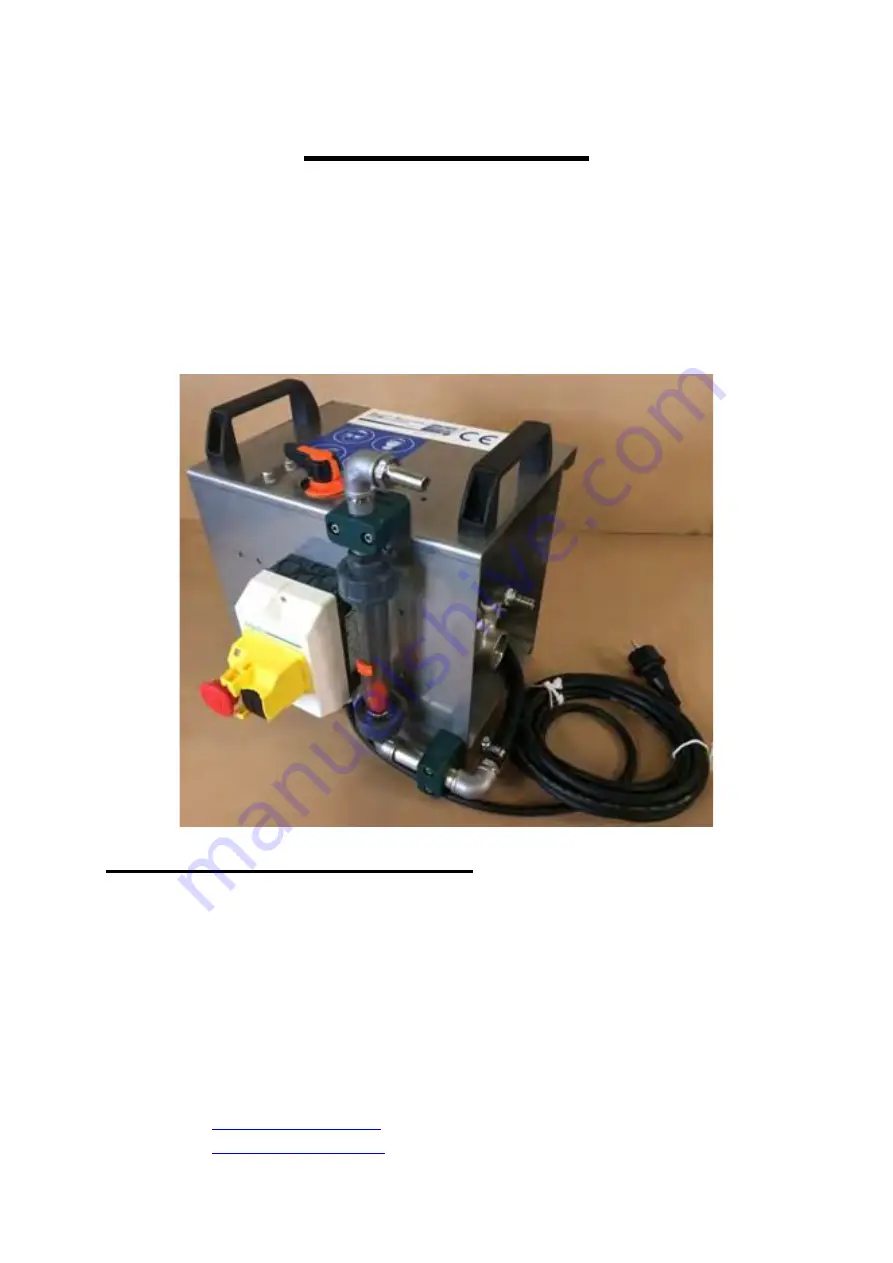
Page 1 of 17
User Manual
Standard 400/600/950 E
(Article No. 150-00)
(Article No. 150-00-06)
(Article No. 150-00-08)
Version as of 06/2020
Consulting, Production & Sales:
Ahlmer Maschinen & Gerätebau
GmbH & Co. KG
Schildarpstraße 20
D - 48712 Gescher
Germany
Tel.: +49 (0) 25 42 917917-0
Fax: +49 (0) 25 42 917917-29
Website:
Email: