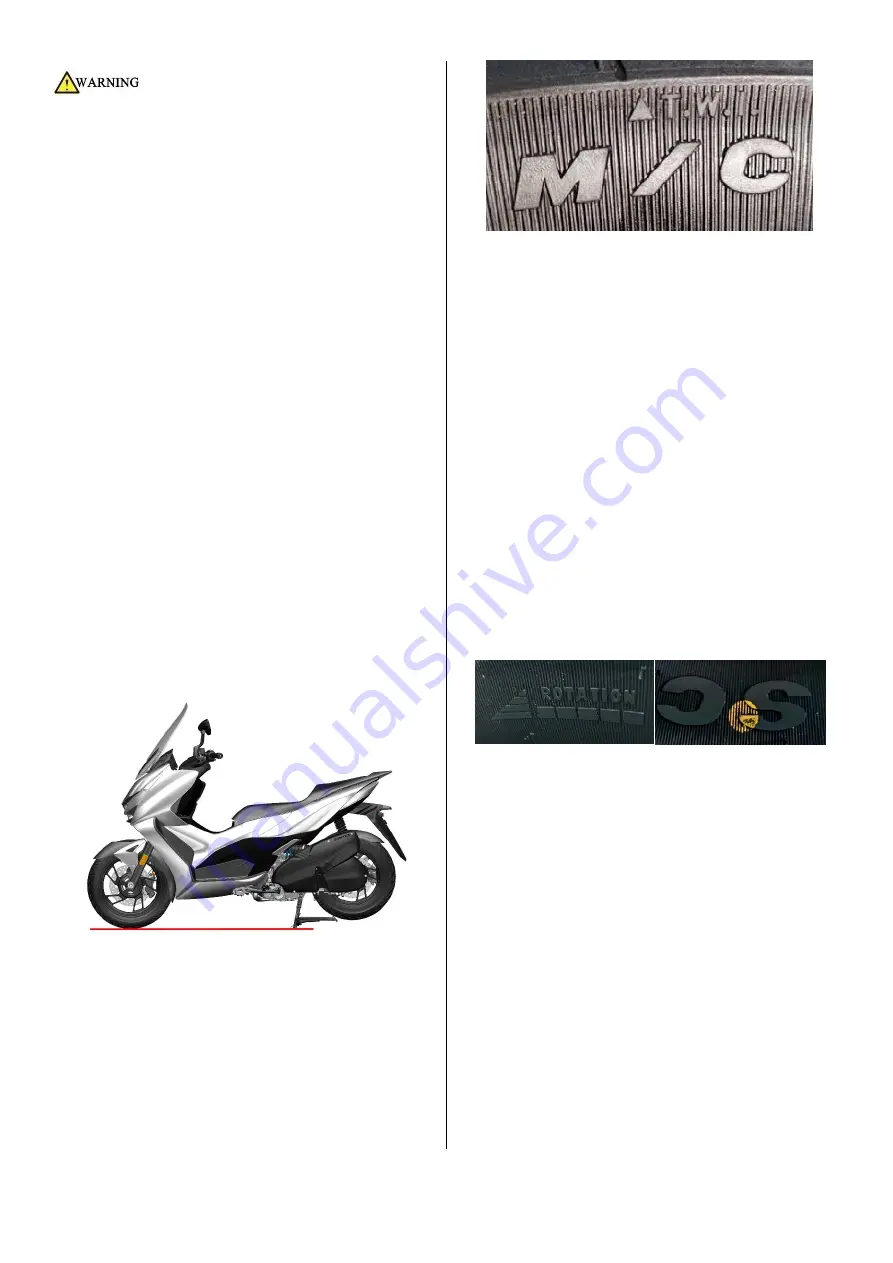
59
/
152
●Check the tire pressure regularly. D350 the standard is
240kPa (2.5 kgf/cm2, 35 PSI) under normal temperature
conditions. The maximum tire pressure in the cold state shall
not exceed 300 kPa (3.1 kgf/cm2, 44 PSI).
●When the tire pressure is found to drop, check whether the
tire has nails or small holes; whether there is a collision on
the side of the rim that causes deformation or cracks.
●Be careful to avoid the position of the valve when removing
the tire with the tyre raking machine. Pay attention to
protect the contact part of the rim and the bead, if it is
scratched, it may cause air leakage.
●The tire pressure is too high, which reduces the contact
area with the ground. It is also more likely to cause a
puncture in the summer.Too low will cause difficult steering,
accelerate wear and increase engine load and increase fuel
consumption.
●Frequent exposure to the sun can cause tire cracks and
aging. It is recommended to park the vehicle in a dust-proof,
sun-proof, and ventilated place; or cover it with a car jacket
to protect the body parts and the tires better. If you do not
drive for a long time, you should support the vehicle firmly
and let the tires hang in the air to avoid deformation caused
by long-term load on the ground contact.
●Because the tire self-refilling may block the air hole of the
tire pressure monitoring sensor, causing difficulty in inflation
or failure of the tire pressure monitoring, it should not be
used.
1. Check the tires
a. Park the vehicle on a flat and stable ground or a lifting
platform, and put down the main support.
b. Support the front wheel with suitable tools, let the front
tire hang in the air, and then rotate the tire to carefully check
for abnormalities, such as partial wear, studs, cracks, etc.
Clean up the pebbles or other foreign objects embedded in
the tread pattern. Check whether the tread and sidewall have
worn to the mark. If they are close to or have worn to the
mark, replace with a new tire of the same specification in
time. Use a tire pressure gauge to measure the tire pressure
when the tire is cold, and add or deflate to the standard
pressure.
b. The height of the wear mark on the tread protrusion is
1.6mm (0.06 in). The triangle (
△
T.W.I.) mark on the sidewall
indicates the location of the wear bar. If the wear reaches the
mark point, it means that it has been worn to the limit. If you
continue to drive, there will be a safety hazard. You must
replace with new tires of the same specification.
c. The inspection of the rear tires is the same as that of the
front tires and will not be repeated here.
2. Replace tires
a. Replace the front tire
The front wheel assembly can be removed by referring to
the description of the steps for disassembling the front wheel
assembly in the "Front Fork Assembly" of this manual. Use a
tyre picker to remove the tire. When disassembling, pay
attention to avoiding the valve position. Do not use a
crowbar to pry the tire at the valve position to avoid damage
to the tire pressure sensor. Before pressing the tire, install it
according to the direction of rotation indicated by the
sidewall, and aim the light point with the yellow mark at the
position of the valve. After replacing a new tire or repairing a
tire, the dynamic balance needs to be re-balanced to prevent
the front wheel from shaking due to unbalance and affecting
the driving experience
b. Replace the rear tire
Refer to the previous operation of replacing the rear brake
disc to remove the rear wheel assembly. Other operations
are similar to the replacement of the front tires, and will not
be repeated here.
Steering mechanism
Caution:
●Regularly inspect the steering mechanism according to the
requirements of the regular maintenance table.
●Park the vehicle on a flat and stable ground or a lifting
platform, and put down the main support.
●Too small steering mechanism clearance will cause
inflexible steering and accelerate bearing wear. When it is
too large, it will cause driving jitter and abnormal noise when
braking.
1. Check the steering mechanism
a. Support the front wheel with a suitable tool so that the
front tire is hung in the air and then rotate the direction
handle left and right to confirm whether the rotation is
flexible and smooth; whether the cable and cable show signs
of being pulled.
Summary of Contents for ZT350T-D
Page 1: ...1 152 ZT350T D Maintenance Manual 2022 11 24...
Page 50: ...50 152 D350 Braking system component diagram...
Page 88: ...88 152 Electrical schematic diagram of EFI system...
Page 124: ...124 152 Exploded view of front fork components Directional exploded view...
Page 125: ...125 152 Front fork exploded view...