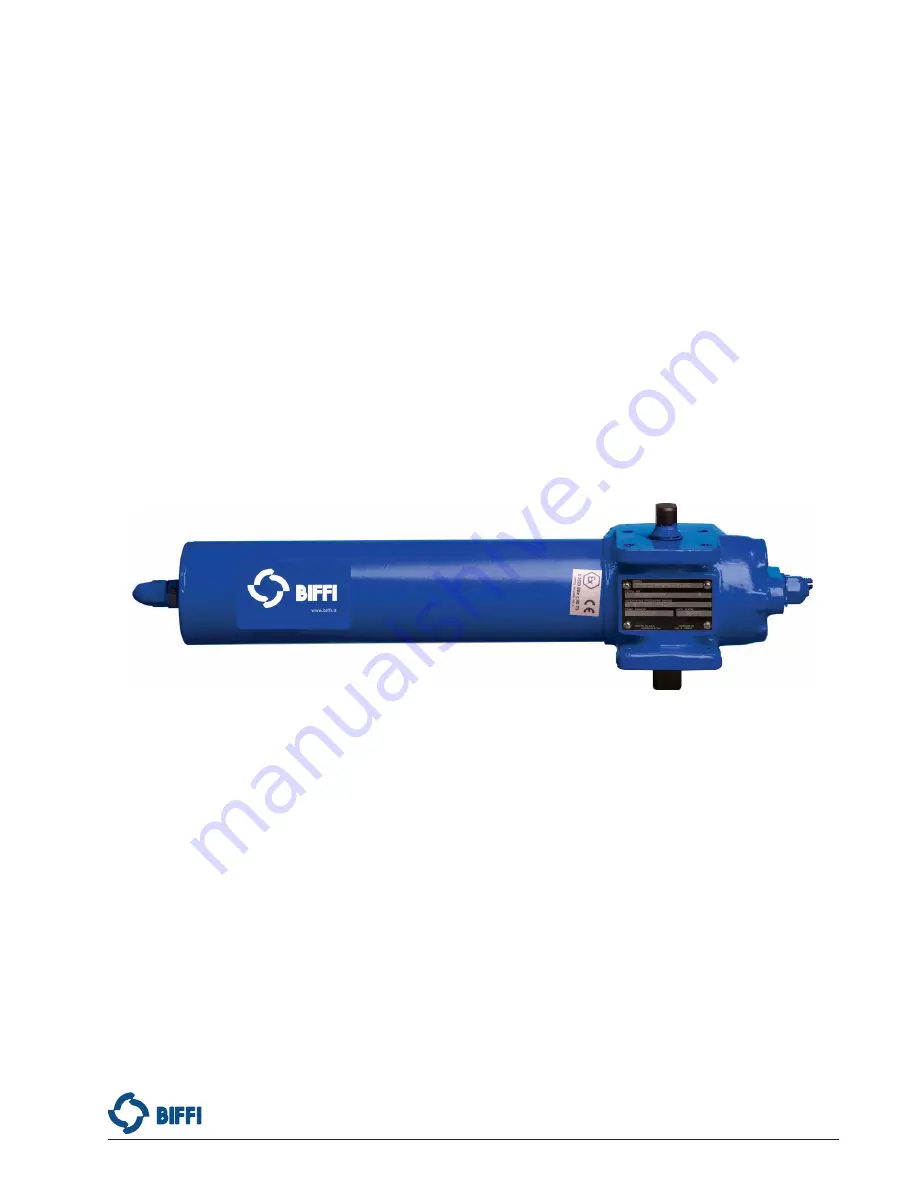
Service Instructions
VCIOM-15313-EN Rev. 1
March 2022
FCB Series Pneumatic Actuators
Model FCBB Spring-Return Dissasembly and Reassembly
Copyright © Biffi. The information in this document is subject to change without notice. Updated data sheets can be obtained from our website www.biffi.it or from your nearest Biffi Center:
Biffi Italia s.r.l. - Strada Biffi 165, 29017 Fiorenzuola d'Arda (PC) –
Italy PH:
+39 0523 944 411 – [email protected]
Summary of Contents for FCB Series
Page 2: ...This page intentionally left blank Notes March 2022 Service Instructions VCIOM 15313 EN Rev 1 ...
Page 4: ...This page intentionally left blank Notes March 2022 Service Instructions VCIOM 15313 EN Rev 1 ...
Page 29: ...Service Instructions VCIOM 15313 EN Rev 1 Notes March 2022 This page intentionally left blank ...