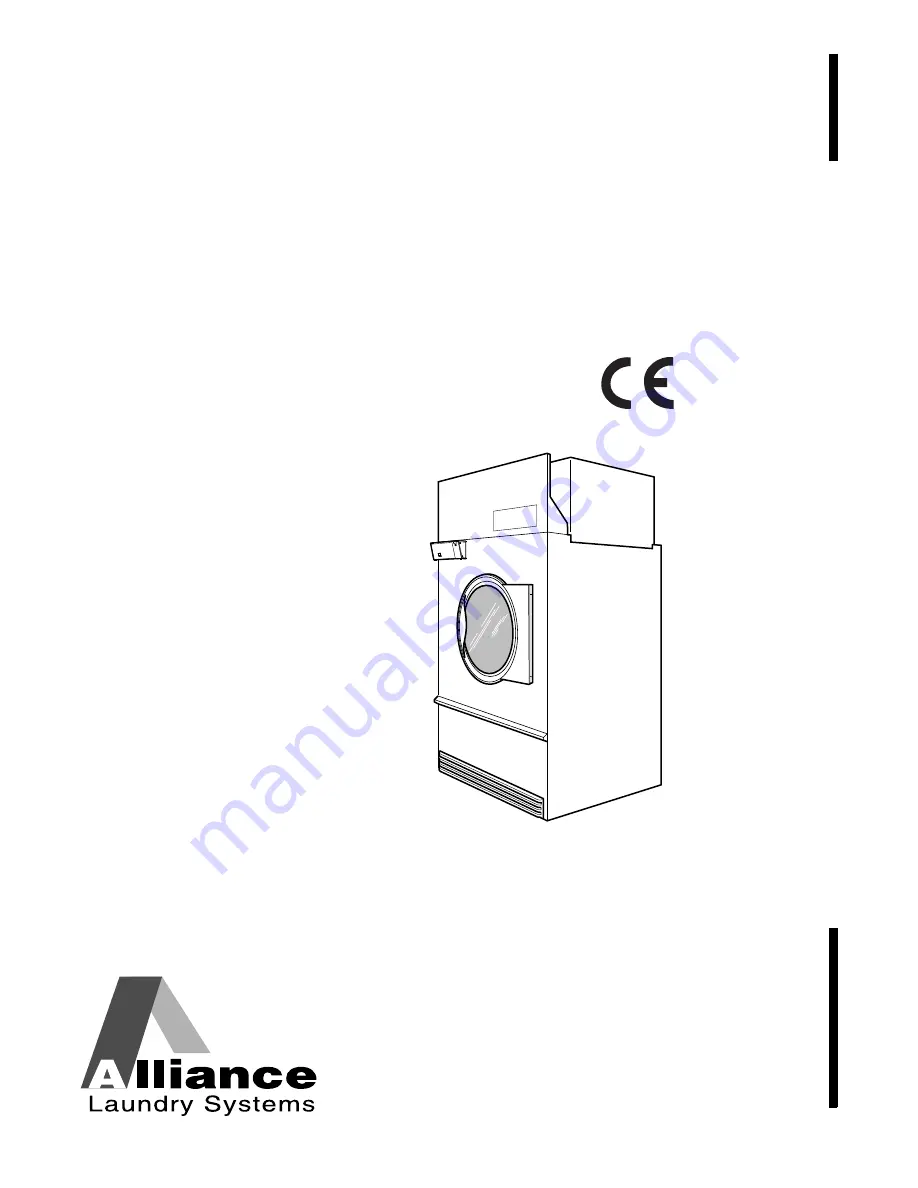
Installation/Operation/Maintenance
www.alliancelaundry.com
Tumble Dryers
54 Kilogram (120 Pound) Capacity
77 Kilogram (170 Pound) Capacity
91 Kilogram (200 Pound) Capacity
Starting Serial No. 0907003062
Refer to Page 6 for Model Identification
TMB1268C
Part No. 70458101ENR3
March 2013
Original Instructions
Keep These Instructions for Future Reference.
(If this machine changes ownership, this manual must accompany machine.)
TMB1268C