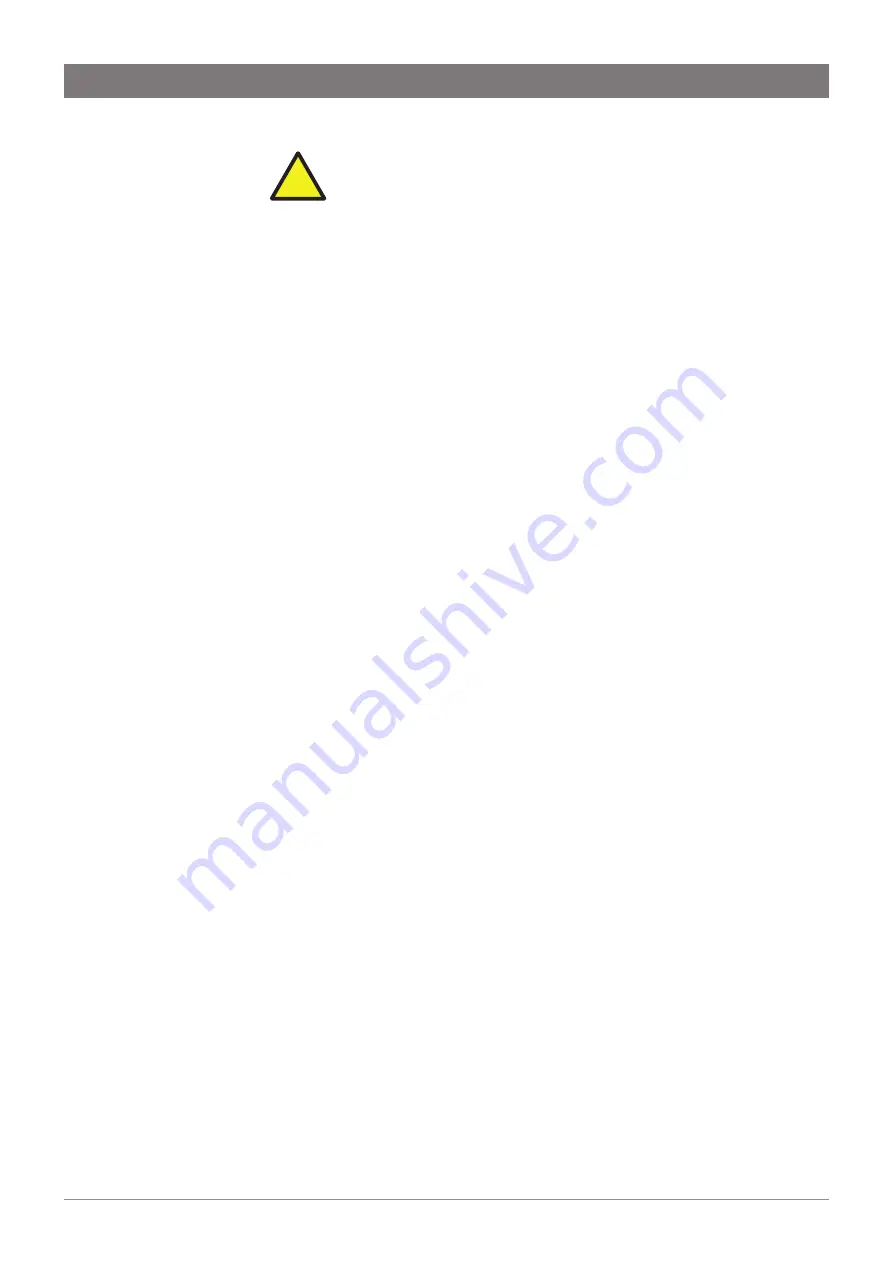
26
805812 v1.04 05.20 HydroChill Install Instructions
If the HydroChill is out of order due to maintenance, fault, or any
other reason, affix a clearly marked sign on the machine to prevent
unauthorised use.
Always disconnect the machine from the electricity supply before
performing maintenance.
When replacing components, use only genuine spare parts.
Contact your nearest service centre for assistance, service, spare
parts or enquiries.
Daily maintenance
• Inspect pipelines. Ensure water, CO
2
and drain lines are not
obstructed, crushed or leaking.
• Check the CO
2
supply is adequate and in good working order, and
that the set pressure values are correct.
• Clean external surfaces:
− Clean using a soft cloth and a stainless steel cleaner or
neutral detergent.
− To prevent damage, do not use abrasive materials, solvents,
alcohol, etc. Do not clean with water jets.
− Clean the dispensing nozzles with a diluted hydrogen
peroxide solution or sanitisation wipes.
− Clean the drip tray using a diluted lime-scale cleaner such
as citric acid, or in a dishwasher.
− Clean dust/dirt from condenser grille using a soft brush.
− Dry thoroughly before putting the machine back into
operation.
Clean condenser: every 3 months
The cooling condenser must be cleaned every three months, or when
necessary, to prevent the build-up of dust and grease which may cause
overheating and could damage the compressor beyond repair.
1. Disconnect from electricity supply.
2. Remove the front or side panel.
3. Gently clean the condenser fins using a soft brush, a vacuum
cleaner or low-pressure compressed air.
4. Remove any dust from the cooling and electrical components.
5. Refit the panel.
6. Reconnect electrical supply.
Maintenance
!