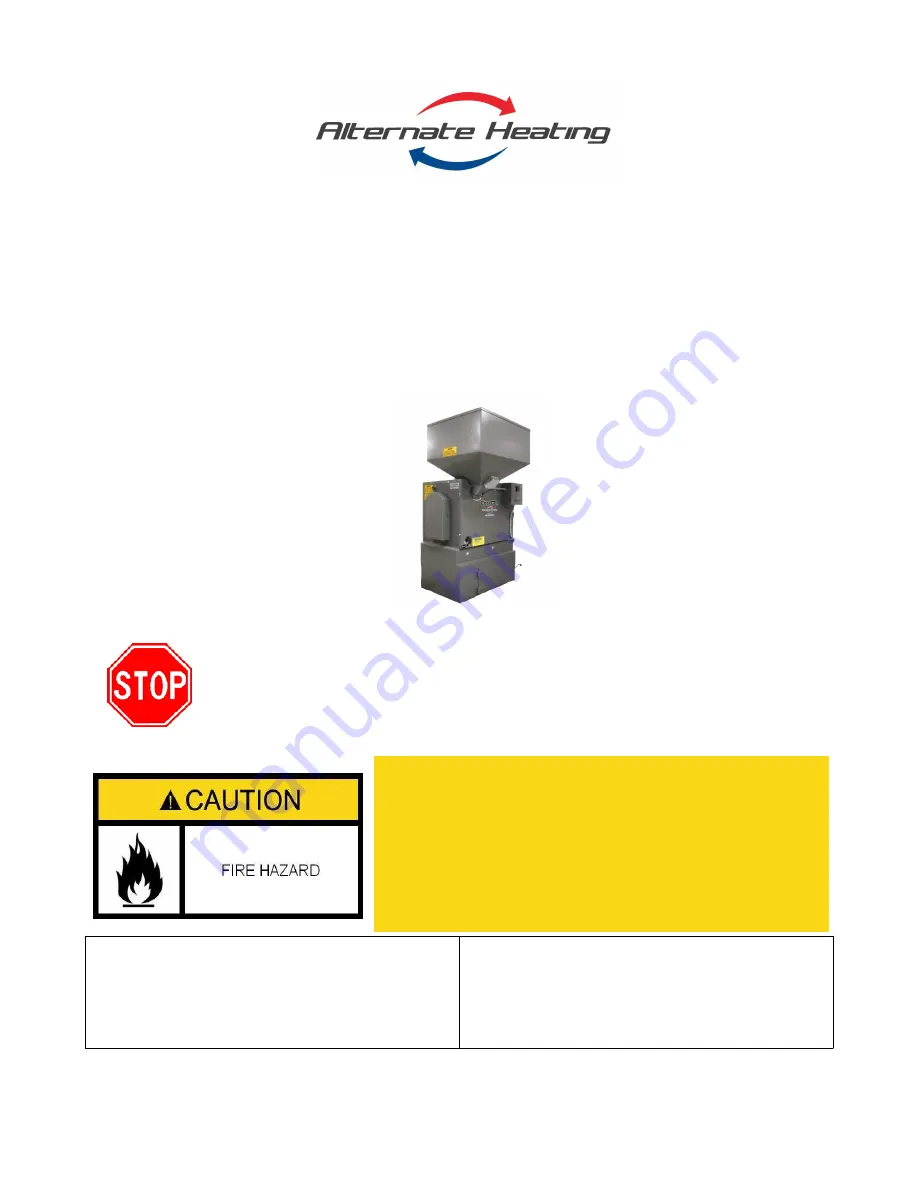
INSTALLATION AND
OPERATOR’S MANUAL
COAL GUN™ BOILER
Models: S130 • S260
IMPORTANT
: IN ORDER TO ACHIEVE SAFE AND SATISFACTORY
RESULTS FROM YOUR ALTERNATE HEATING SYSTEMS BOILER, READ
SAFETY RULES AND INSTRUCTIONS CAREFULLY BEFORE
INSTALLING AND OPERATING. ALL INSTALLATIONS MUST BE IN
ACCORDANCE WITH STATE AND LOCAL CODES. SAVE THESE
INSTRUCTIONS FOR FUTURE REFERENCE.
Your Alternate Heating Systems Boiler is capable of generating
very hot temperatures. Boiler temperatures and flames in the
ignition box area are capable of causing ignition or explosion of
explosive or flammable products or explosion of the boiler itself if
maximum safe water temperature is exceeded. Maximum safe
water temperature is 210° Fahrenheit. Flammable or explosive
products must never be stored in the same room or in the vicinity
of a boiler, and the boiler water temperature must never be
allowed to exceed 210° Fahrenheit.
ALTERNATE HEATING SYSTEMS
2393 LITTLE EGYPT RD
HARRISONVILLE, PA 17228
717-987-0099
WWW.ALTERNATEHEATINGSYSTEMS.COM
EMAIL: [email protected]
Record Model and Serial Number Below:
Model:
Serial Number:
Date of Purchase:
REV 170126
Summary of Contents for COAL GUN S130
Page 2: ......
Page 4: ......
Page 34: ...Appendix A Boiler Specification Diagrams 28 ...
Page 35: ... 29 ...
Page 37: ...Appendix B Wiring Diagrams 31 ...
Page 38: ... 32 ...
Page 39: ... 33 ...
Page 40: ...Appendix C Exploded Parts Drawing 34 ...
Page 51: ...Appendix E Troubleshooting Guide 45 ...
Page 54: ...Appendix F Table of Figures 48 ...
Page 57: ...Appendix H Dump Zone Wiring Applications 51 ...
Page 58: ... 52 ...
Page 59: ... 53 ...
Page 60: ... 54 ...
Page 61: ... 55 ...
Page 62: ... 56 ...