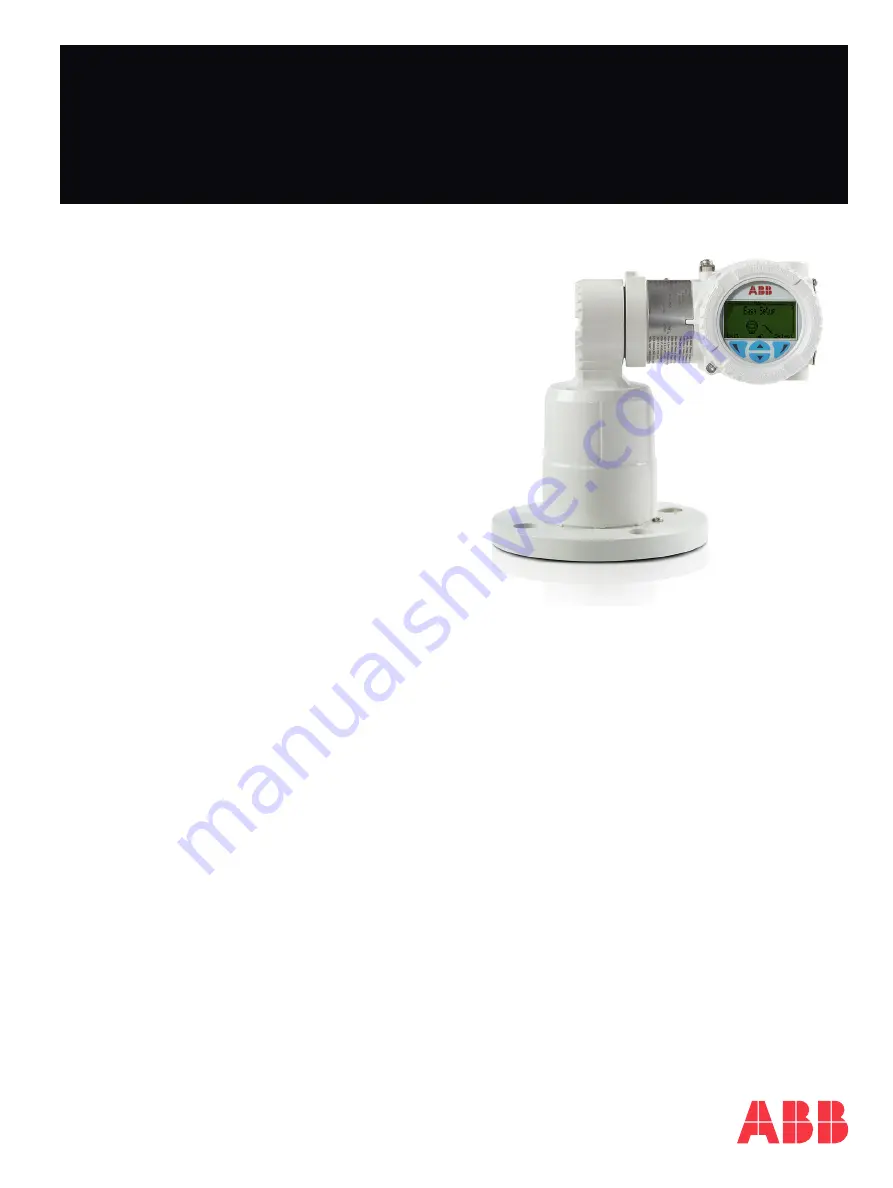
LLT100
Laser Level Transmitter
Operating Instructions/OI-LLT100-EN Rev. D
The new standard in industrial laser
level transmitters
Measurement made easy
Customer benefits
The LLT100 is specifically made for industrial applications
and harsh environments. It provides continuous, non-contact
level measurement capabilities for process automation
and inventory management in industries such as mining,
aggregates, oil & gas, chemicals, food & beverages, power,
pulp & paper, pharma, and water & waste water.
Optimize process or inventory management
– Precise measurement of any solid or liquid
– Independent of material properties
Low cost of ownership
– Fast and flexible installation
– No maintenance
– Single product configuration works in many applications
Main features
ABB brings laser level transmitters to the next level of non-
contact measurements by packaging laser ranging technology
with the features required by industrial applications. Using a
pulsed laser for performing time-of-flight measurements,
the LLT100 provides accurate distance measurements
while being powered from the 4 – 20 mA loop. Available in
aluminum or stainless steel body, it comes with a variety of
process interfaces. It can meet the demands of hazardous
area locations, as well as high pressure and high temperature
applications.
Convenient
– Easy setup function
– Articulated embedded user interface
– 2-wire powered, and HART 7 communication
Reliable
– Dust and fog penetration capabilities
– Accurate measurements at short and long distances
– Explosion-proof class 1, division 1 (zone 1)
Summary of Contents for LLT100
Page 8: ...This page intentionally left blank ...
Page 10: ...This page intentionally left blank ...
Page 18: ...This page intentionally left blank ...
Page 22: ...This page intentionally left blank ...
Page 26: ...This page intentionally left blank ...
Page 44: ...This page intentionally left blank ...
Page 50: ...This page intentionally left blank ...
Page 66: ...This page intentionally left blank ...
Page 67: ......