibers and/or crystalline silica.
Avoid creating dust. Inhalation of such dust is a cancer and respiratory tract hazard.
Smoking by individuals exposed to asbestos fibers greatly increases the risk of serious bodily harm.
Unless positively certain that the existing in-place product is a non-asbestos-containing material, you
must presume it contains asbestos. Regulations may require that the material be tested to determine
asbestos content and may govern removal and disposal of material.
See current edition of the Resilient Floor Covering Institute (RFCI) publication Recommended Work
Practices for Removal of Resilient Floor Coverings for instructions on removing all resilient floor
covering structures or contact your retailer.
The floor covering or adhesive in this package does NOT contain asbestos.
Minnesota Residential Formaldehyde Regulation:
IMPORTANT HEALTH NOTICE THESE
BUILDING MATERIALS EMIT FORMALDEHYDE, EYE, NOSE, AND THROAT IRRITATION, HEADACHE,
NAUSEA AND A VARIETY OF ASTHMA-LIKE SYMPTOMS, INCLUDING SHORTNESS OF BREATH, HAVE BEEN
REPORTED AS A RESULT OF FORMALDEHYDE EXPOSURE. ELDERLY PERSONS AND YOUNG CHILDREN,
AS WELL AS ANYONE WITH A HISTORY OF ASTHMA, ALLERGIES, OR LUNG PROBLEMS, MAY BE AT
GREATER RISK. RESEARCH IS CONTINUING ON THE POSSIBLE LONG-TERM EFFECTS OF EXPOSURE TO
FORMALDEHYDE. REDUCED VENTILATION MAY ALLOW FORMALDEHYDE AND OTHER CONTAMINANTS
TO ACCUMULATE IN THE INDOOR AIR. HIGH INDOOR TEMPERATURES AND HUMIDITY RAISE
FORMALDEHYDE LEVELS. WHEN A HOME IS TO BE LOCATED IN AREAS SUBJECT TO EXTREME SUMMER
TEMPERATURES, AN AIR-CONDITIONING SYSTEM CAN BE USED TO CONTROL INDOOR TEMPERATURE
LEVELS. OTHER MEANS OF CONTROLLED MECHANICAL VENTILATION CAN BE USED TO REDUCE LEVELS
OF FORMALDEHYDE AND OTHER INDOOR AIR CONTAMINANTS. IF YOU HAVE ANY QUESTIONS REGARDING
THE HEALTH EFFECTS OF FORMALDEHYDE, CONSULT YOUR DOCTOR OR LOCAL HEALTH DEPARTMENT.