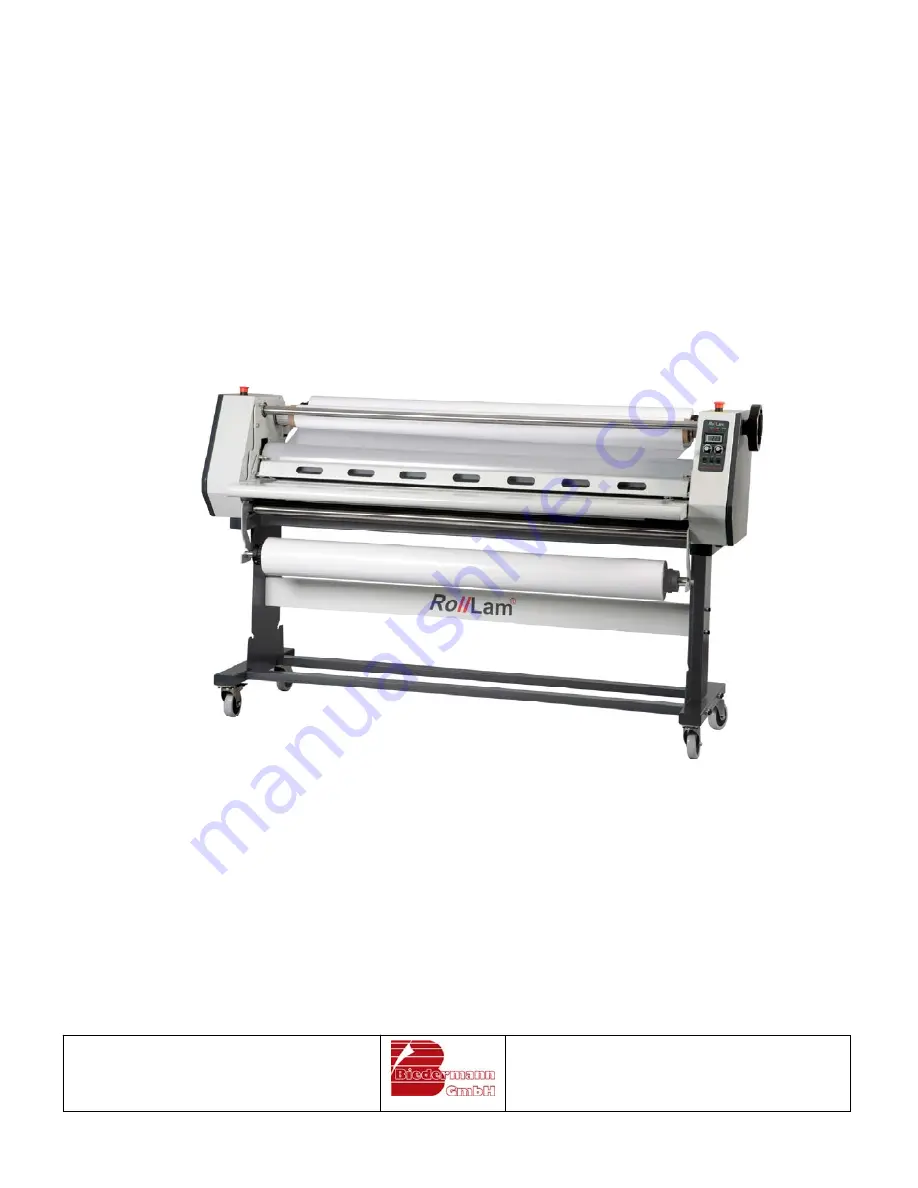
OPERATION
MANUAL
Laminators
RollLam 120W; RollLam 140W; RollLam 160W
Biedermann GmbH
Solutions for mounting and laminating
DE-70806 Kornwestheim, Heubergstraße 19
Phone:+49(0)7154-83990; Fax:+49( 0)7154-839983
E-mail: [email protected]
www.biedermanngmbh.com