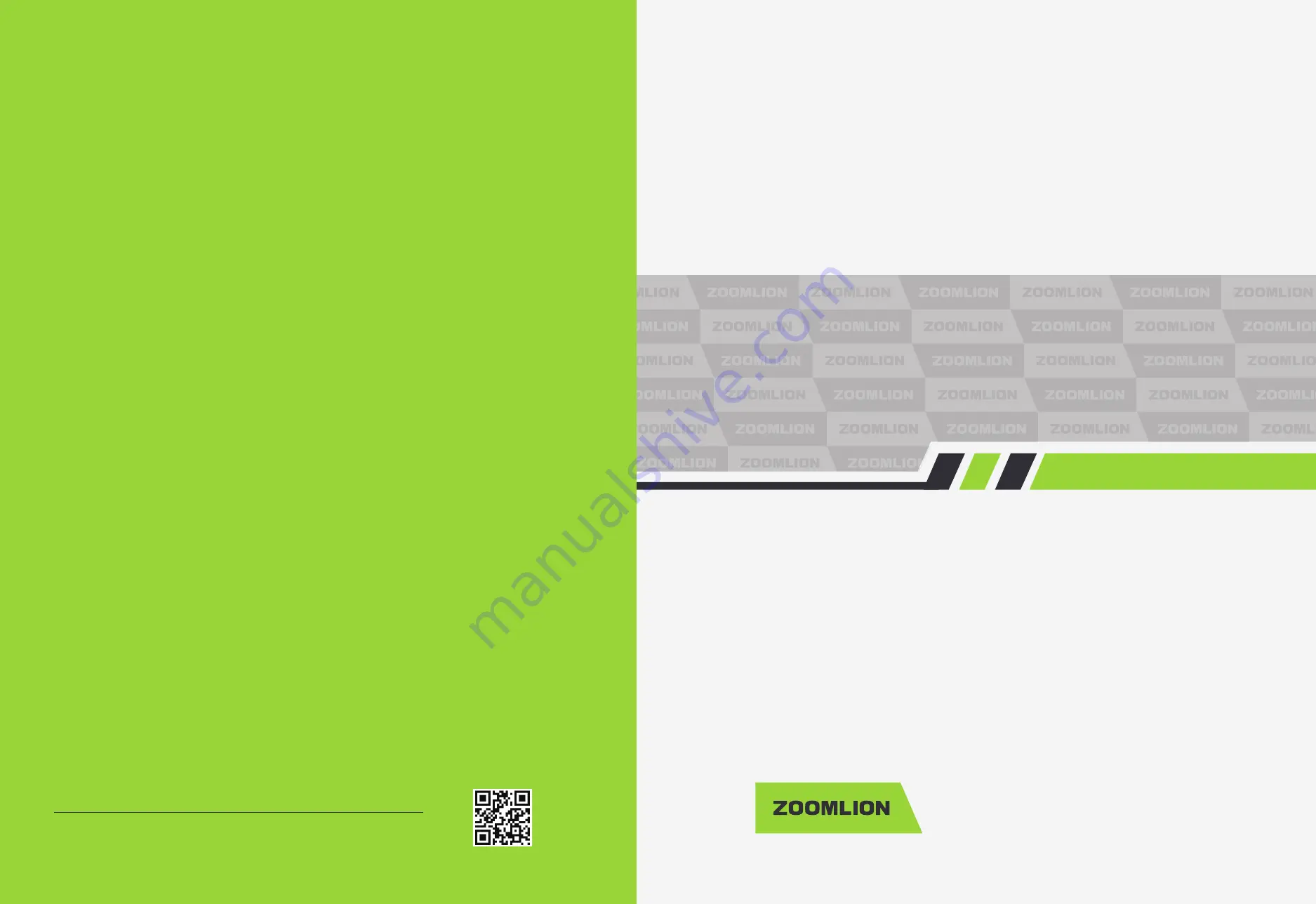
Zoomlion Heavy Industry Science & Technology Co.,Ltd.
Address: Quantang Industrial Park, No. 1636, 2nd Yuanda Road, Changsha, Hunan Province, China
Postcode: 410131
Website: http://www.zoomlion.com Email: [email protected]
Copyright © 2015 Zoomlion Heavy Industry Science&Technology Co., Ltd. All rights reserved
CRAWLER CRANE
OPERATOR’S MANUAL
Summary of Contents for ZCC2600CR
Page 2: ......
Page 3: ...Edition 1 July 2018 ZCC2600CR Crawler Crane Operator s Manual...
Page 4: ......
Page 13: ...Chapter 1 Safety Operator s Manual for Crawler Crane...
Page 14: ......
Page 20: ......
Page 21: ...Chapter 2 Description of Crane Operator s Manual for Crawler Crane...
Page 22: ......
Page 41: ...Chapter 3 Safety Guidelines Operator s Manual for Crawler Crane...
Page 42: ......
Page 69: ...Safety Guidelines Operator s Manual for Crawler Crane Figure 3 67 Hook 3 27...
Page 126: ......
Page 127: ...Chapter 4 Crane Operation Operator s Manual for Crawler Crane...
Page 128: ......
Page 224: ......
Page 225: ...Chapter 5 Assembly and Dismantling Operator s Manual for Crawler Crane...
Page 226: ......
Page 395: ...Chapter 6 Appendix Operator s Manual for Crawler Crane...
Page 396: ......