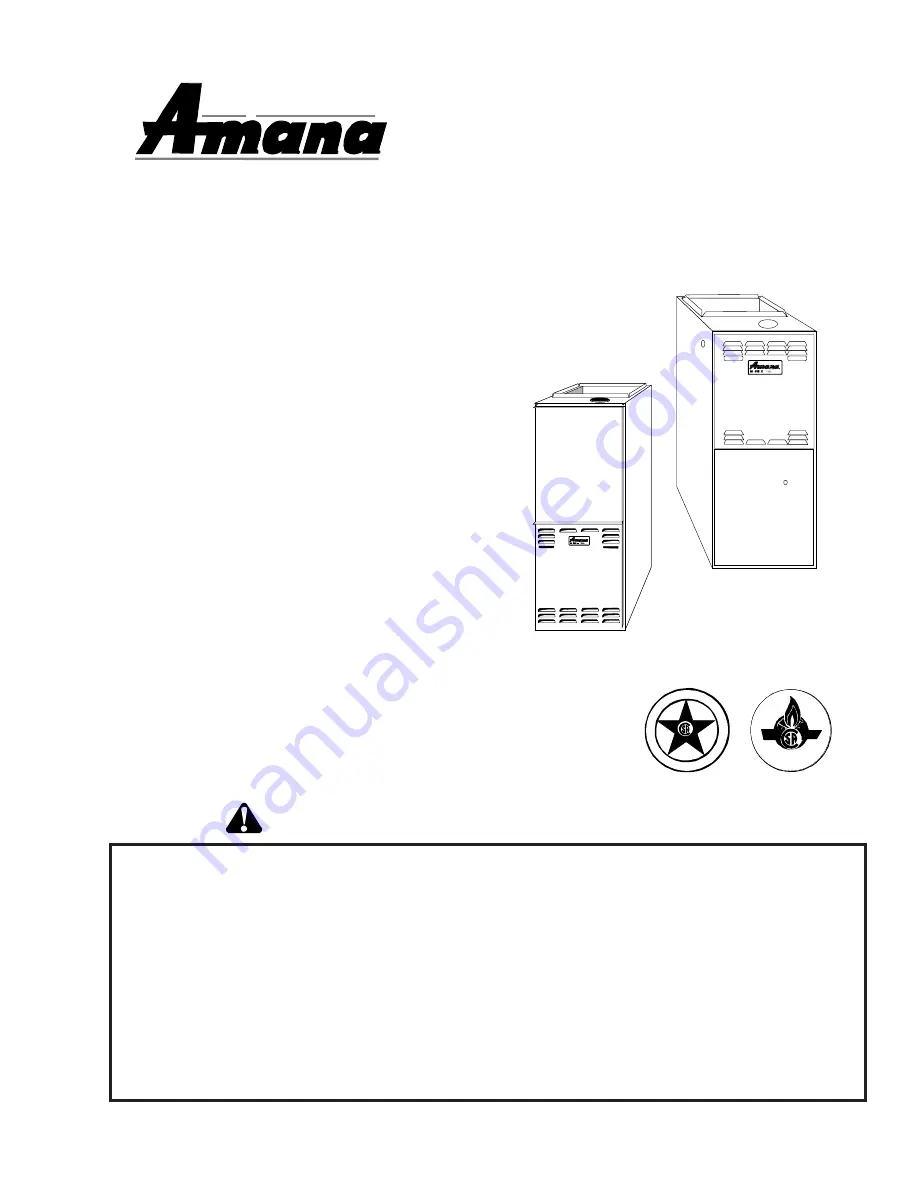
Amana
1810 Wison Parkway • Fayetteville, TN 37334
RECOGNIZE THIS SYMBOL AS A SAFETY PRECAUTION.
ATTENTION INSTALLING PERSONNEL
As a professional installer you have an obligation to
know the product better than the customer. This
includes all safety precautions and related items.
Prior to actual installation, thoroughly familiarize
yourself with this Instruction Manual. Pay special
attention to all safety warnings. Often during
installation or repair it is possible to place yourself
in a position which is more hazardous than when
the unit is in operation.
Remember, it is your responsibility to install the
product safely and to know it well enough to be able
to instruct a customer in its safe use.
Safety is a matter of common sense...a matter of
thinking before acting. Most dealers have a list of
specific good safety practices...follow them.
The precautions listed in this Installation Manual
are intended as supplemental to existing practices.
However, if there is a direct conflict between existing
practices and the content of this manual, the
precautions listed here take precedence.
October 2001
Rev. 5
10759825
Amana Forced Air Central Furnace Design Complies With Requirements
Embodied in The American National Standard / National Standard of Canada
Shown Below.
ANSI Z21.47•CSA-2.3 Central Furnaces
Table of Contents
To The Owner .............................................................. 2
To The Installer ........................................................... 2
I. Safety and Unit Location ..................................... 2
II. General Information ............................................. 3
III. Combustion and Ventilation Air Requirements . 4
IV. Category I Venting (Vertical Venting) .................. 6
V. Gas Supply and Piping ........................................ 8
Vl. Electrical Wiring ................................................. 12
VlI. Circulating Air and Filters ................................. 14
VIII. Sequence of Operation ..................................... 15
IX. Start-Up, Adjustments, and Checks .................. 16
X. Maintenance ....................................................... 24
GUIS/GCIS
Two-Stage Gas-Fired
Warm Air Furnace
Installation Instructions
Affix this manual, Specification Sheet and Users
Information Manual adjacent to the furnace.
DESIGN
C E RTIFIED
C E R T I F I E D
Com fort. Q uality. Trust.
Heating
®
&
Air Conditioning