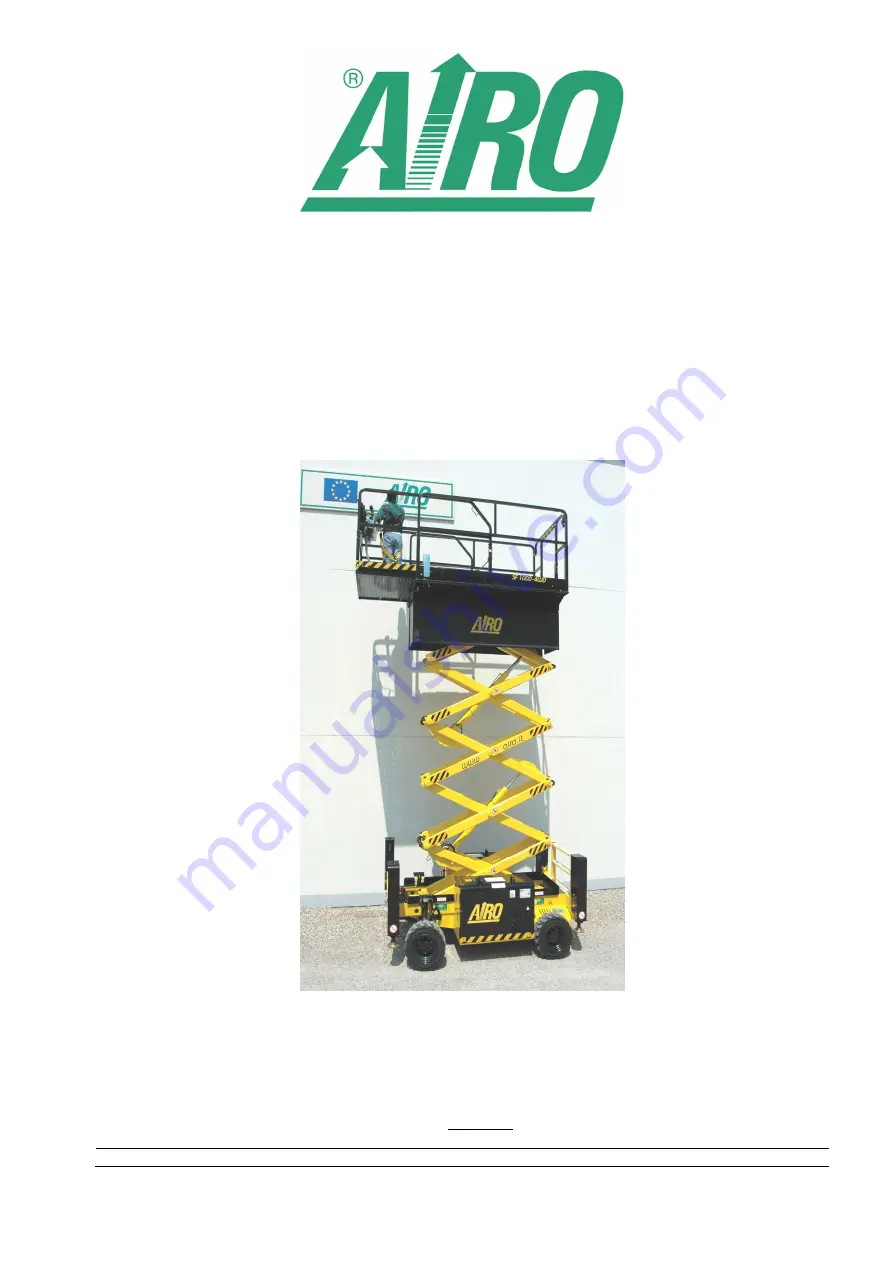
PIATTAFORME AEREE SEMOVENTI
SELF-PROPELLED WORK-PLATFORMS
PLATES-FORMES DE TRAVAIL AUTOMOTRICES
SELBSTFAHRENDE HUBARBEITSBÜHNEN
PLATAFORMAS ELEVADORAS AUTOPROPULSADAS
ZELFRIJDENDE HOOGWERKERS
SJÄLVGÅENDE ARBETSPLATTFORMAR
SAMOKRETNE RADNE PLATFORME
“SF” SERIES
SF820-4WD SF1000-4WD
USE AND MAINTENANCE MANUAL
- ENGLISH -
AIRO
is a division of
TIGIEFFE SRL
Via Villasuperiore , 82 -42045 Luzzara (RE) ITALIA-
'
+39-0522-977365 -
7
+39-0522-977015
WEB: www.airo.it
026.20.UEM-EN
03-2008