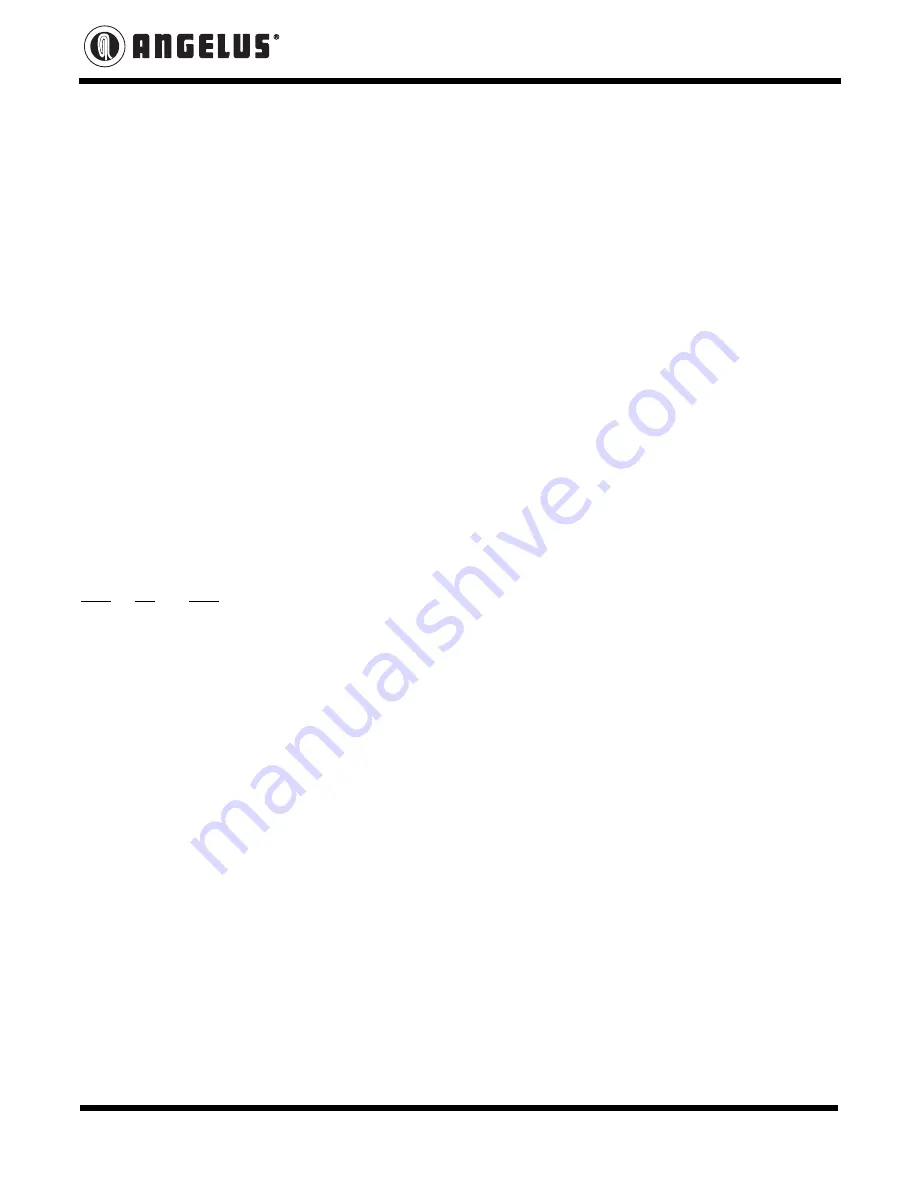
Angelus 4900 Pacific Blvd. Los Angeles, CA 90058-2214 Tel: (323) 583-2171 1/1
Service Notices
Model 180S
1) Select the Bookmark option
2) Click on appropriate Service Notice
Service Notice Numbering and Tracking System
The following layout is using a single part number for reference
65L614 Rubber Plug
8 characters used as a "File Name" on the computer system.
060
14
001
Subdivision related to the part "14" which will continually increase as the number
of Lubrication Notices are created.
Type of part - Main Division, such as "14" for Lubrication or "44" for Shafts or "00" for an
assembled component.
Designates Seamer Model Number
Revisions to existing Service Notices will be as follows:The "File Name" will be duplicated on
the Service Notice with the latest revision level designated by a letter.
Example: 06014001"A". Revision levels on Service Notices are rare but can happen. The
Service Notice will provide remaining needed information.