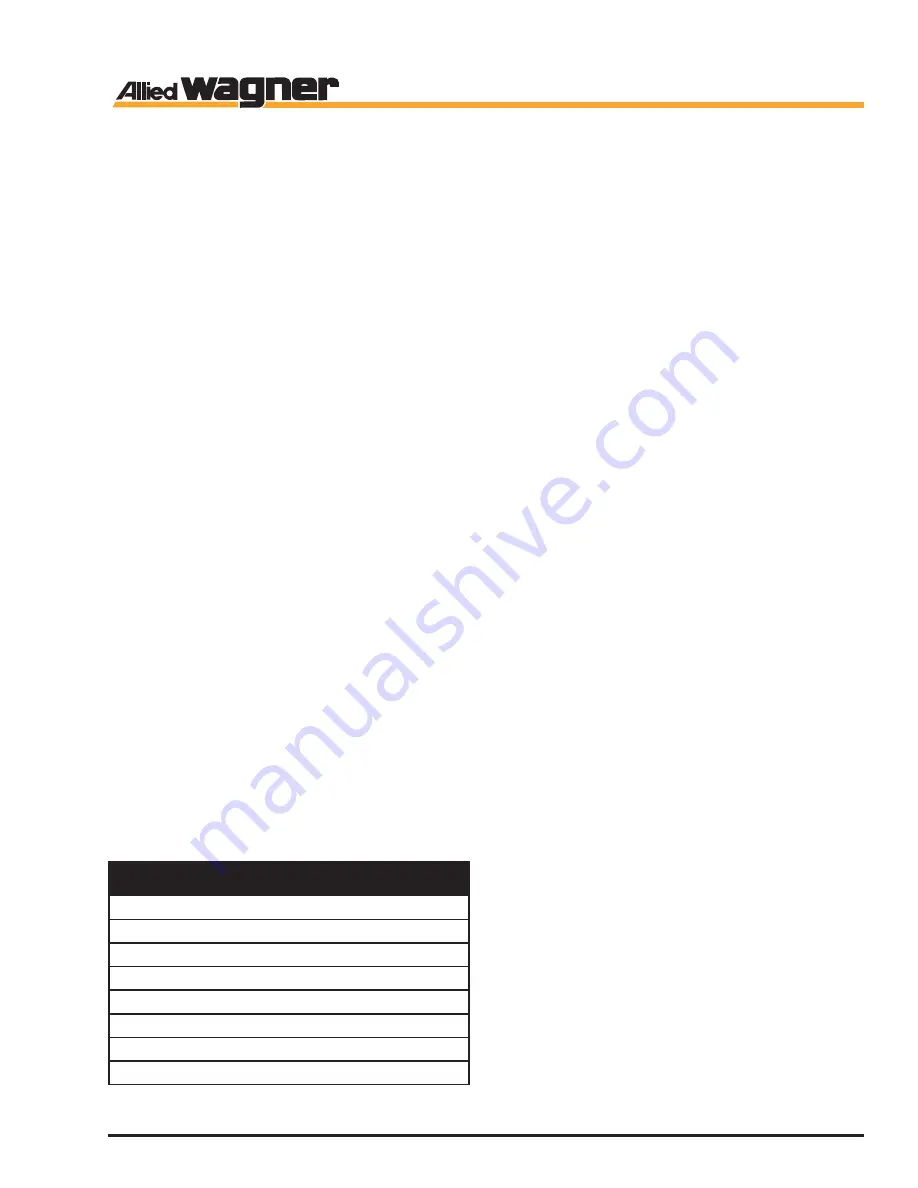
1
80-1056
Rev: 8-2014
Vehicle Monitor Kit Installation Instructions
Part Number 591004
Section
9-1
Table 1
Required Tools List
Unpacking
Immediately upon receiving the kit, it should be un-
packed, and an inventory taken. See Figure 1 for a list
of items that should be included. Report any missing
items to Allied Systems Company (503.625.2560)
immediately.
Installation
The figures in this document illustrate this kit mounted
on a CHD100 Chipdozer. This kit will install on many
different models of Wagner equipment. Your installa-
tion may vary.
Important: Read entire instructions prior to install-
ing this kit, and make sure you understand them.
If you have any questions, contact Allied Systems
Service department at 503-625-2560.
1. Park the machine on level ground, and lower the
carriage or bucket to the ground. Shut off the
machine, employ work site lockout/tagout proce-
dures, and disconnect the battery at the switch.
Refer to your operator’s manual if necessary.
2. Please document the serial number located on the
back of the vehicle monitor unit
here: ______________. You will need to contact
your dealer or Allied Systems Company to acti-
vate your service and will need to reference both
the monitoring system’s serial number and the
vehicle’s serial number in order to do so. Please
call for activation 24-hours prior to installation so
service can be activated with the service supplier.
3. The kit includes four terminal blocks. Three of
these four 4-position terminal blocks replace exist-
ing 2-position terminal blocks. The fourth does not
replace any existing terminal block, but should be
mounted near the other three if possible.
4. The existing terminal blocks to be replaced will
typically be inside the console assembly (Chipdoz-
ers), or in the terminal panel assembly (Logstack-
ers).
5. These four terminal blocks are labeled “A”, “B”,
“C”, and “D” in
Figure 2
. To determine which
existing terminal blocks to replace for the blocks
labeled “B” and “C”, you may need to temporarily
close the battery disconnect switch to test for volt-
age at the terminal block. Make sure to disconnect
the battery at the switch again before disconnect-
ing any wires or removing any terminal blocks.
Terminal A:
This terminal block does not replace
any existing terminal block. Mount near the other
terminal blocks if possible.
Terminal B:
This terminal block replaces an exist-
ing 2-position terminal block. Refer to the electri-
cal schematic for your machine. Find an existing
2-position terminal block that connects to the
unswitched power and the BATT terminal on the
ignition switch. This terminal block should be ener-
gized (24 VDC) regardless of keyswitch position.
Disconnect and tag the wires from this terminal
block, and remove it. Replace with a 4-position
terminal block (“B” on
Figure 2
).
Terminal C:
This terminal block replaces an
existing 2-position terminal block. Refer to the
electrical schematic for your machine. Find an
existing 2-position terminal block that connects
to RUN on the ignition switch. This terminal block
should be energized (24 VDC) when the keyswitch
is on, and not energized when off. Disconnect and
tag the wires from this terminal block, and remove
it. Replace with a 4-position terminal block (“C” on
Figure 2
).
Terminal D:
This terminal block replaces an exist-
ing 2-position terminal block. Refer to the electri-
cal schematic for your machine. Find an existing
2-position terminal block that connects to the
chassis ground. Disconnect and tag the wires from
this terminal block, and remove it. Replace with a
4-position terminal block (“D” on
Figure 2
).
Required Tools
Drill
Flat and Phillips screw drivers with magnetic tips
Small drill bit set
Wire cutters
Wire strippers
Wire crimp
Crescent wrench - 8”
Open end wrench - 3/8” and 3/4”