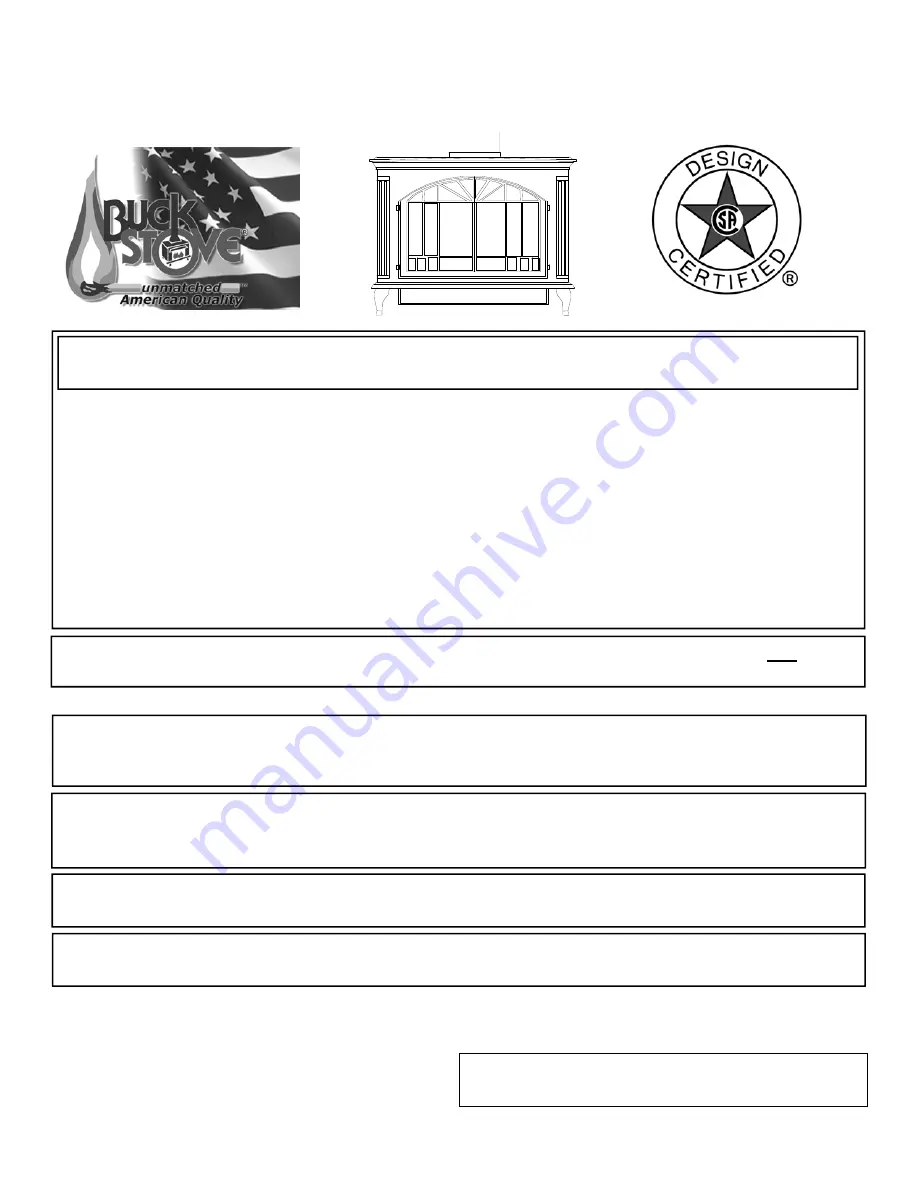
MODEL: CDVB200
CAST STOVE AND DIRECT-VENT
NATURAL OR L.P. (LIQUID PROPANE) FREESTANDING GAS STOVE HEATER
OWNER’S OPERATION AND INSTALLATION MANUAL
Revised September 2010
Approved By:
WARNING: If the information in these instructions are not followed exactly, a fire or explosion may
result causing property damage, personal injury or loss of life.
⎯
Do not store or use gasoline or other flammable vapors and liquids in the vicinity of this or any
other appliance.
⎯
WHAT TO DO IF YOU SMELL GAS
•
Do not try to light any appliance.
•
Do not touch any electrical switch; do not use any phone in your building.
•
Immediately call your gas supplier from a neighbor’s phone. Follow the gas suppliers instruc-
tions.
•
If you cannot reach your gas supplier, call the fire department.
⎯
Installation and service must be performed by a qualified installer, service agency or the gas sup-
plier.
INSTALLER:
Leave this manual with the appliance.
CONSUMER:
Retain this manual for future reference.
MANUFACTURED BY NEW BUCK
CORPORATION
200 ETHAN ALLEN DRIVE, PO BOX 69
SPRUCE PINE, N.C. 28777
(*) Indicates Color Suffix Designation)
www.buckstove.com
WARNING:
The Direct-Vent (CDV) burner system provided in this package must be installed only into the
approved cast iron stove body Townsend II provided by New Buck Corporation.
WARNING:
Improper installation, adjustment, alteration, service, or maintenance can cause injury or property
damage. Refer to this manual for correct installation and operational procedures. For assistance or additional
information consult a qualified installer, service agency, or the gas supplier.
This Burner System (Direct Vent) has been tested and approved for use with the following Vent Pipe
manufacturers: “Use only Simpson-Dura-Vent or AmeriVent GS venting components or kits, these
types have been tested and approved specifically for this stove and burner system.”
WARNING: This appliance may be installed in an aftermarket, permanently located, manufactured
home (USA only) or mobile home, where not prohibited by local codes.
* Aftermarket: Completion of sale, not for purpose of resale,
from the manufacturer.
WARNING:
Only New Buck Corporation approved
blower assembly may be used with the CDV installed
into the Townsend II.
This appliance is only for use with the type of gas indicated on the rating plate. This appliance is not
convertible for use with other gases.