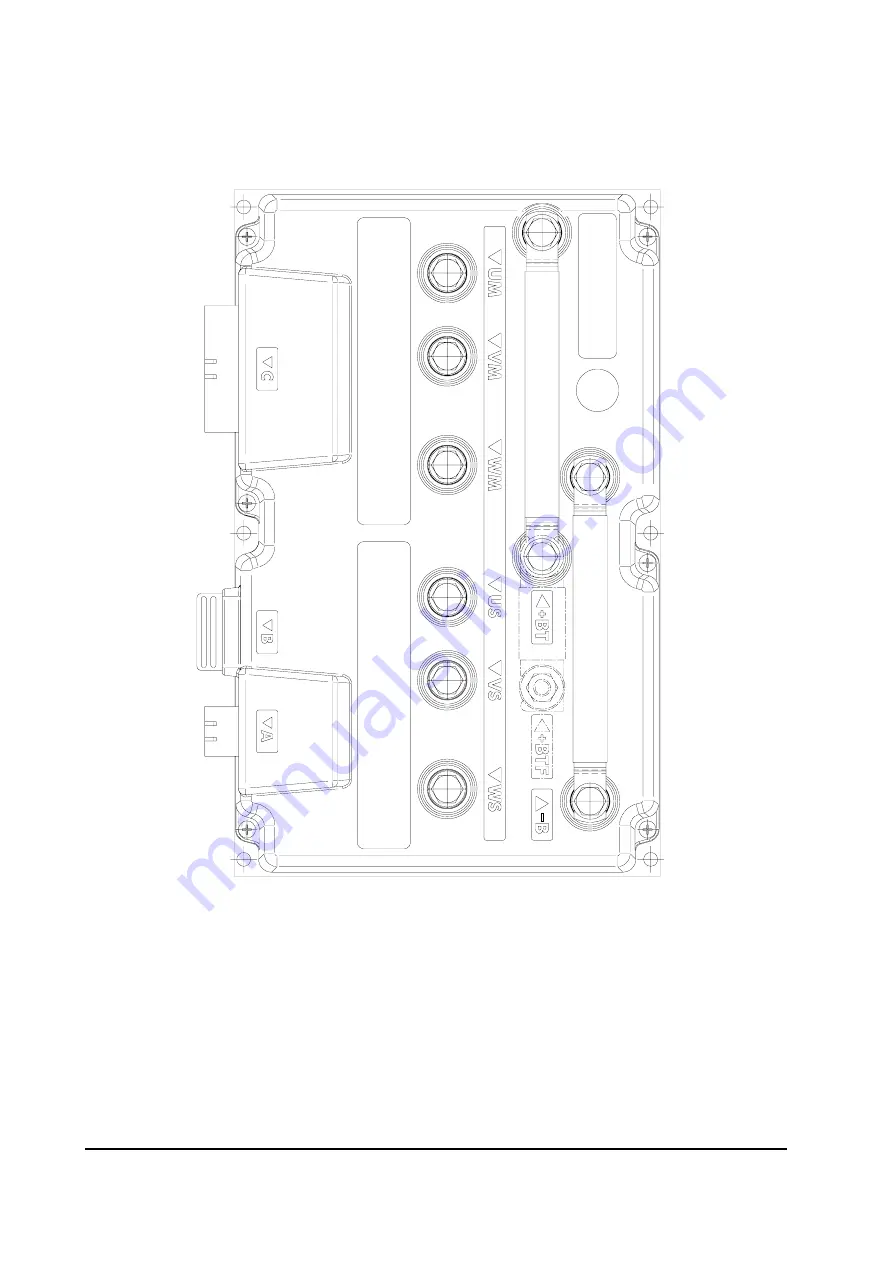
Page 26
4.8 DESCRIPTION OF POWER CONNECTIONS
4.8.1 "Dualac2"
View of the power bars:
-B
Negative of the battery.
+BT
Positive of the battery; if the power fuse is not present, the positive
cable coming from LC contact must be connected to this power
connection.
+BTF
Positive of battery before power fuse, must be connected to positive
cable coming from LC contact.
Um; Vm; Wm
Connection bars of the three right motors phases; follow this se-
quence and the indication on the motor.
Us; Vs; Ws
Connection bars of the three left motors phases; follow this se-
quence and the indication on the motor.
Summary of Contents for DUALAC2
Page 32: ...Page 32 4 9 MECHANICAL DRAWING Dimensions of Dualac2...
Page 33: ...Page 33 Dimensions of Dualac2 Power...
Page 34: ...Page 34 Dimensions of Dualac2 hp...
Page 35: ...Page 35 Dimensions of Dualac2 hp Power...
Page 36: ...Page 36 4 10 CONNECTION DRAWING DUALAC2 AND DUALAC2 POWER STANDALONE...
Page 37: ...Page 37 4 11 CONNECTION DRAWING DUALAC2 HP AND DUALAC2 HP POWER STANDALONE...
Page 40: ...Page 40 5 3 1 b Slave...
Page 41: ...Page 41 5 3 2 Dualac2 hp and Dualac2 hp Power menu configuration 5 3 2 a Master...
Page 42: ...Page 42 5 3 2 b Slave...