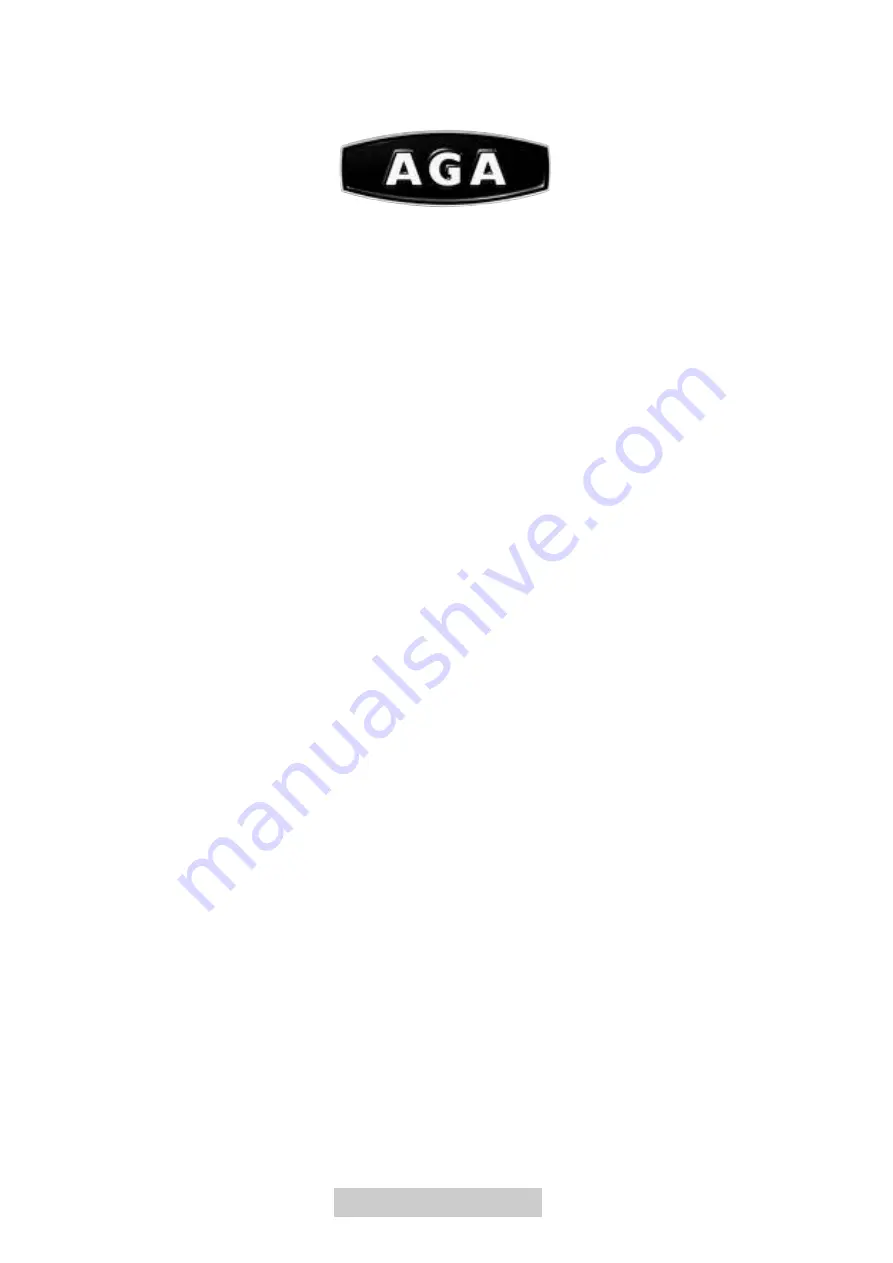
AGA DUAL CONTROL
Model No’s: DC3G & DC5G
Installation
Guide
06/15 EINS 516911
PLEASE READ THESE INSTRUCTIONS BEFORE COMMENCING SITE SURVEY
OR INSTALLING THIS APPLIANCE.
IMPORTANT :
SAVE INSTRUCTIONS FOR FUTURE REFERENCE
IMPORTANT :
CONSERVER CES INSTRUCTIONS POUR REFERENCE FUTURE
For use in USA/Canada
Summary of Contents for DC3G
Page 17: ...Fig 10 DESN 516850 17 ...
Page 19: ...WIRING DIAGRAM AGA DC3G Fig 12 19 ...
Page 33: ...33 ...
Page 34: ...34 ...
Page 35: ...35 ...