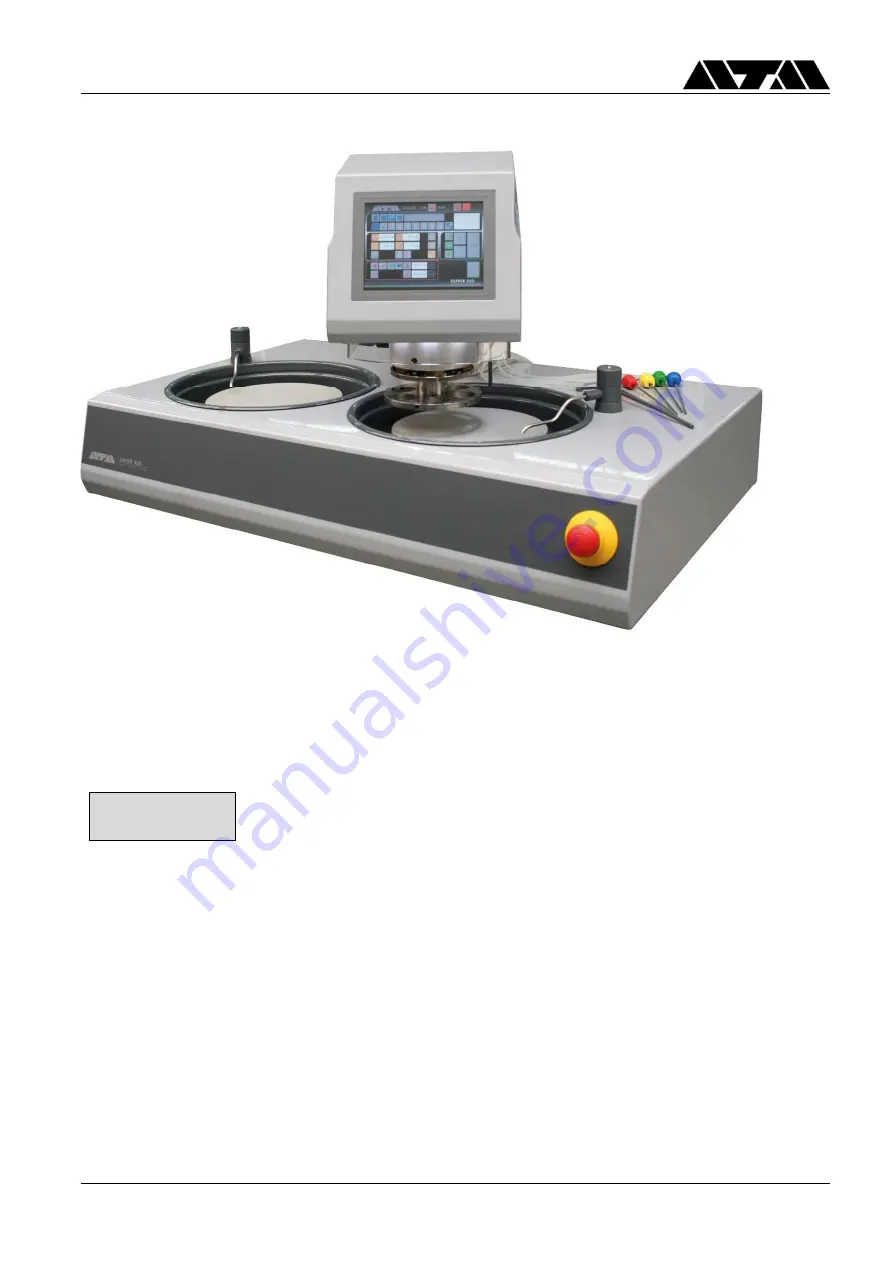
»SAPHIR 550/560
Operating Manual
GmbH
- 1 -
Stand: 03.02.2020
Introduction
This operating manual contains important instructions, descriptions and tips for operation and safety. It is the basis for
safe, economic and problem-free work.
Personnel must be instructed by an authorized person before the machine is commissioned.
Safety First
comes first!
Whoever works with or on the machine, transports or sets up the machine, commissions or decommissions the
machine, maintains or cleans the machine, is obligated to read and observe these safety instructions, guidelines
and precautions.
This will prevent injuries to persons and damage to the machine, material and environment. Furthermore, any
claim in accordance with EU machine guideline 2006/42/EU is nullified if the machine is used improperly.
This operating manual is a component part of the delivered device.
Made in Germany
Summary of Contents for SAPHIR 550
Page 42: ...0 1 ...