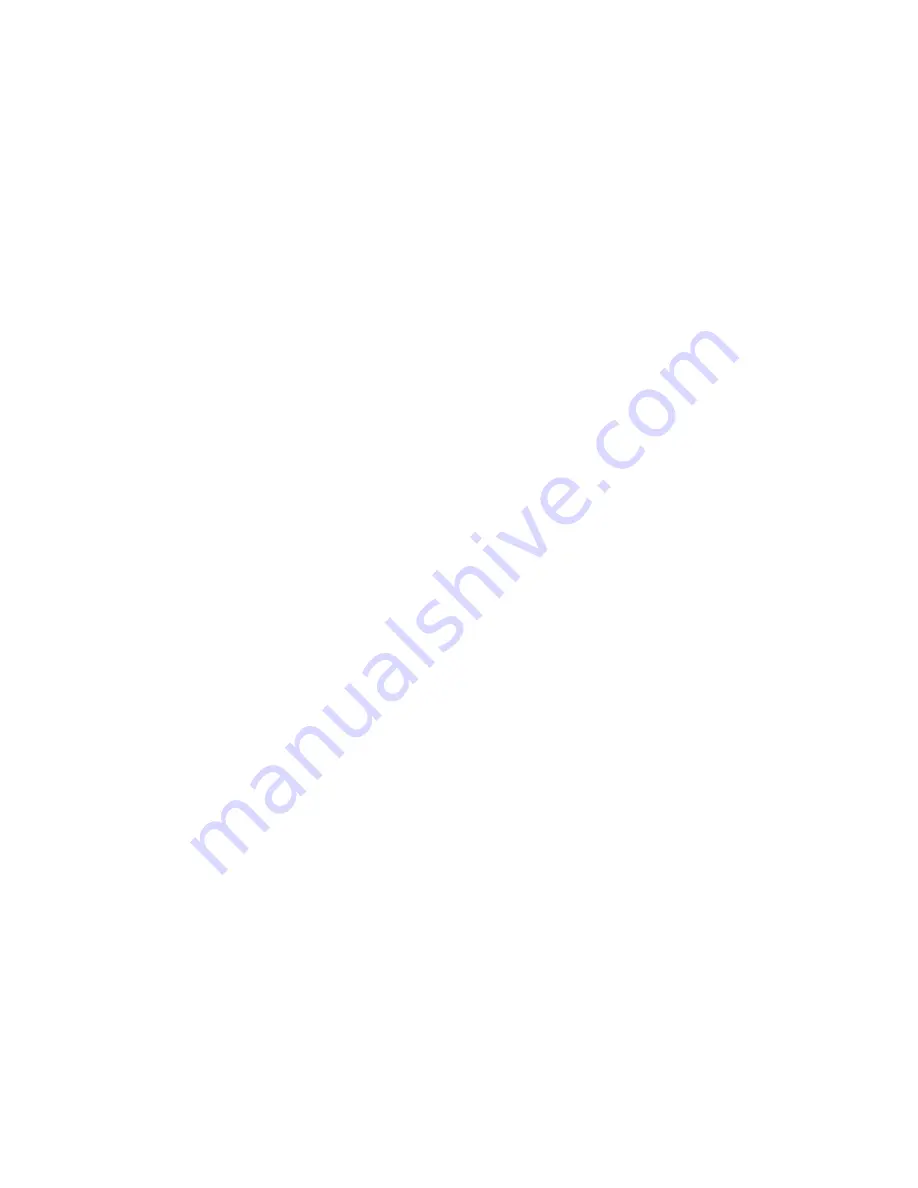
OWNERS MANUAL
AMS 2000HD Series Hard Drive Shredder
Thank you for purchasing an Ameri-Shred Shredder. This model is made of the finest
materials available and is manufactured in the Unites States by skilled craftsmen. The
shredder has been designed with the operator in mind for both ease of operation and
maintenance. Ameri-Shred requests that each operator read and familiarize themselves with
this manual before operating the machine.
The AMS 2000HD Series Hard Drive Shredder is designed by Ameri-Shred Engineers to shred
hard drives and other electronic media into unusable particles to ensure that the information
they contain is rendered useless. Ameri-Shred believes in using the highest quality
components in each of our industrial shredders.
Included in this manual are safety tips, operating instructions, preventative maintenance and
lubrication schedules, trouble shooting information , and a parts list. For information or
questions that may not be found in this manual please contact our service department at
888-270-6879.
NOTICE
: The information contained within this manual is correct at time of printing, but due to the
continuing development of products, changes in specifications are inevitable. Ameri-Shred reserves the
right to implement such changes without prior notice.
Summary of Contents for 2000HD Series
Page 17: ...17 SHREDDER OPERATION Figure 1 OUTPUT CONVEYOR CONTROL STATION INFEED CHUTE ...
Page 18: ...18 GUARD IDENTIFICATION Figure 2 FRONT LEFT RIGHT TOP ...
Page 19: ...19 CHAIN LUBRICATION Figure 3 ...
Page 21: ...21 CONVEYOR BELT TAKEUP Figure 5 ...
Page 22: ...22 CHAIN TENSIONER Figure 6 ...
Page 23: ...23 NAMEPLATE MODEL 2000 HDS S N VOLTS 60 CYCLE AC F L A 20 HP 3 PHASE JOB Figure 7 ...
Page 30: ...30 CUTTER HEAD ASSEMBLY ...
Page 33: ...APENDIX I REDUCER MANUAL ...
Page 34: ...34 ...
Page 35: ...35 ...
Page 36: ...36 ...
Page 37: ...37 ...
Page 38: ...38 ...
Page 39: ...39 ...
Page 40: ...40 ...
Page 41: ...41 ...
Page 42: ...42 ...
Page 43: ...43 ...
Page 44: ...44 ...
Page 45: ...45 ...