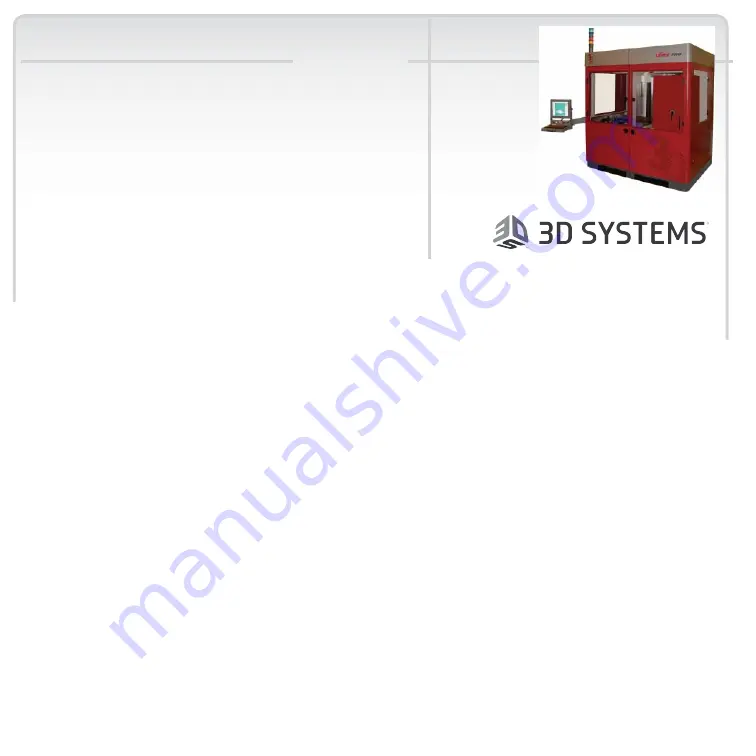
Viper Pro
q u i c k s t a r t
g u i d e
Thank you for purchasing the Viper Pro
system .
Before using this equipm ent,
please read this guide
carefully
to
enjoy
optim um
perform ance
and
longer
service life.
Docum ent 23XXX-M XX-00
Revision 1X DRAFT
Decem ber 2005
Copyright © 2005 by
3D System s Corporation.
All rights
reserved.
3D System s,
the
3D System s logo, and Viper Pro
are
registered
tradem arks of 3D System s,Inc.
O ther tradem arks
are the property
of their respective ow ners.
To prepare and build a part, see Quick System Overview on page 11.
The Viper Pro system runs on 200-240 VAC / 50-60Hz, single phase power 30A for the single
resin delivery module and 50A for the dual and extra large resin delivery module.
i
See “Facility Requirements Guide: Viper Pro SLA System” for complete Viper Pro system electrical,
mechanical, environmental, and network requirements.
™
What’s Inside? 3
New Features 7
Hazard Messages 9
Other Useful Documents 10
Quick System Overview 11
Operator Interface 15
RDM Installation and Removal 16
RDM Removal 34
Software Overview 40
Gel and Debris Filtering 46
Recoater Module 48
Lasers 51
Safety 54
Maintenance 60
Glossary 62
Troubleshooting 75
Содержание Viper Pro SLA iPro 8000
Страница 2: ...q u i c k s t a r t g u i d e 2 Customer Support 78 Legal Notices 79 ...
Страница 12: ...q u i c k s t a r t g u i d e q u i c k s y s t e m o v e r v i e w 12 ...
Страница 13: ...q u i c k s t a r t g u i d e q u i c k s y s t e m o v e r v i e w 13 ...
Страница 14: ...q u i c k s t a r t g u i d e q u i c k s y s t e m o v e r v i e w 14 ...
Страница 27: ...q u i c k s t a r t g u i d e r d m i n s t a l l a t i o n a n d r e m o v a l 27 Figure 7 Container Lifted ...