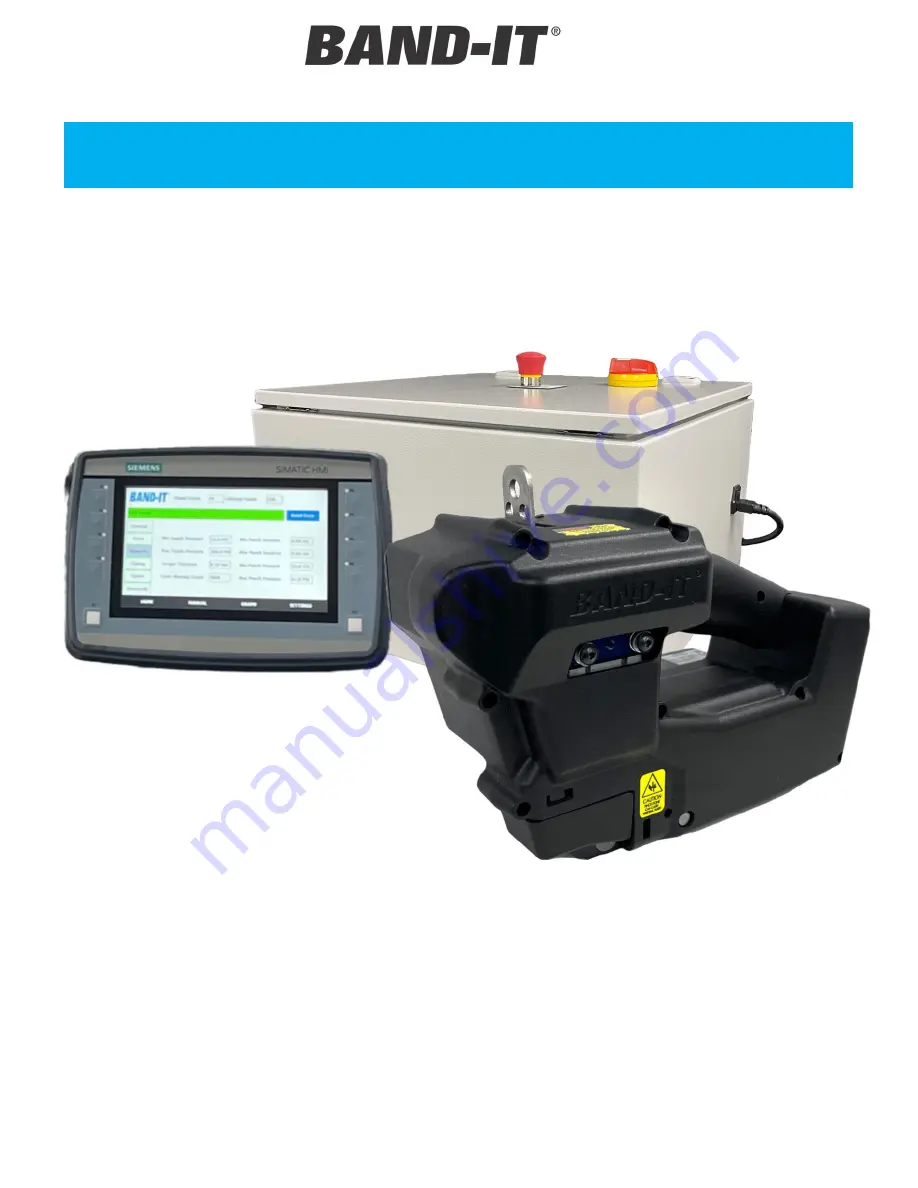
1
User Manual
IT8000
3/8” Tie
-Lok® Data Tool
Document #P80080 Rev. B
© Copyright
BAND-IT-IDEX, Inc. 2022
All rights reserved
All rights reserved
BAND-IT-IDEX, Inc.
A Unit of IDEX Corporation
4799 Dahlia Street
Denver, CO 80216-3070 USA
P: 1-800-525-0758
IT8000
User Manual
Original document
(Not a translation)