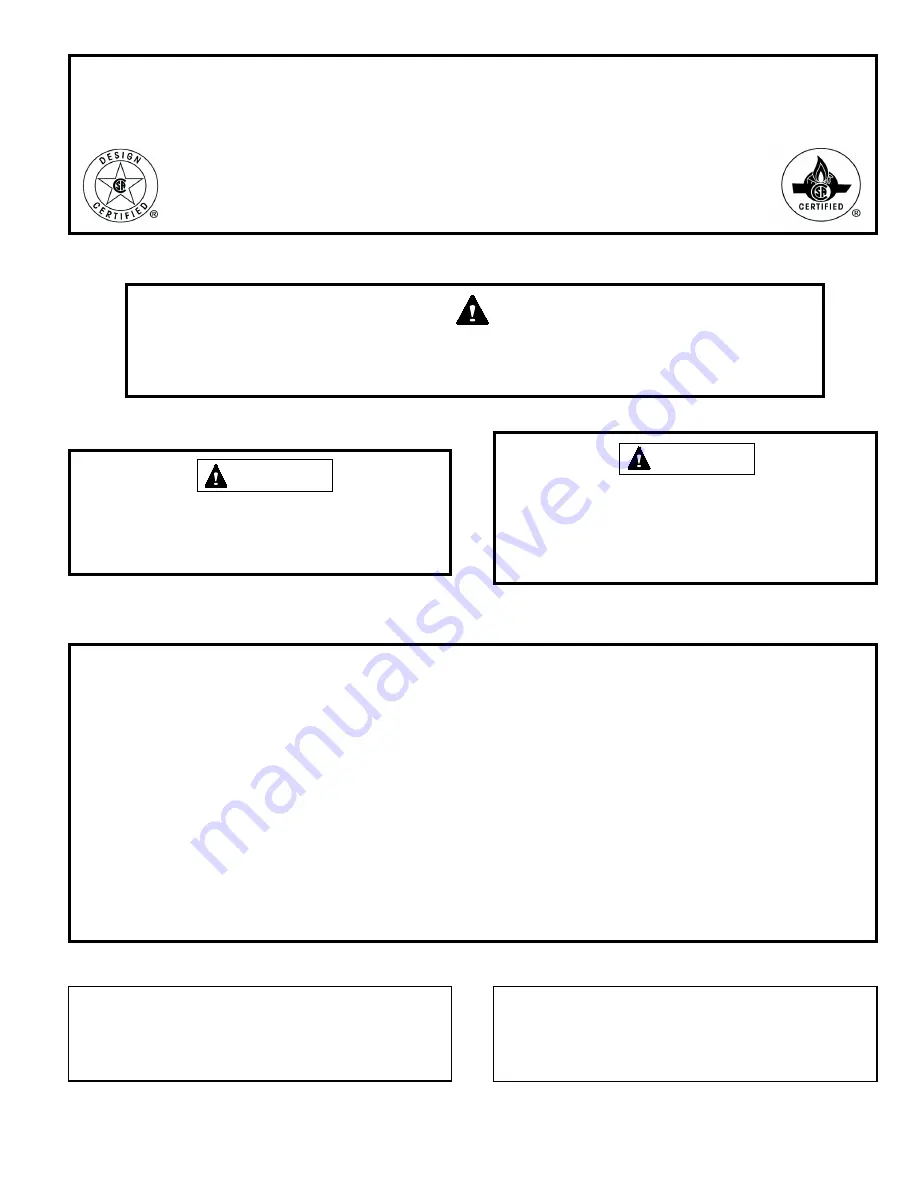
507276-03
Page 1 of 59
Issue 1621
This is a safety alert symbol and should never be ignored. When you see this symbol on labels or in
manuals, be alert to the potential for personal injury or death.
Manufactured By
Allied Air Enterprises LLC
A Lennox International, Inc. Company
215 Metropolitan Drive
West Columbia, SC 29170
(P) 507276-03
This manual must be left with the homeowner for future reference.
INSTALLATION INSTRUCTIONS
A95UH1E & 95G1UHE
Warm Air Gas Furnace
Upflow/Horizontal Left and Right Air Discharge
TABLE OF CONTENTS
As with any mechanical equipment, personal injury can
result from contact with sharp sheet metal edges. Be
careful when you handle this equipment.
CAUTION
Improper installation, adjustment, alteration, service
or maintenance can cause property damage, personal
injury or loss of life. Installation and service must
be performed by a licensed professional installer (or
equivalent), service agency or the gas supplier.
WARNING
*P507276-03*
Unit Dimensions ................................................................ 2
Parts Arrangement............................................................. 3
Gas Furnace ...................................................................... 4
Shipping and Packing List ................................................. 4
Safety Information ............................................................. 4
Use of Furnace as a Construction Heater
General ............................................................................ 6
Combustion, Dilution & Ventilation Air ............................... 6
........................................................... 10
Filters .......................................................................... 14
Duct System .................................................................... 14
Pipe & Fittings Specifications
.......................................... 14
Joint Cementing Procedure ............................................. 16
Venting Practices ............................................................. 17
Vent Piping Guidelines .................................................... 18
Gas Piping ....................................................................... 39
Electrical .......................................................................... 42
Unit Start-Up .................................................................... 45
Gas Pressure Adjustment ................................................ 47
................................................. 47
Other Unit Adjustments.................................................... 50
.............................................. 51
Service .......................................................................... 53
Planned Service .............................................................. 55
Diagnostic Codes ............................................................ 55
Repair Parts List .............................................................. 56
Start-Up & Performance Check List ................................ 57
Summary of Contents for 95G1UHE
Page 3: ...507276 03 Page 3 of 59 Issue 1621 EXPANDED VIEW Figure 1 ...
Page 22: ...507276 03 Page 22 of 59 Issue 1621 Figure 25 Figure 26 ...
Page 28: ...507276 03 Page 28 of 59 Issue 1621 Figure 34 ...
Page 38: ...507276 03 Page 38 of 59 Issue 1621 Figure 57 Trap Drain Assembly Using 1 2 PVC or 3 4 PVC ...
Page 40: ...507276 03 Page 40 of 59 Issue 1621 Figure 59 Figure 60 ...
Page 44: ...507276 03 Page 44 of 59 Issue 1621 TYPICAL WIRING DIAGRAM Figure 65 ...
Page 57: ...507276 03 Page 57 of 59 Issue 1621 Start Up Performance Check List ...