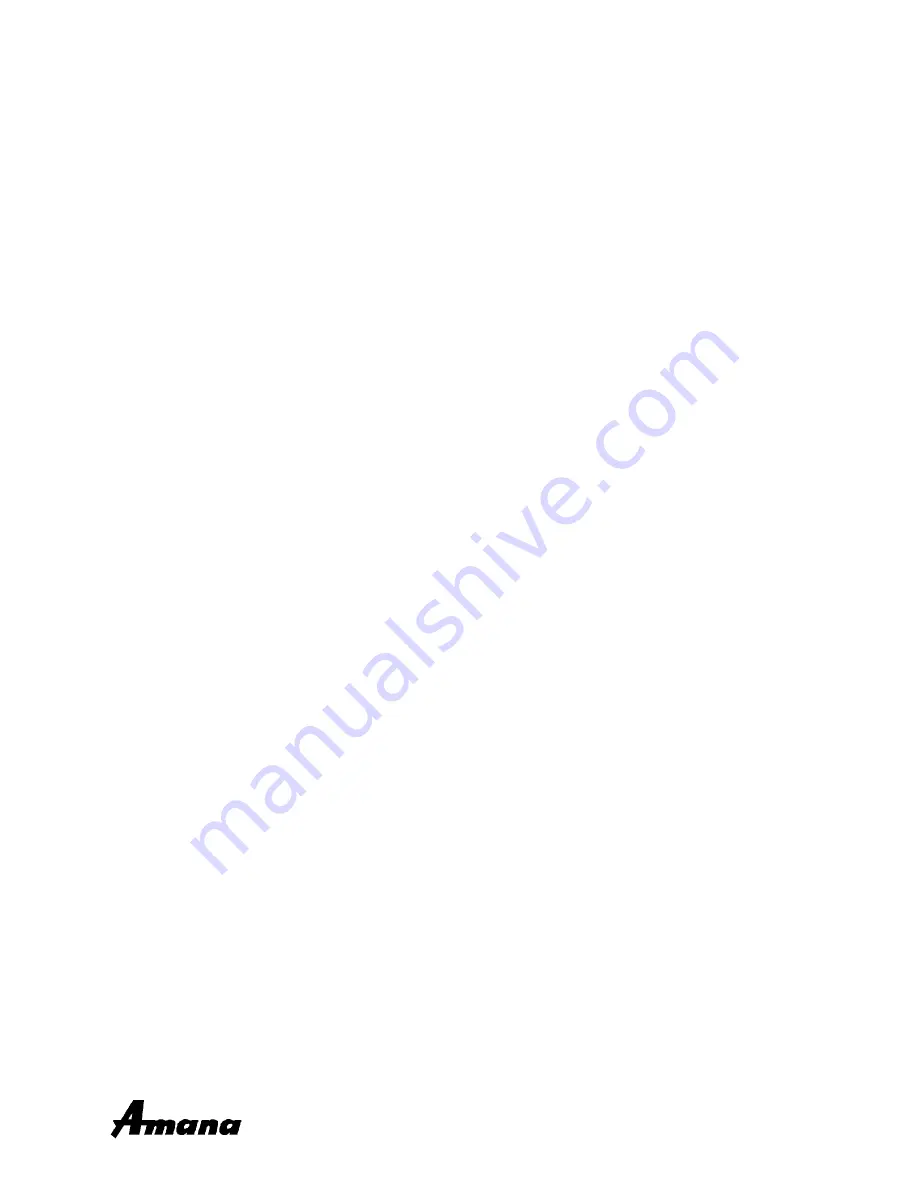
Service
Refer to Technical Information for
values and wiring schematics.
This manual is to be used by qualified appliance technicians
only. Amana does not assume any responsibility for property
damage or personal injury for improper service procedures done
by an unqualified person.
RS5280001
Revision 0
September 2001
“V” Model International
Top Mount Refrigerators
Models and manufacturing
numbers in this manual
ATX 518 VW P1322503W W
HT600W P1322901W W
TR521VW P1322601W W
TR525VW P1322701W W
TW518VW P1322501W W
TX518VW P1322502W W