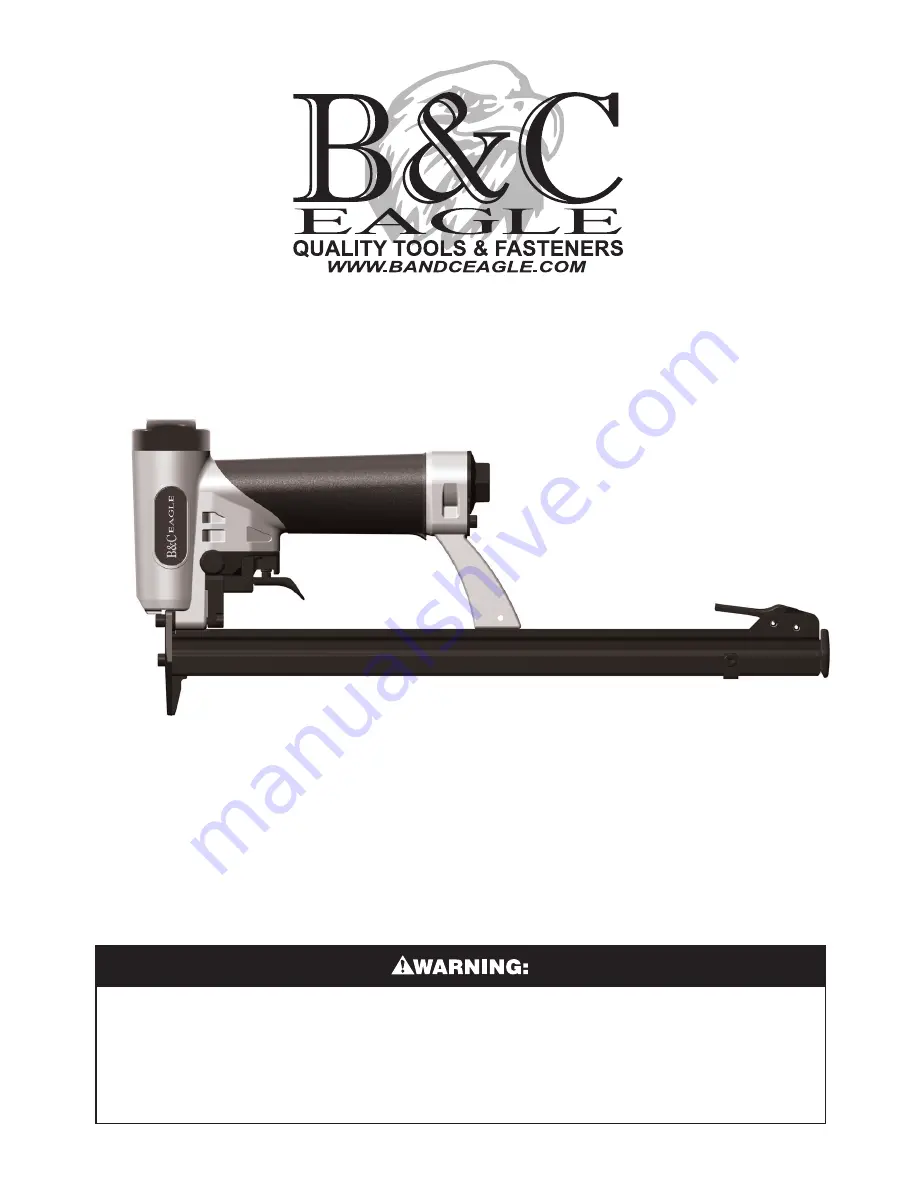
BEFORE OPERATING THIS TOOL, ALL OPERATORS SHOULD STUDY THIS
MANUAL TO UNDERSTAND AND FOLLOW THE SAFETY WARNINGS AND
INSTRUCTIONS. KEEP THESE INSTRUCTIONS WITH THE TOOL FOR FUTURE
REFERENCE.
IF
YOU
HAVE
ANY
QUESTIONS,
CONTACT
YOUR
REPRESENTATIVE OR DISTRIBUTOR.
OPERATION and MAINTENANCE MANUAL
US5016LMA
FINE WIRE AUTO STAPLER
Summary of Contents for US5016LMA
Page 11: ... 11 ...