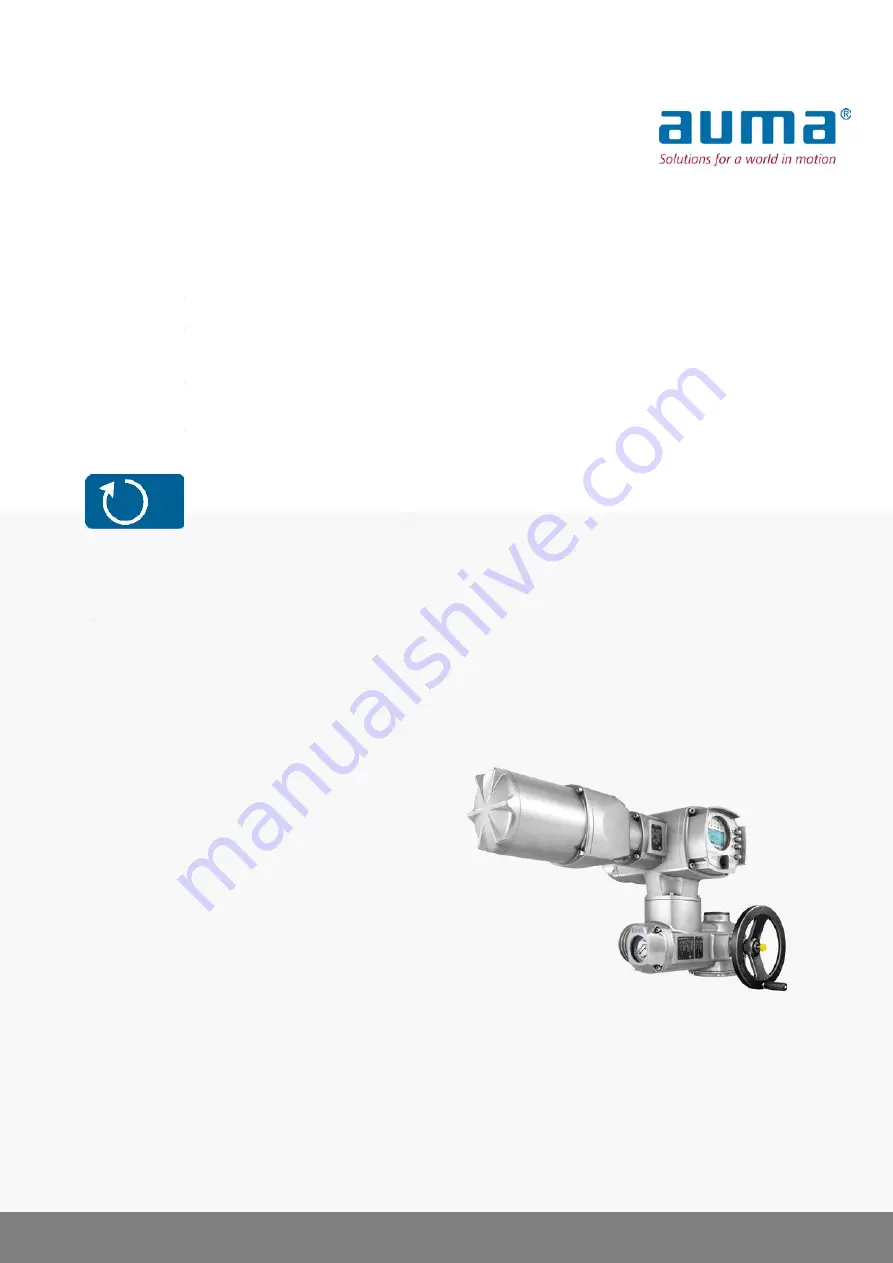
Control
Parallel
Profibus DP
Profinet
Modbus RTU
→
Modbus TCP/IP
Foundation Fieldbus
HART
Multi-turn actuators
SAEx 07.2 – SAEx 16.2
SAREx 07.2 – SAREx 16.2
Control unit: electronic (MWG)
with actuator controls
ACExC 01.2 Non-Intrusive
Multiport valve version
Assembly and commissioning
Operation instructions