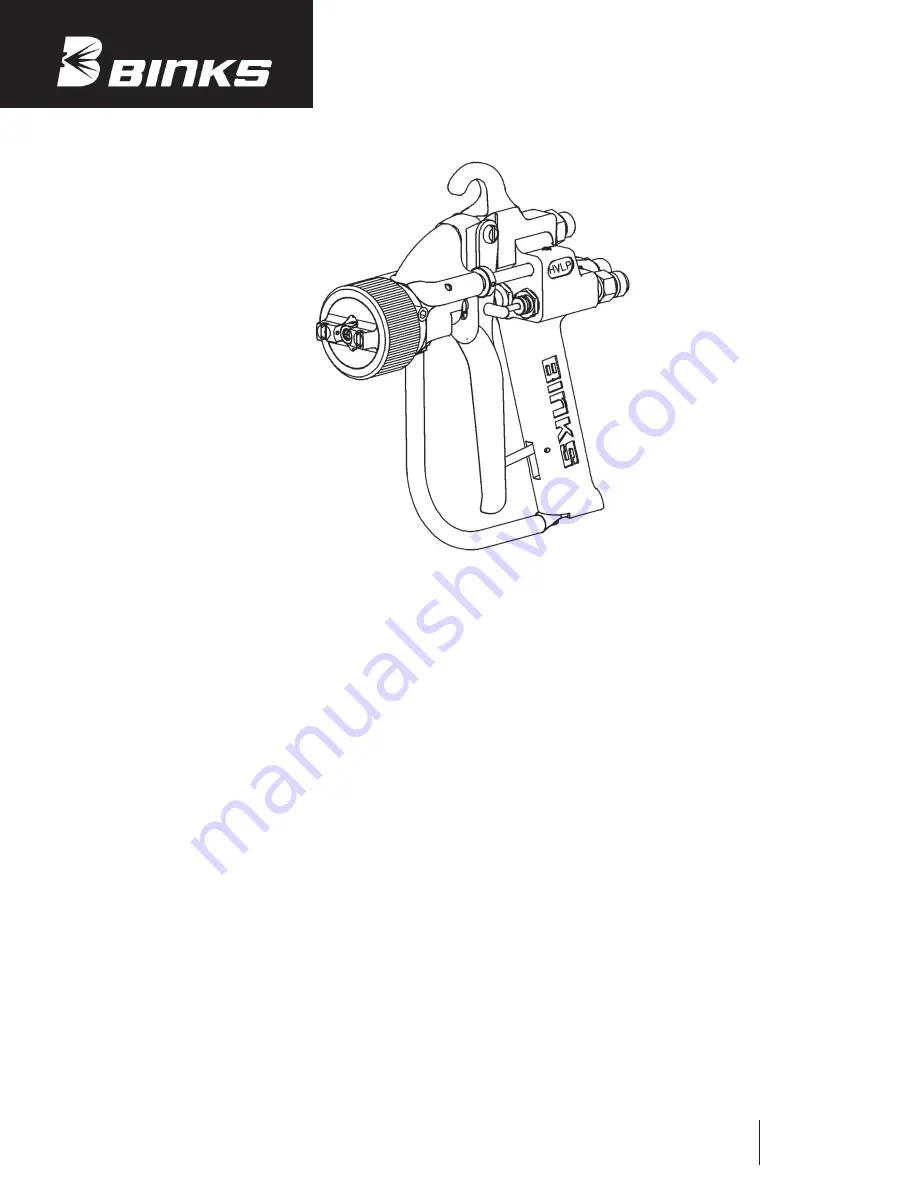
Binks Model 202-755
HVLP GUN ASSEMBLY
Replaces
Part Sheet
77-2756R-1
Part
Sheet
77-2756R-2
READ BEFORE OPERATING
Your new High Volume, Low Pressure (HVLP) Spray gun
complies with the strict California South Coast Air Quality
Management District Rule #1162 along with Air Quality Rules
in other geographical areas. You should also know that the defi-
nition of H.V.L.P., as defined in the S.C.A.Q.M.D. Rule #1162
reads, ”High Volume Low Pressure (HVLP) spray is a coating
application system which is operated at air pressure of between
0.1 and 10 pounds per square inch gauge (PSIG).”
To maintain compliance and best results, we suggest:
1. Install air pressure test gauge (207-11799) with adapter in
gun nozzle body.
2. With an air hose connected to the assist air connection on rear
of gun, set assist air pressure to a maximum of 40 psi. Because
of the superb flow characteristics of the gun design, 40 psi
max is all that is ever required with only few exceptions.
3. Open pattern control thumbwheel all the way. Pull trigger
and observe the pressure reading of the test gauge. It should
not exceed 10 psi. Should the test gauge indicate more or
less than 10 psi, increase or decrease regulated air supply
until 10 psi is shown on test gauge while pulling trigger.
You might want to put a “landmark” on your air control
gauge for easy reference. The variables of air hose length
and regulator and gauge types sometimes require that these
adjustments become necessary.
4. Remove test gauge and adapter and install 1/16
″
NPT pipe
plug furnished. You are now in compliance for the criteria
HVLP. Should your local Air Quality Officer or Inspector
ever request air pressure reading, co-operate and install test
gauge and demonstrate that your nozzle pressure is 10 psi
or less.
The material transfer efficiency of your 755 HVLP Gun is
excellent but resin and catalyst pressure(s) must also be correctly
set for optimum results.
We suggest:
1. Resin pump pressure should be set as low as possible for an
acceptable spray pattern. Remember the assist air (10 psi)
plays a big part in the final spray pattern shape.
2. Select the proper spray tip for the job. A spray tip with too
small an orifice with excessive resin pump pressure would
result in poor results. It is recommended that a range of
spray tip sizes be on hand to avoid compromises. Your
spray pattern should be a soft, uniform shape without fin-
gers or tails. Resin “bounce back” should not occur.
Catalyst and catalyst atomizing pressures should also be set as
low as possible. Usually, the Catalyst Tank pressure is set at
35-40 psi. Catalyst Fan pressure should be 10 psi lower or
25-30 psi. Flowmeter (black ball) should be adjusted for
desired gel time. A good place to start would be a black ball
reading of between 60-80. Always test spray gun and gel times
on waste material until you’re ready to fabricate parts.
OPERATING INSTRUCTIONS