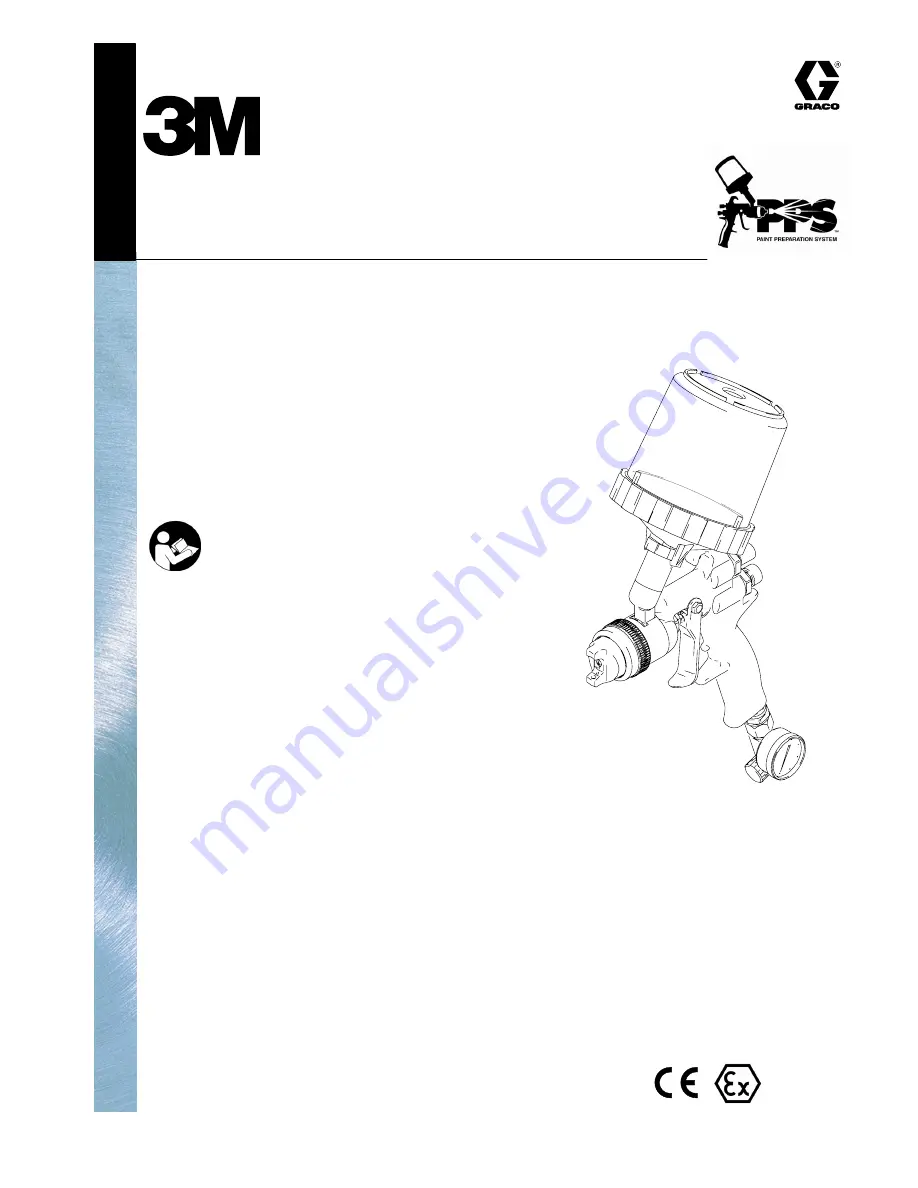
Paint Preparation System
Spray Guns
INTENDED USE: 3M–Graco spray gun systems are intended for use only by
trained and professional tradesmen, and used solely for the purpose of
spray application of liquid coating materials. They must be used only in
areas which are compatible with the material being sprayed, in strict
compliance with applicable local and national regulations.
HVLP, Compliant, and Airspray
100 psi (0.7 MPa, 7 bar) Maximum Working Air Pressure
29 psi (200 kPa, 2.0 bar) Maximum Compliant Inbound Air Pressure
(HVLP and Compliant)
U.S. Patent Pending
Table of Contents
Symbols
2
. . . . . . . . . . . . . . . . . . . . . . . . . . . . . . .
Warnings
2
. . . . . . . . . . . . . . . . . . . . . . . . . . . . . . .
Selection Charts
4
. . . . . . . . . . . . . . . . . . . . . . . .
Typical Installation
5
. . . . . . . . . . . . . . . . . . . . . . .
Setup
6
. . . . . . . . . . . . . . . . . . . . . . . . . . . . . . . . . .
Operation
11
. . . . . . . . . . . . . . . . . . . . . . . . . . . . .
Daily Gun Care, Flushing, and Cleaning
13
. . .
Troubleshooting
16
. . . . . . . . . . . . . . . . . . . . . . . .
Service
18
. . . . . . . . . . . . . . . . . . . . . . . . . . . . . . .
Parts
24
. . . . . . . . . . . . . . . . . . . . . . . . . . . . . . . . .
Accessories
27
. . . . . . . . . . . . . . . . . . . . . . . . . . .
Dimensions
27
. . . . . . . . . . . . . . . . . . . . . . . . . . . .
Technical Data
27
. . . . . . . . . . . . . . . . . . . . . . . . .
Warranty
28
. . . . . . . . . . . . . . . . . . . . . . . . . . . . . .
Contact Information
28
. . . . . . . . . . . . . . . . . . . . .
Manufactured by
Instructions – Parts List
II 2 G
Important Safety Instructions
Read all warnings and instructions in this manual.
Save these instructions.