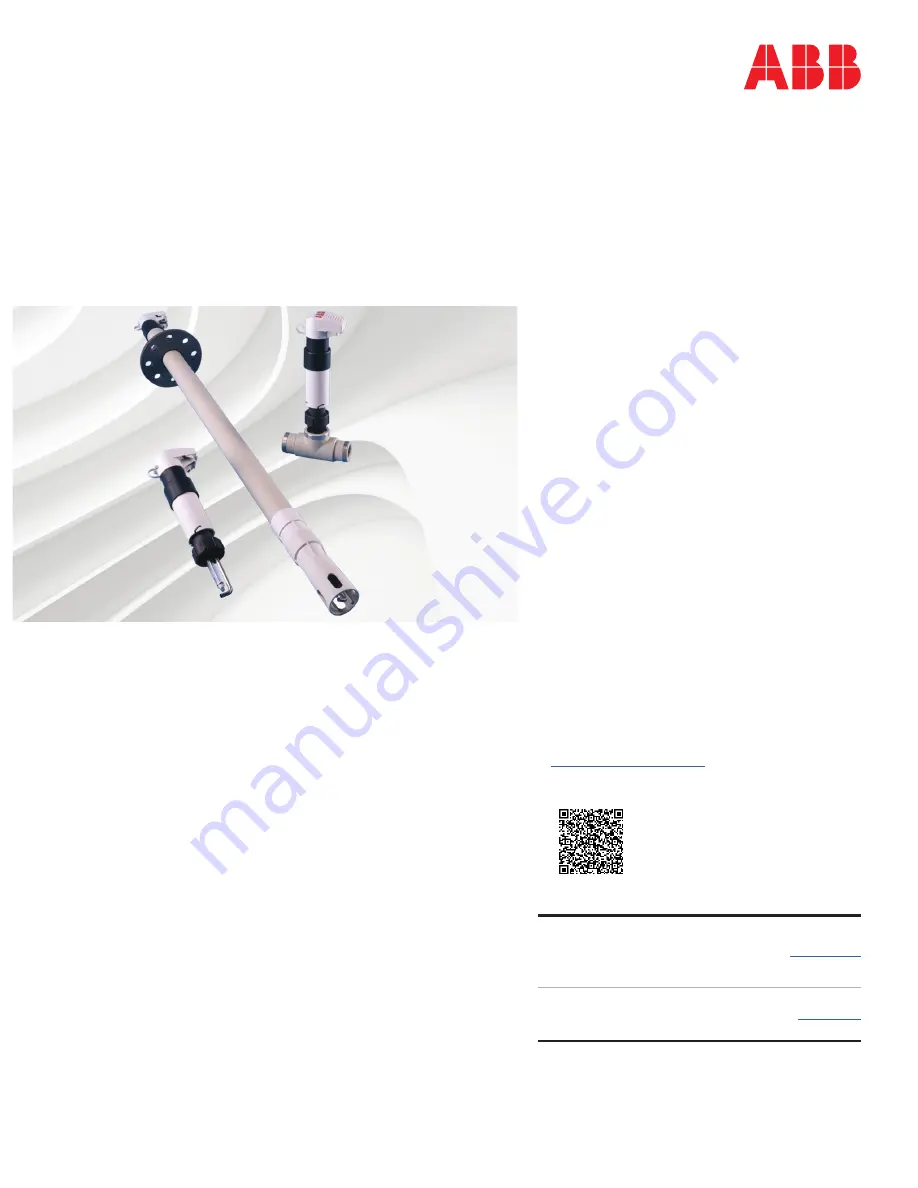
—
A B B ME A SUR EMENT & A N A LY TIC S | USER GU IDE | IM/A P20 0 R E V. S
AP200 series
Rugged pH/Redox (ORP) sensor systems with rapid
temperature response for critical processes
Measurement made easy
Introduction
The pH / redox (ORP) sensor AP200 provides high
reliability and withstands the toughest
environments for process monitoring and control.
The rugged assembly is built to bear the rigors of
weather and process. Parts in contact with the
process comprise chemically-resistant PPS Ryton™
and stainless steel, or PPS Ryton™ and Hastelloy C.
Flow-through holders are available in polypropylene,
while the PPS Ryton™ insertion adapter enables
installation in alternative material pipelines.
Insertion and Flow-through systems tolerate
temperatures up to 130 °C (266 °F) and pressures up
to 6 bar (90 psi). The inner electrode connections
are ingress-protected to IP 67 / NEMA 6P (exceeds
NEMA 4X).
For more information
Further publications are available for free download
from:
www.abb.com/analytical
or by scanning this code:
Search for
or click on
AP200
Rugged pH/Redox (ORP) sensor systems with
rapid temperature response for critical
processes
Data Sheet
DS/AP200-EN
AAO100
Dosing pump
User Guide
IM/DOSPMP
—
AP200 series
Rugged pH/Redox
(ORP) sensor systems