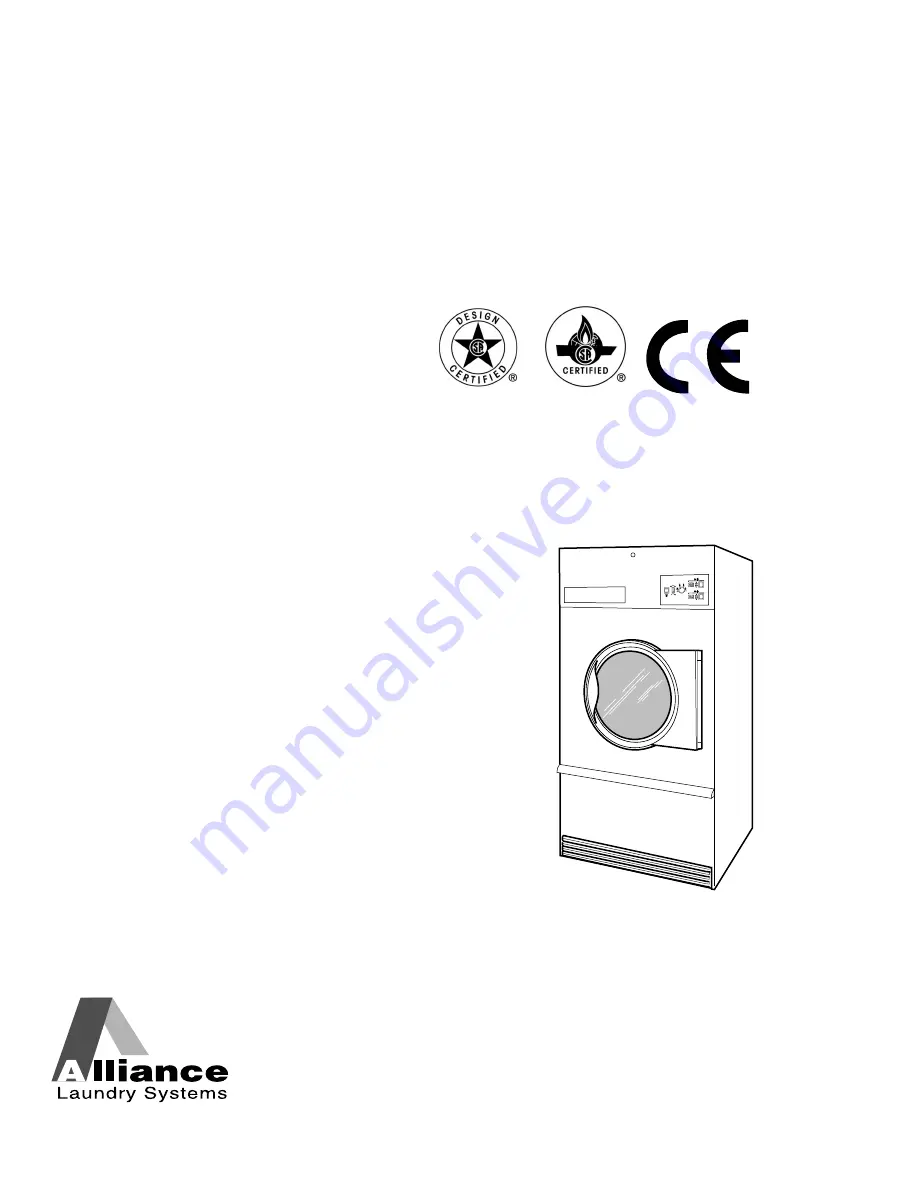
Installation/Operation/Maintenance
Tumble Dryers
50 Pound (25 Kilogram) Capacity
75 Pound (34 Kilogram) Capacity
Starting Serial No. 0904004427
Refer to Page 9 for Model Identification
TMB1277C_SVG
Original Instructions
Keep These Instructions for Future Reference.
(If this machine changes ownership, this manual must accompany machine.)
www.alliancelaundry.com
Part No. 70457901ENR12
September 2015
Summary of Contents for YU050E
Page 2: ......