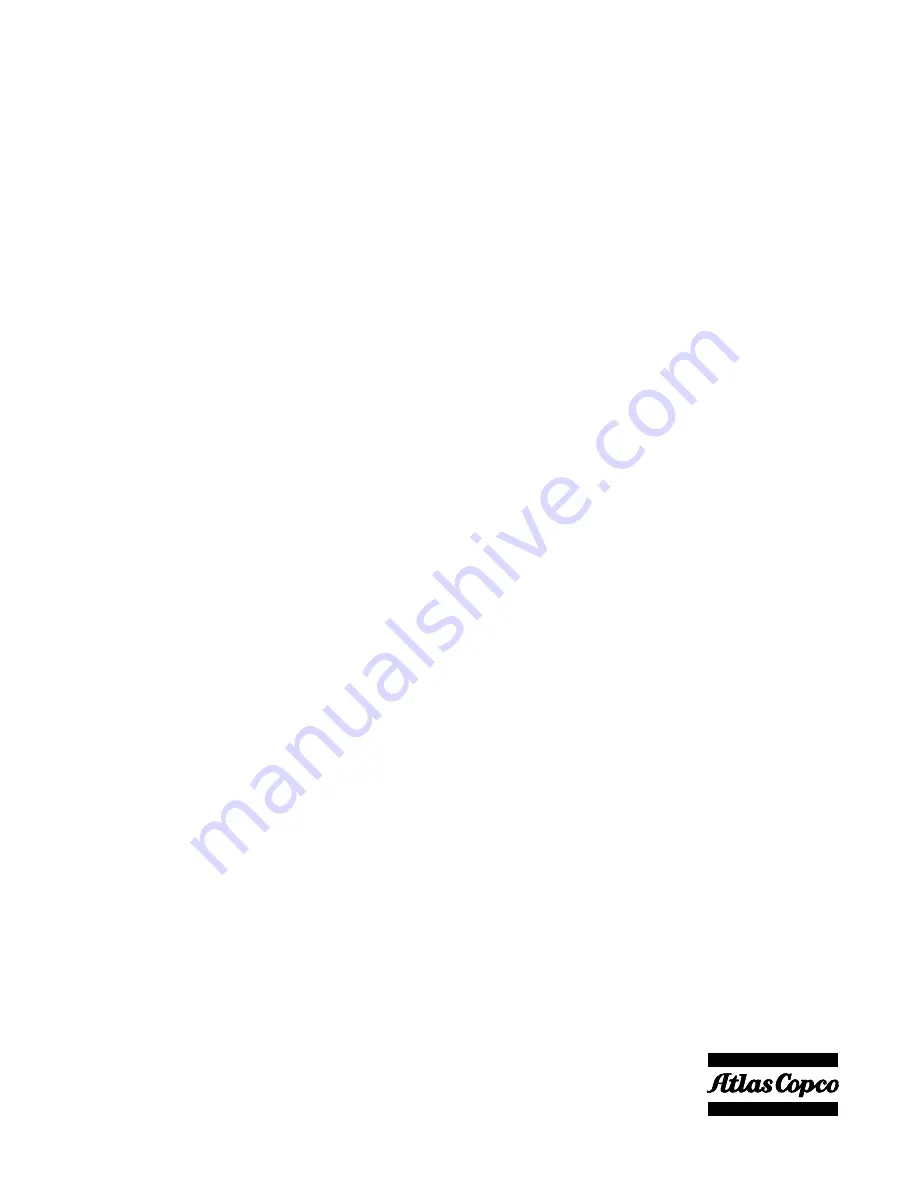
Atlas Copco
Stationary Air Compressors
*2920125704*
No. 2920 1257 04
Registration code: APC L / 38 / 989
Replaces 2920 1257 03
2000-10
LE/LT15, -22, -40, -55, -75, -110, -150
LF15, -22, -40, -55, -75
www.atlascopco.com
•
Copyright 2000, Atlas Copco Airpower n.v., Antwerp, Belgium.
Any unauthorized use or copying of the contents or any part thereof is prohibited. This applies in
particular to trademarks, model denominations, part numbers and drawings.
•
This instruction book meets the requirements for instructions specified by the machinery directive
98/37/EC and is valid for CE as well as non-CE labelled machines.
Instruction Book
Summary of Contents for LE110
Page 11: ...2920 1257 04 11 Instruction book Fig 2 2 Dimension drawing LE LT55 75 and LF40 55 Power Pack ...
Page 19: ...2920 1257 04 19 Instruction book Fig 2 10 Dimension drawing LE LT15 up to 40 Unsilenced Pack ...
Page 21: ...2920 1257 04 21 Instruction book Fig 2 12 Dimension drawing LE LT15 up to 150 with CD dryer ...