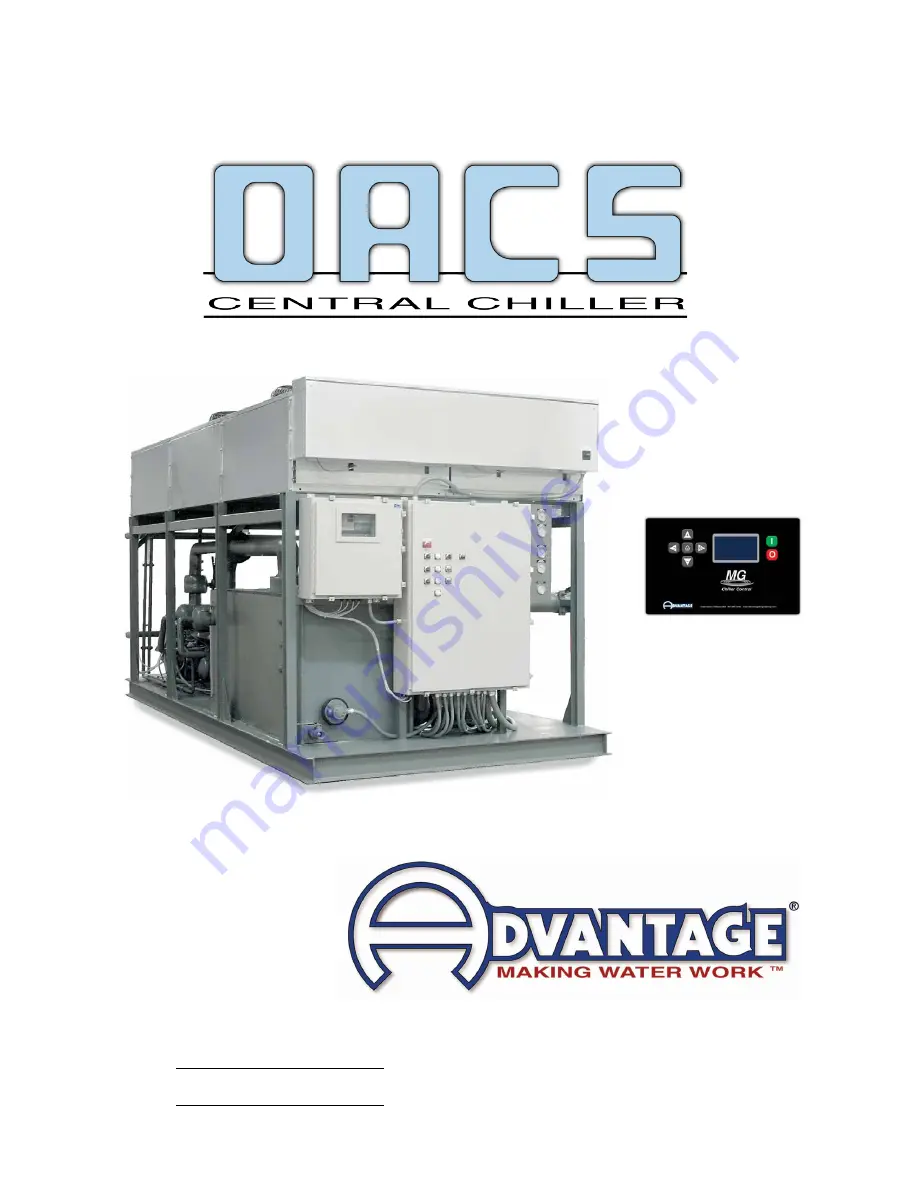
I.O.M. #167 updated 12/11/2019
INSTRUCTION MANUAL
• INSTALLATION • OPERATION • MAINTENANCE
ADVANTAGE ENGINEERING, INC.
525 East Stop 18 Road Greenwood, IN 46142
317-887-0729 fax: 317-881-1277
Service Department fax: 317-885-8683
www.AdvantageEngineering.com
E-mail [email protected]
Covering Models
From 20 - 210 Tons
Air-Cooled with MG
Control Instrument
Model:
Serial Number :
Summary of Contents for OACS Series
Page 2: ......
Page 6: ...Page 6 THIS PAGE INTENTIONALLY BLANK ...
Page 44: ...Page 44 THIS PAGE INTENTIONALLY BLANK ...
Page 72: ...Page 72 THIS PAGE INTENTIONALLY BLANK ...
Page 85: ...END 2019 ADVANTAGE ENGINEERING INC RE 20190822 ...
Page 86: ......