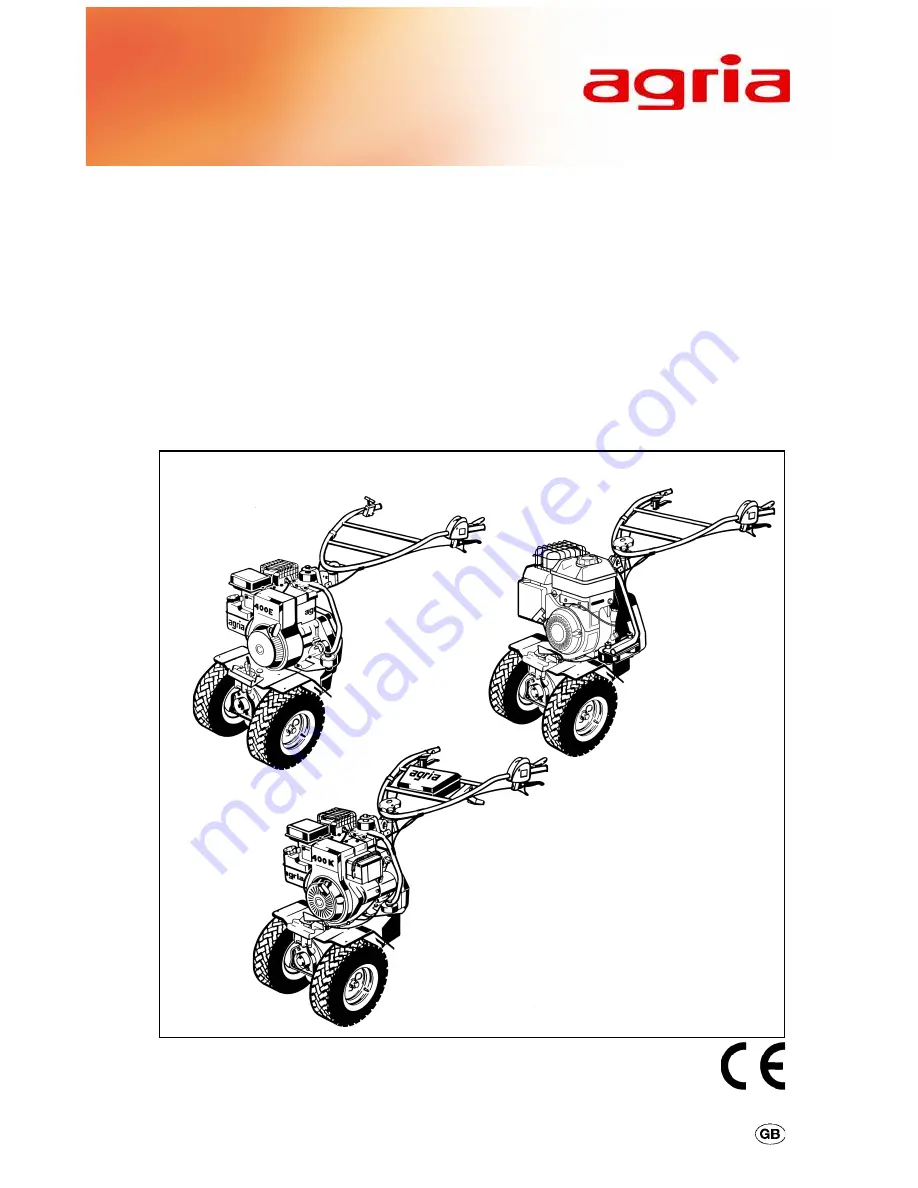
Before commissioning the machine, read operating
instructions and observe warnings and safety instructions.
Operating Instructions No. 998 702-C 01.10
&
Briggs&Stratton engine
Multi-Purpose Machine
Multi-Purpose Machine
Multi-Purpose Machine
Multi-Purpose Machine
Multi-Purpose Machine
400E and 400K
400E and 400K
400E and 400K
400E and 400K
400E and 400K
Original
Original
Original
Original
Original
Operating
Operating
Operating
Operating
Operating
Instructions
Instructions
Instructions
Instructions
Instructions
3348, 5117, 3346
Summary of Contents for 400E
Page 6: ...6 agria Multi Purpose Machine 400E 400K ...
Page 7: ...agria Multi Purpose Machine 400E 400K 7 C D Designation of Parts Type 400K ...
Page 55: ...agria Multi Purpose Machine 400E 400K 55 5 ...
Page 60: ...60 agria Multi Purpose Machine 400E 400K ...
Page 62: ...62 agria Multi Purpose Machine 400E 400K E F Designation of Parts Type 400E ...
Page 63: ...agria Multi Purpose Machine 400E 400K 63 ...
Page 66: ...66 agria Multi Purpose Machine 400E 400K G H Designation of Parts Type 400K ...
Page 67: ...agria Multi Purpose Machine 400E 400K 67 EC Declaration Conformity ...