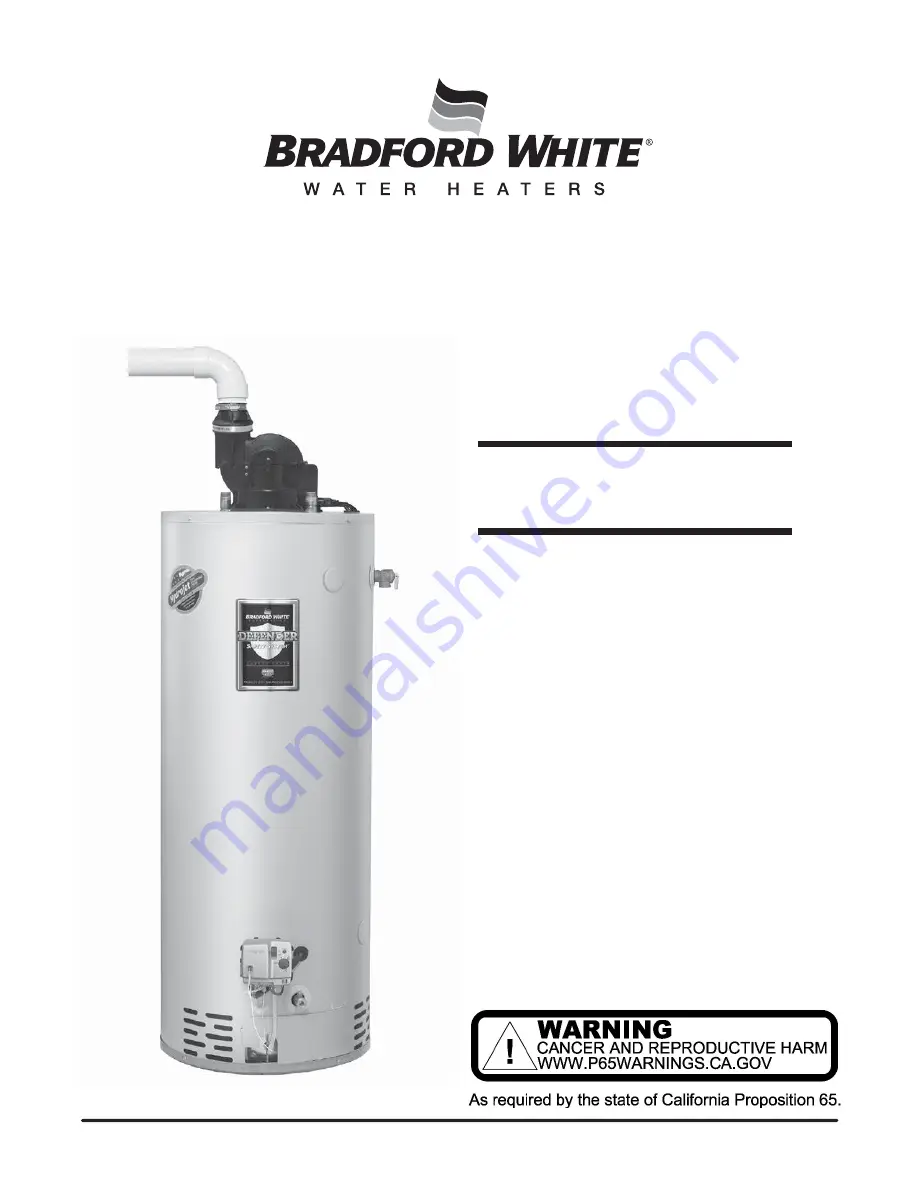
Save this manual for future reference
Manual 238
‐
51540
‐
00A
REV 08/18
SERVICE
MANUAL
Troubleshooting Guide
and Instructions for Service
(To be performed ONLY by
qualified service providers)
Models Covered
by This Manual:
Through
‐
The
‐
Wall Models:
RG1PV40S*(N,X)
RG1PV50S*(N,X)
RG1PV55H*(N,X)
RG2PV40T*(N,X)
RG2PV50H*(N,X)
RG2PV50T*(N,X)
RG2PV75H*(N,X)
LG1PV55H78*(N,X)
LG2PV50H65*(N,X)
LG2PV75H76*(N,X)
(*) Denotes Warranty Years
Power Vent Gas Water Heaters
PV Series