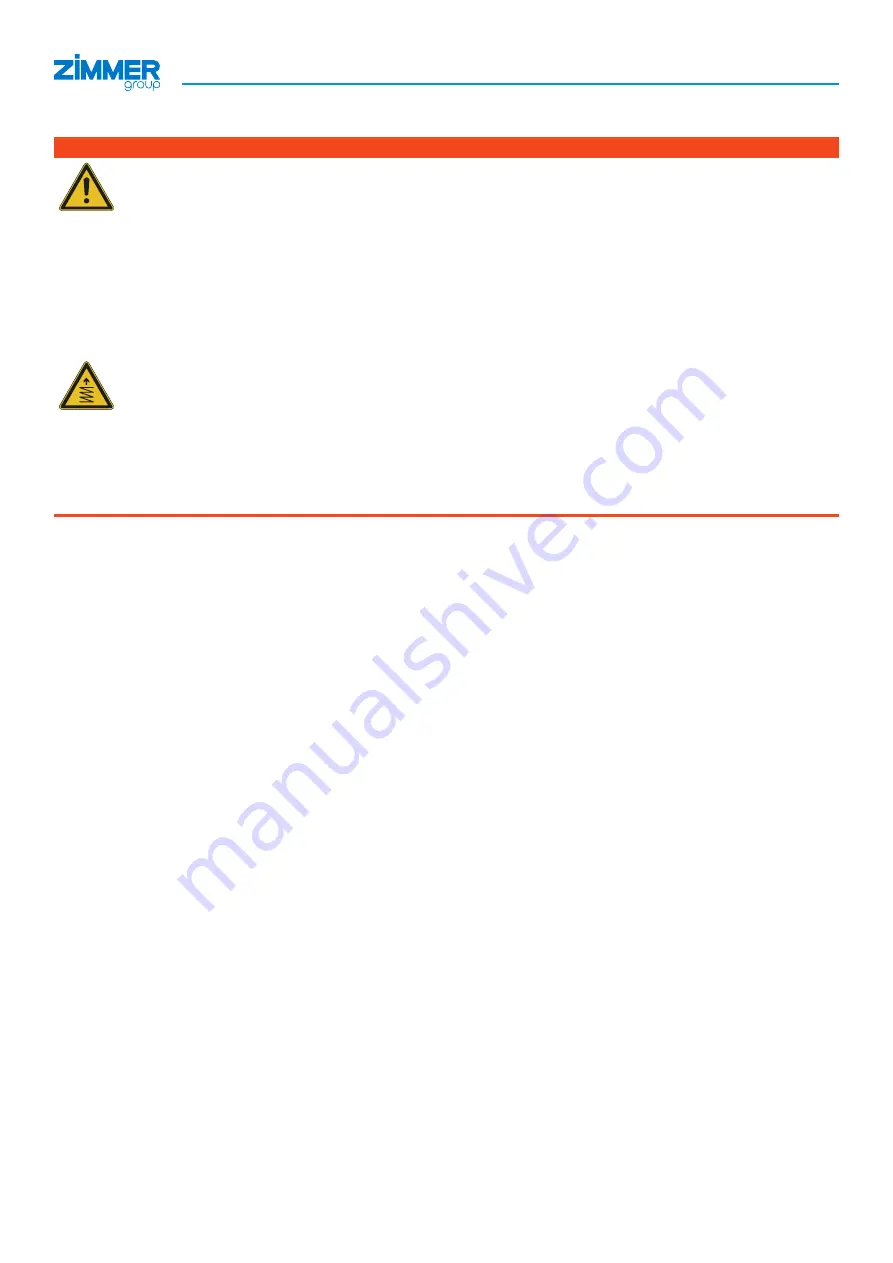
Zimmer GmbH • Im Salmenkopf 5 •
77866 Rheinau, Germany •
+49 7844 9138 0 • www.zimmer-group.com
DDOC00836 / e
4
INSTALLATION AND OPERATING INSTRUCTIONS:
SPN
EN / 2022-10-12
2 Safety notices
WARNING
Risk of injury during manual loading
Risk of injury due to parts moving independently after the power supply has failed or is switched off (including an
emergency stop).
►
Do not reach into the product.
►
Do not reach between the clamping surfaces.
►
Wait for the system to come to a complete standstill.
Risk of injury due to parts moving independently after accidental or careless actuation of the release actuation.
►
Do not insert a clamping pin into a clamped product.
►
Do not place a clamping pin onto a clamped product.
Risk of injury from parts flying and being flung
Various components of the product are continuously under spring tension.
• Spring package
• Cover
►
Do not loosen the screws of the cover.
►
Do not remove the cover.
Ö
Warranty and disclaimer