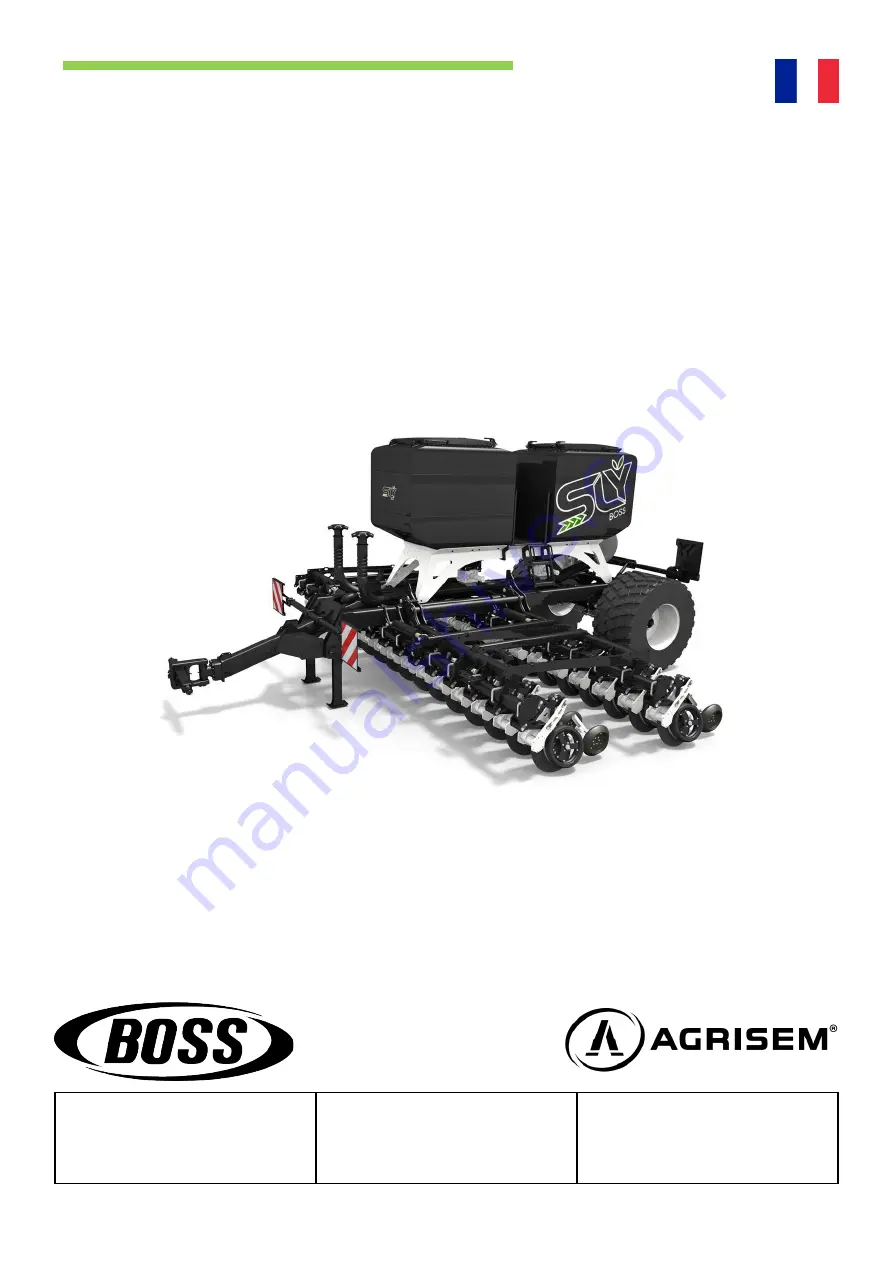
USER MANUAL
BOSS SEED DRILL
Telephone : +33 (0) 2 51 14 14 40
Mail : [email protected]
Manual: NOTT-FR-800-A
AGRISEM
535 Rue Pierre Levasseur
CS 60263
44158 ANCENIS - FRANCE
Summary of Contents for Big Boss
Page 73: ...73 12 5 1 3 Icons ...