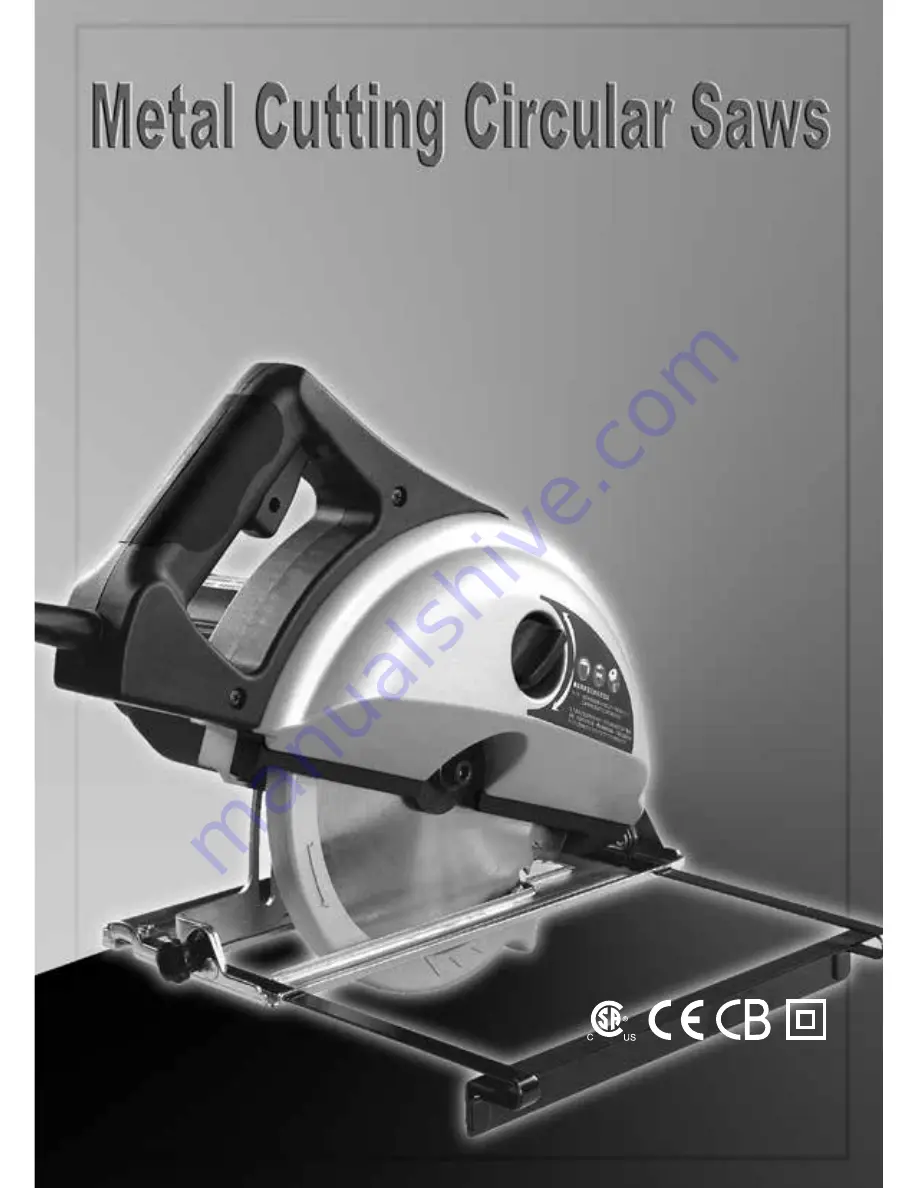
ORIGINAL INSTRUCTIONS
For your personal safety, READ and
UNDERSTAND before using
.
SAVE THESE INSTRUCTIONS FOR
FUTURE REFERENCE.
Warning:
Only tools equipped with over load protection, when motor has been cut off due to over
load, always switch on machine with no load for at least 3 minutes to reduce temperature
before switch on again to avoid burn out to the motor.
Version:20130603
Summary of Contents for CS200
Page 13: ...13 WIRING ij IJ IJ ij AC SWITCH CARBON BRUSH CARBON BRUSH MOTOR OVERLOAD RED BLACK WHITE ...
Page 18: ......
Page 19: ......
Page 20: ......