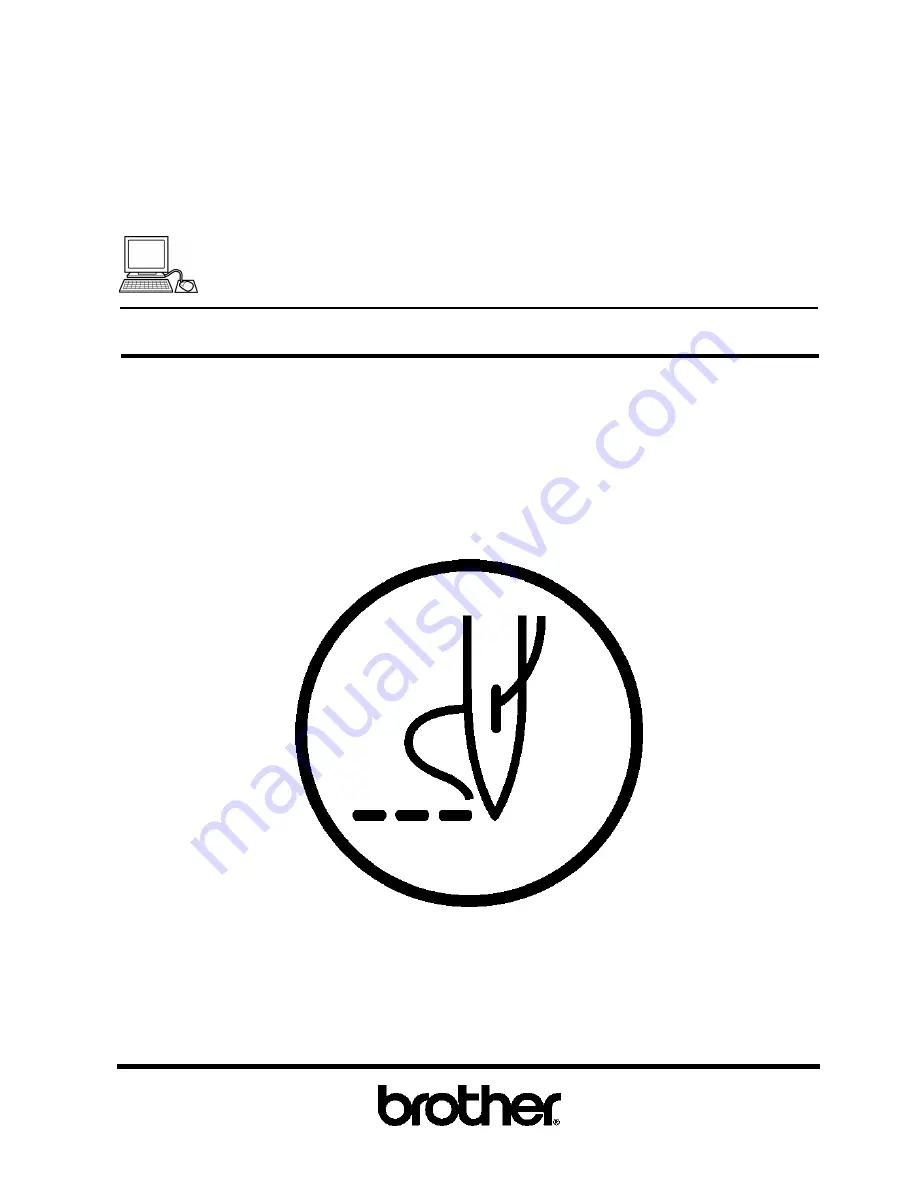
BE-1204B-BC
BE-1204C-BC
BE-1206B-BC
PC Control type
Please read this manual before using the machine.
Please keep this manual within easy reach for quick reference.
TWELVE NEEDLE FOUR HEAD EMBROIDERY MACHINE
TWELVE NEEDLE FOUR HEAD EMBROIDERY MACHINE<WIDE AREA>
TWELVE NEEDLE SIX HEAD EMBROIDERY MACHINE
INSTRUCTION MANUAL
Summary of Contents for BE-1204B
Page 2: ......
Page 9: ...BE 1204B BC BE 1206B BC 7 W1400Q W1208Q 5 4 6 7 5 8 9 11 4 8 8 4 4 1 2 10 3 ...
Page 19: ...Chapter 1 An Introduction of Embroidery Machine ...
Page 21: ...BE 1204B BC BE 1204C BC BE 1206B BC 1 3 Chapter 1 An Introduction of Embroidery Machine ...
Page 28: ...1 10 BE 1204B BC BE 1206B BC Chapter 1 An Introduction of Embroidery Machine ...
Page 29: ...Chapter 2 Preparation of Embroidery Machine ...
Page 56: ...2 28 BE 1204B BC BE 1206B BC Chapter 2 Preparation of Embroidery Machine ...
Page 66: ...3 10 BE 1204B BC BE 1206B BC Chapter 3 Embroidering Procedures ...
Page 126: ...5 34 BE 1204B BC BE 1206B BC Chapter 5 Editing Embroidery Data ...
Page 188: ...6 62 BE 1204B BC BE 1204C BC BE 1206B BC Chapter 6 Embroidering ...
Page 189: ...Chapter 7 Operation of Machine ...
Page 221: ...Chapter 9 Maintenance ...
Page 231: ...Chapter 10 Adjustment ...
Page 240: ...10 10 BE 1204B BC BE 1206B BC Chapter 10 Adjustment ...
Page 241: ...Chapter 11 Error code list ...
Page 248: ...11 8 BE 1204B BC BE 1206B BC Chapter 11 Error code list ...
Page 257: ...Chapter 13 Connection and Installation of Optional Equipment ...
Page 260: ...13 4 BE 1204B BC BE 1206B BC Chapter 13 Connection and Installation of Optional Equipment ...
Page 261: ......