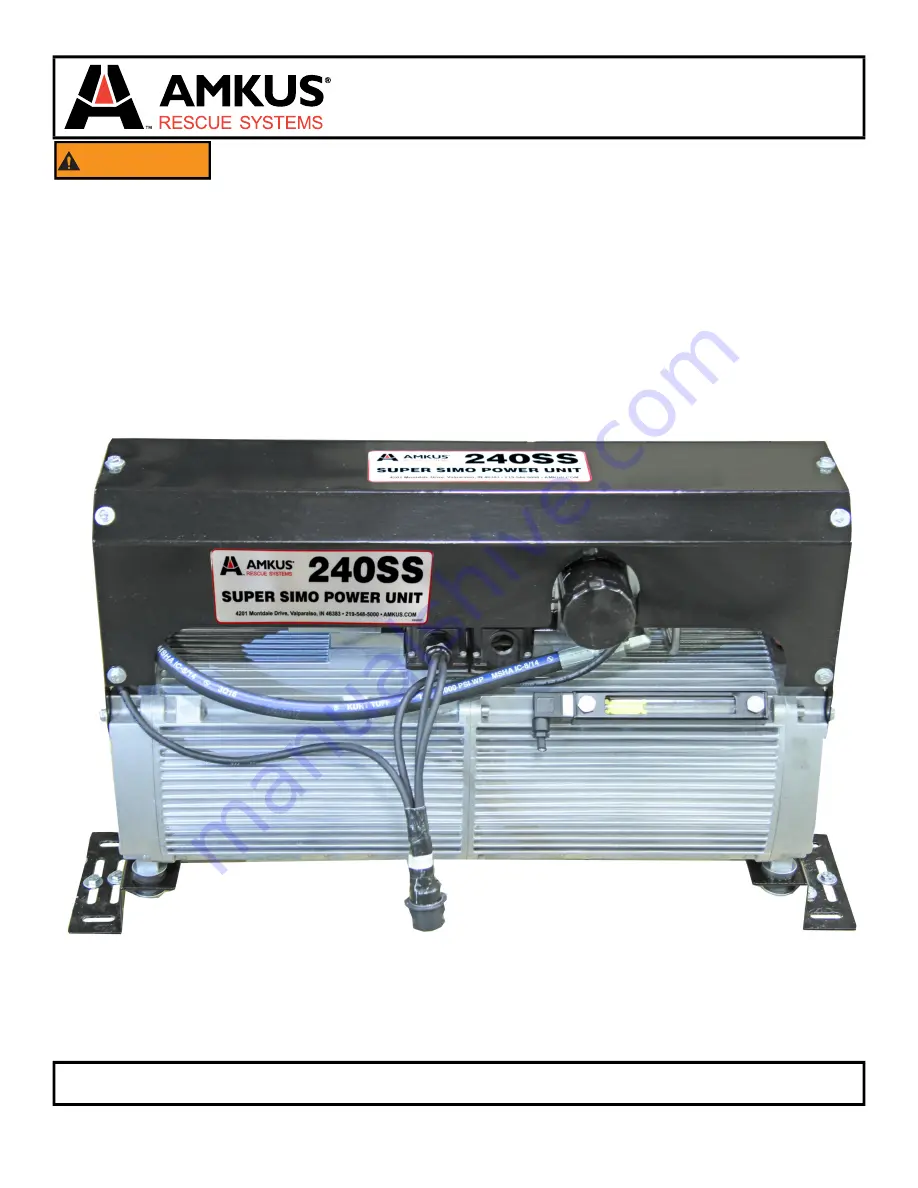
©Copyright AMKUS Rescue Systems 2020-2021
1
LAP-012 October 7, 2021 Rev02
AMKUS RESCUE SYSTEMS
AMKUS.com
4201 Montdale Drive, Valparaiso, IN 46383-4098 USA
800-592-6587 · 219-548-5000
G-Force
INSTRUCTIONS FOR INSTALLATION, OPERATION, AND MAINTENANCE
240SS
Super Simo Power Unit
WARNING
Understand manual before use. Operating AMKUS Rescue Systems without understanding the
manual, receiving proper training, and using appropriate personal protective equipment is a misuse
of AMKUS equipment. Obtain safety information at amkus.com
This instruction manual is intended to familiarize operators and maintenance personnel with the
operation, basic maintenance, and safety procedures associated with this product. This manual
should be kept available to all operating and maintenance personnel.
This manual does NOT address servicing of AMKUS Rescue Systems. Only competent rescue tool
repair technicians are qualified to repair AMKUS equipment.
This manual is intended for use with manuals published by manufacturers of the prime movers
(motor and pump) used in this power unit.