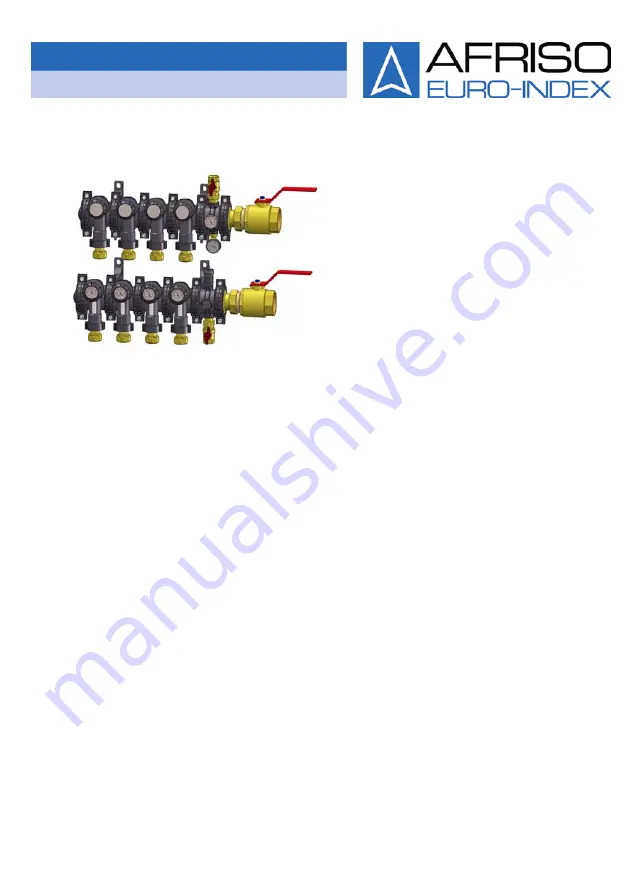
Mess-, Regel- und
Überwachungsgeräte
für Haustechnik,
Industrie und Umweltschutz
Lindenstraße 20
74363 Güglingen
Telefon +49 7135 102-0
Service +49 7135-102-211
Telefax +49 7135-102-147
[email protected]
www.afriso.de
Read instructions before using device!
Observe all safety information!
Keep instructions for future use!
12.2013 0
854.001.0692
Operating instructions
Brine / heating circuit manifold
ProCalida
®
GT 3
# 81704