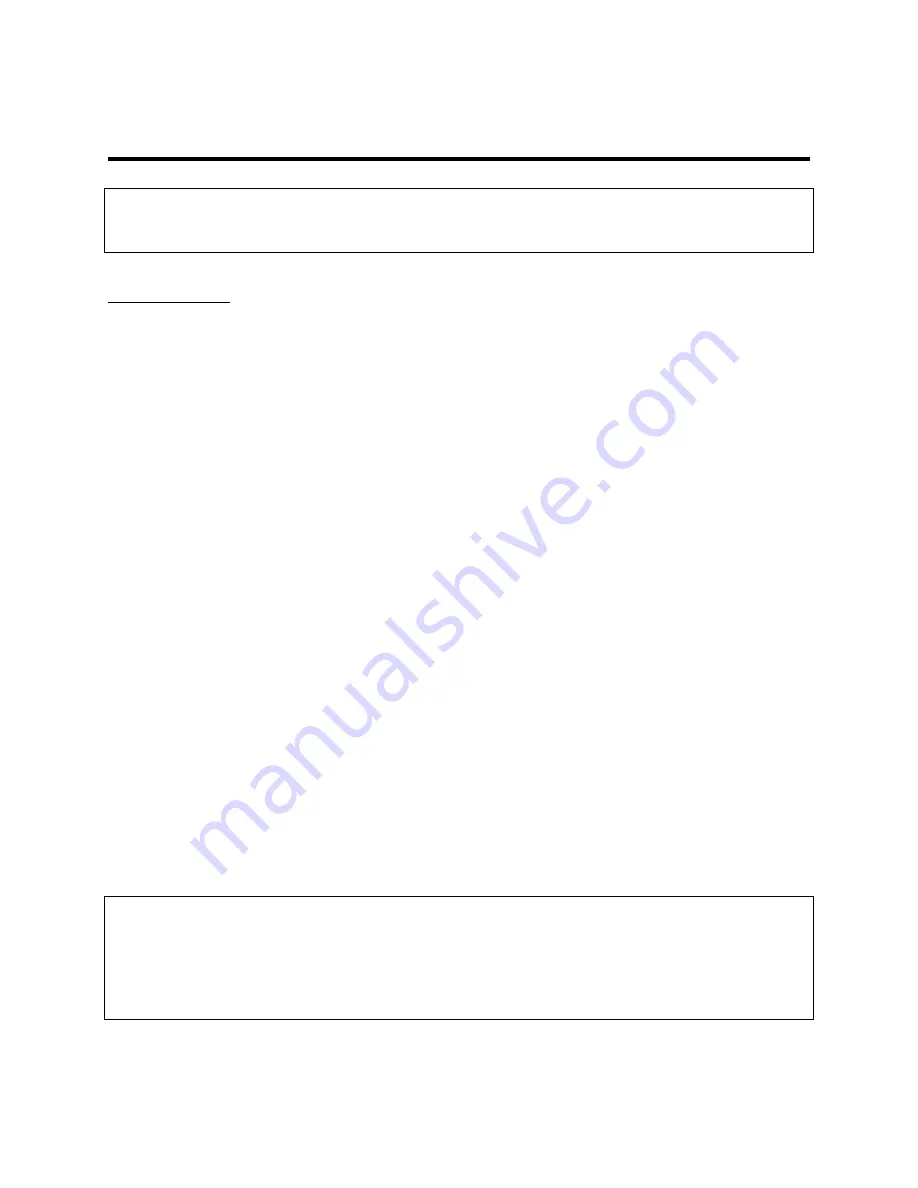
-1-
ALTRONIC CONTROLLER SYSTEM
INSTALLATION & OPERATING INSTRUCTIONS
MODEL DE-2500
FORM DE-2500 IOI 3-04
WARNING: DEVIATION FROM THESE OPERATING INSTRUCTIONS MAY LEAD TO
IMPROPER ENGINE/MACHINE OPERATION WHICH COULD CAUSE PERSONAL
INJURY TO OPERATORS OR OTHER NEARBY PERSONNEL.
1.0 OVERVIEW
1.1 For help locating subjects in this document, a section index is provided on page 57. A
glossary of technical terms is also provided which begins on page 52.
1.2 The Altronic DE-2500 controller system is an electronic, microprocessor-based system
designed to sense various analog and digital input points to control and monitor industrial
compressors. The system is field-programmable using a PC (personal computer) and the
supplied DE-2500 terminal program and contains a non-volatile memory to store the setup.
Serial communications provide an interface to PC’s, PLC’s, modems and satellite uplinks for
remote communication. A backlit 4x20 LCD character display shows system status,
programmed engine/motor and compressor parameters and channel labels. A front mounted
keypad serves as the user interface. The DE-2500 provides for both the safety shutdown
functions needed to prevent unnecessary damage to remote operated equipment and the
closed loop automatic control functions needed to optimize their efficiency of operation.
Additionally, the DE-2500 provides for remote data acquisition and supervisory control in a
compact, low cost package dedicated to industrial compressor applications. The optimization
strategies available for the management of compressor throughput include automatic prime
mover speed setting as well as capacity control. On rotary screw compressors, capacity
control can be done via suction throttling, or using an internal gas bypass technique
employing poppet valves, turn valves or slide valves. On reciprocating compressors, capacity
can be controlled using external gas bypass loops or pressure regulation techniques. A wide
range of output options, including both analog current loops and digital outputs, are provided
to interface with the large variety of actuation systems currently in use. In addition, automatic
load limiting based upon prime mover power capabilities or other application specific
limitations, such as cooling capacity, are readily implemented. There is also an AUTO START
option that is enabled using the terminal program.
1.3 The system consists of three main parts: a panel mounted Display Module DE-2500, a
Power Supply Module 691122-1, and a Terminal Module 691127-1. These components are
interconnected by means of Cable assembly 693115-1.
WARNING: THE CONTROLLER SYSTEM MUST BE CONFIGURED PRIOR TO USE ON A
COMPRESSOR SYSTEM. REFERENCE DE-2500 PI PROGRAMMING
INSTRUCTIONS, FOR INSTRUCTIONS DESCRIBING HOW TO CONFIGURE THE
CONTROLLER FOR THE SPECIFIC APPLICATION. VERIFY THE PROGRAM IN
NONVOLATILE MEMORY (THE EEPROM) PRIOR TO STARTING THE SYSTEM.
REFER TO SECTION 10.0 ON HOW TO VIEW THE CURRENT CONFIGURATION.