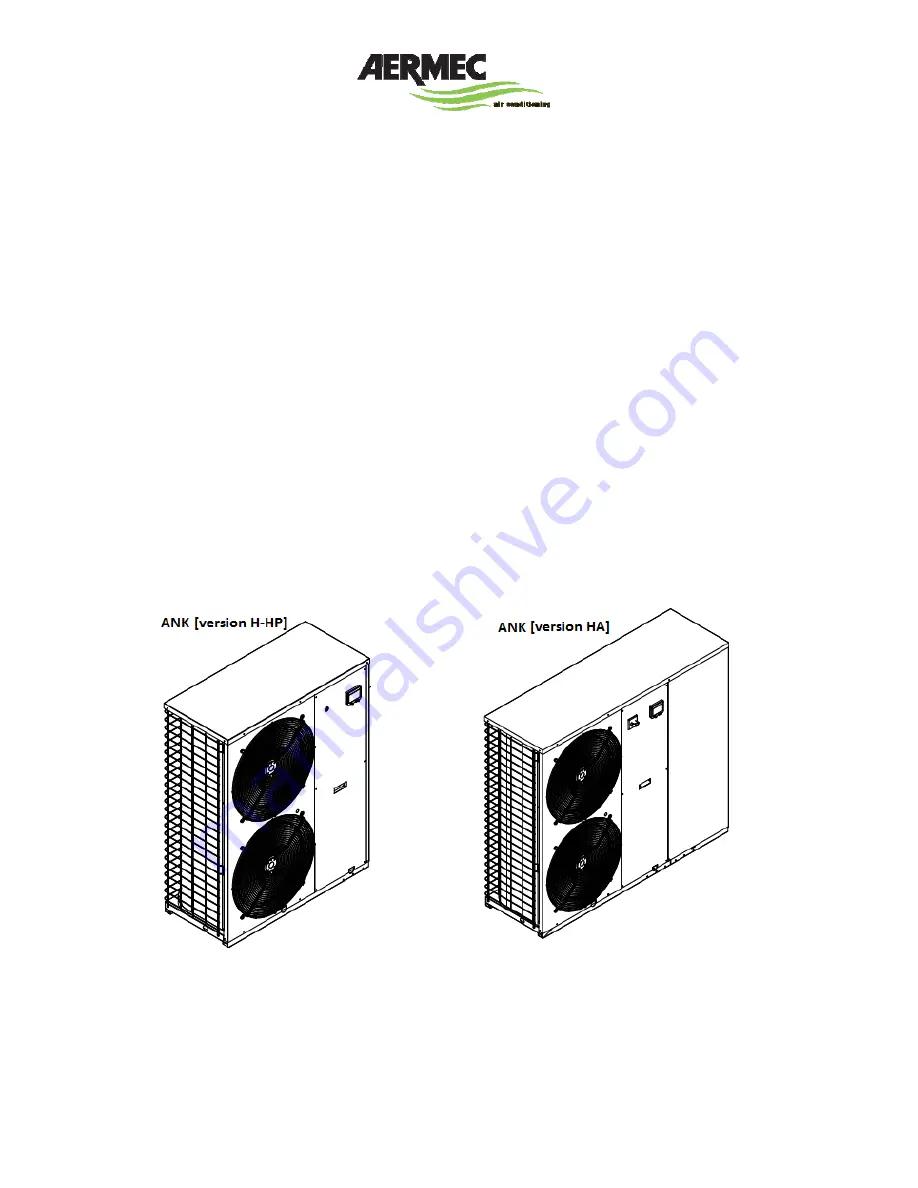
1. INSTALLATION REQUIREMENTS
…………………....….2
1.1. TOOLS AND PARTS…………………………………………………...…..2
1.2. SYSTEM REQUIRMENTS…………………………………………..……..2
1.3. LOCATION REQUIREMENTS………………………….………………..2
1.4 MINIMUM WATER VOLUME…………………………………………….2
1.5. MINIMUM CLEARANCE…………………………………………………2
1.6 ELECTRICAL REQUIREMENTS………………………………………….3
2. INSTALLATION INSTRUCTIONS
………………….……...4
2.1 HYDRONIC CONNECTIONS………………………………………….4
2.2. ELECTRICAL CONNECTIONS………………………………………..5
2.2.1CABLE…………………………………………………………………..5
2.2.2. CONNECTING POWER SUPPLY…………………… ..……………5
3. TERMINAL BOARD CONNECTIONS
…………………..6
4. CONTROLS AND COMMISSIONING
…………………...6
4.1. PREPARATION FOR COMMISSIONING…………………………….6
4.2. MACHINE COMMISSIONING………………………….………...…....7
4.3. SEASON CHANGOVER……………………………..................................7
5. OPERATION
5.1. SET POINT IN COOLING MODE……………………………....7
5.2. SET POINT IN HEATING MODE……………………………....7
5.3. COMPRESSOR START-UP DELAY………………………...…....7
5.4. CIRCULATION PUMP…………………………………………...7
5.5.FAN SPEED CONTROL……………………………………….....7
5.6. ANTI-FREEZE ALARM……………………………........................7
5.7. WATER FLOW RATE ALARM……………………………...........8
6. MAINTENANCE
…………………………………………....8
6.1. HYDRAULIC CIRCUIT…………………………….........................8
6.2. ELECTRICAL CIRCUIT CHECKS…………………………….....8
6.3. COOLING CIRCUIT CHECKS……………………………...........8
6.4. MECHANICAL CHECKS………………………………………...8
6.5.REFRIGERANT LOAD PROCEDURE………..………………....8
7. LIST OF CONTROLS……………………………….……………....9
8. TROUBLESHOOTING
……………………………...…...11
WIRING DIAGRAM
…………………………….........................12
WARRANTY
……………………………...........................................13
ANK INSTALLATION MANUAL
NORTH AMERICAN REVISION
Table of contents
GENERAL WARNING FOR THE INSTALLER
The
chiller
must
be
installed
by
a
qualified
and
trained
technician.
AERMEC
will
not
assume
any
responsibility
for
damage
due
to
failure
to
follow
these
instructions.
Before
beginning
any
operation,
READ
THESE
INSTRUCTIONS
CAREFULLY
AND
CARRY
OUT
THE
SAFETY
CHECKS
TO
REDUCE
ALL
RISK
OF
DANGER
TO
A
MINIMUM.
All
the
staff
involved
must
have
thorough
knowledge
of
the
operations
and
any
dangers
that
may
arise
at
the
moment
in
which
the
installation
operations
are
carried
out.
Vers.
1.1.15