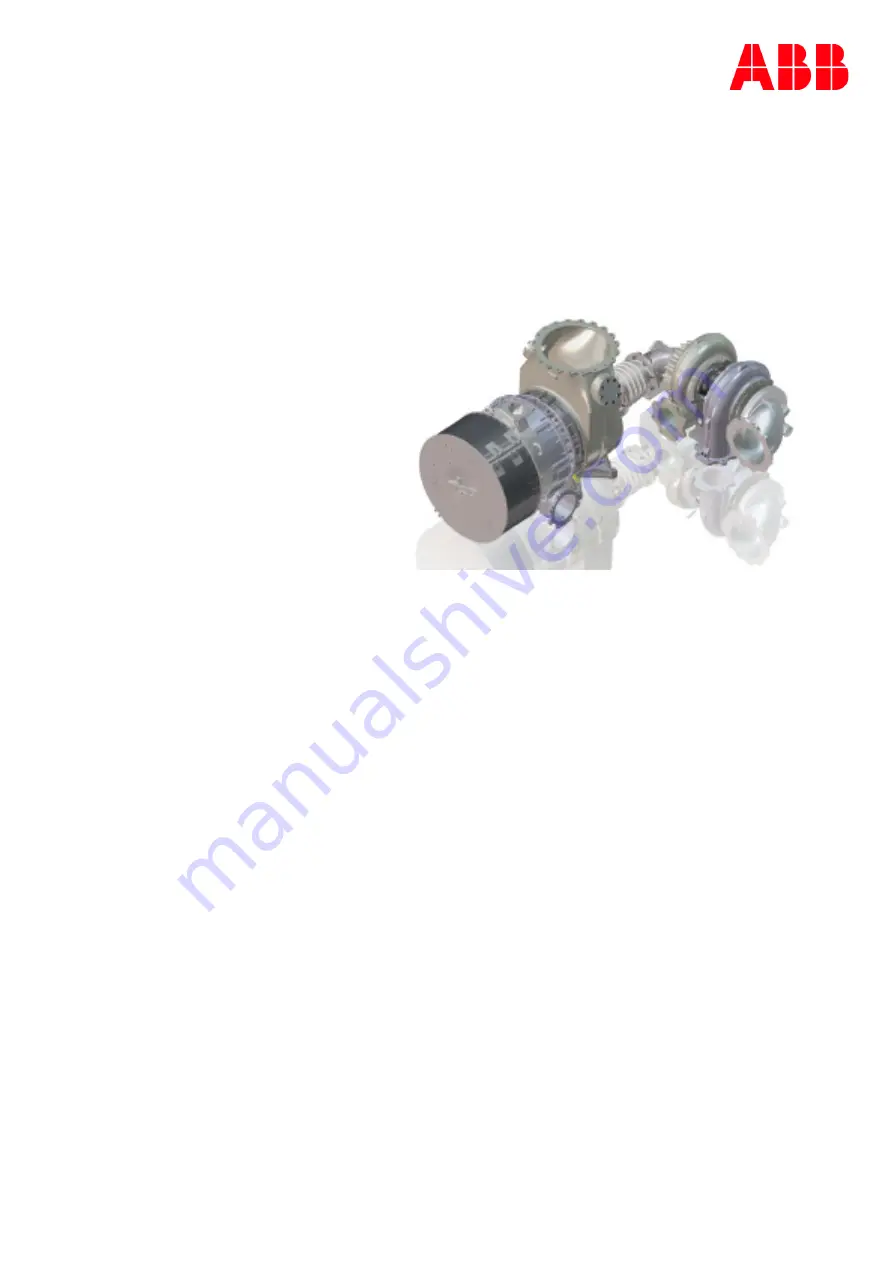
Turbocharger / A100-M radial
Original assembly instructions – English
This document is valid for the
Power2 series:
Power2 550-M
Purpose
The assembly instructions explain how the low-
and high-pressure stage of ABB Turbo
charging
is fitted to the engine correctly and without any
health and safety risks.
Target group
The assembly instructions are intended for
engineers and mechanics responsible for fitting
the low- and high-pressure stage on the engine.
Power2 performance package
Two-stage turbocharging solution for highest
turbocharging efficiency
—
ASSEMBLY INSTRUCTIONS
Turbocharger / Power2 500-M
Original assembly instructions – English
Summary of Contents for Power2 Series
Page 2: ......