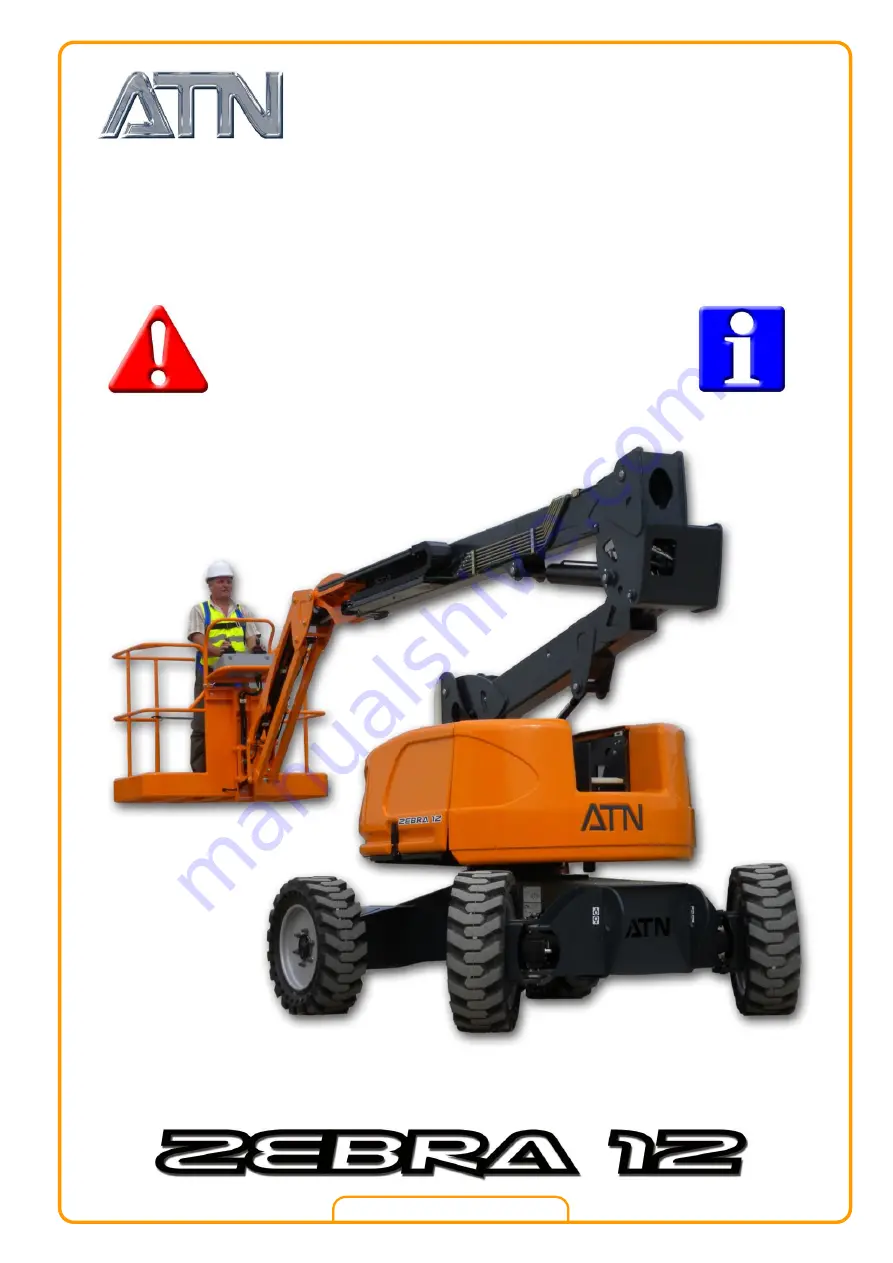
11/2009
1NO 0027FR-01
1NO0027UK-05 revision 08/2015
Lieu-Dit Bacqué, rue André Thévet
47400 FAUILLET - FRANCE
Tel: 33 (0)5 53 79 83 20
Fax: 33 (0)5 53 79 96 90
Email: [email protected]
www.atnplatforms.com
Operator and
Safety Manual
Translation of the original manual
Summary of Contents for Zebra 12
Page 2: ...OPERATOR AND SAFETY MANUAL 1NO0027UK 05 ZEBRA 12 2 DISTRIBUTOR S STAMP ...
Page 42: ...OPERATOR AND SAFETY MANUAL 1NO0027UK 05 ZEBRA 12 42 ...
Page 44: ...OPERATOR AND SAFETY MANUAL 1NO0027UK 05 ZEBRA 12 44 NOTES ...
Page 45: ...OPERATOR AND SAFETY MANUAL 1NO0027UK 05 ZEBRA 12 45 NOTES ...