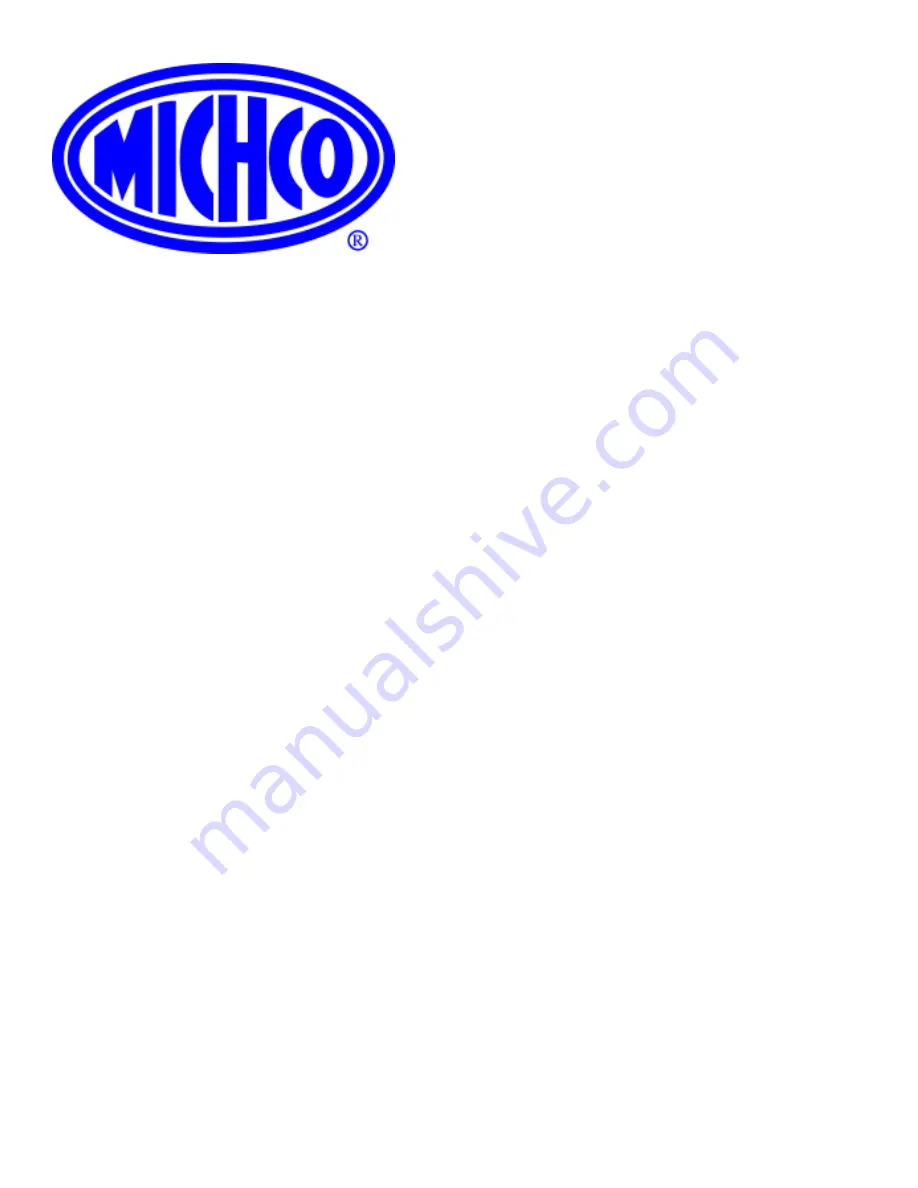
Electronic Service
Manuals
This electronic document is provided as a service to our customers.
We do not create the contents of the information contained in this docu-
ment. Should you have detailed questions pertaining to the information
contained in this document, you may contact Michco, or the manufac-
turer which provided the original information in this electronic deliver-
able. Michco’s only part in this electronic deliverable was the electronic
assembly process. By providing this manual on line we are not guaran-
teeing parts availability.
You may contact Michco through the following methods:
Phone (517) 484-9312 or (800) 331-3339
2011 N. High St. -- Lansing, Michigan -- 48906
Fax: (517) 484-9836
Email: [email protected]
Web site: www.Michco.Com
Parts Web site: www.FloorMachineParts.Com
Order Parts on Line at:
www.FloorMachineParts.Com
Directly to Parts & Service:
By Email:
By Fax: (517) 702-2041
By Voice: Use numbers above.
Serving the Cleaning Industry Since 1922
Notice: All copyrighted material remains property of original owners, all trademarks are property of respective owners.
Manuals are subject to Manufacturer’s reproduction limitations. Originals or reproductions were provided by manufacturers
through a request. We make no warranty as to the correctness of information provided in this document and you assume
all risk. By placing these manuals on line we are not declaring our corporation to be an manufacturer authorized dealer or
provider, please check our web site for authorized manufacturers we represent.
Summary of Contents for ADVANCE RS 501
Page 2: ...RS 501 Nilfisk 502 SERVICE MANUAL ENGLISH 33019746 2 2010 03...
Page 3: ......
Page 57: ...ENGLISH SERVICE MANUAL 54 33019746 2 2010 03 RS 501 STERZO...
Page 146: ......
Page 147: ......
Page 148: ......
Page 149: ......
Page 150: ......
Page 151: ......
Page 152: ......
Page 153: ......
Page 154: ......