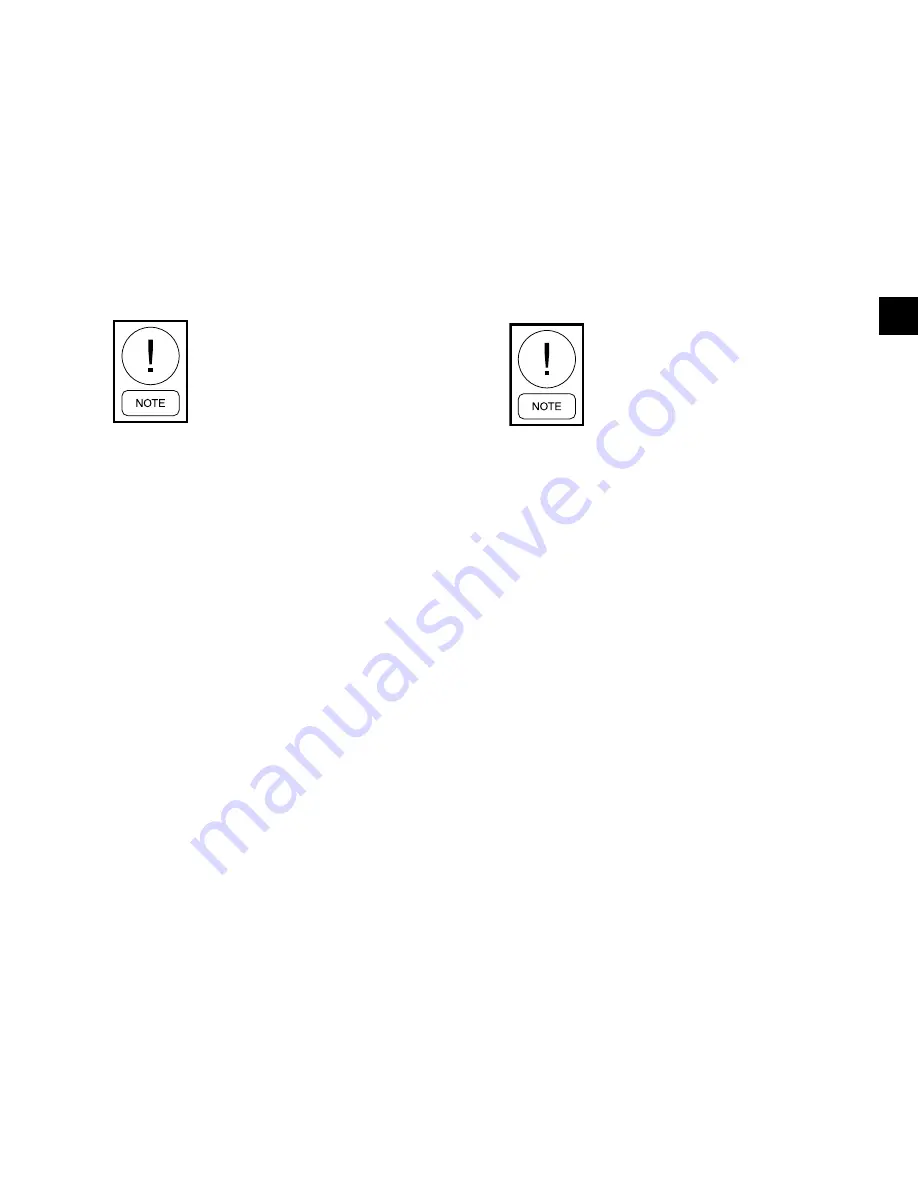
JOHNSON CONTROLS
51
SECTION 5 - COMMISSIONING
FORM 155.33-ICOM2.EN.GB
ISSUE DATE:12/4/2017
5
START THE CHILLER-HEATER
Before starting the chiller-heater, review the following:
• Check that the refrigerant blow valve V2 is closed.
• Check the degree of the vacuum in the machine.
Use the pressure gauge of the high temperature
generator.
• Check the c
hilled / hot
water inlet temperature.
• Make sure the Forced Exhaust Gas Bypass
OFF
switch is selected. If it is not, turn the switch.
The switch is located on the exterior of
the control panel door. See
.
• Check the following:
a. Forced Dilution
OFF
button is pressed
b. Refrigerant Pump
Auto
button is pressed
c. Blower Fan
Auto
button is pressed.
1. After the review is complete, press the
OPER.
button on the Control Panel Main screen to start
the chiller-heater. To start the chiller-heater from a
remote location, enter the remote start signal.
When the chiller-heater starts, the following occurs:
• The solution circulation pump, solution spray
pump, and refrigerant pump start.
• The exhaust gas inlet valve, the exhaust outlet
valve, and the waste hot water control valve open.
STOP THE CHILLER-HEATER
1. To stop the chiller-heater, press the
STOP
but-
ton on the Control Panel Main screen. To stop the
chiller-heater from a remote location, enter the re-
mote stop signal.
When the chiller-heater stops, the following occurs:
• The exhaust gas inlet valve, the exhaust outlet
valve, and the waste hot water control valve close.
• The dilution operation starts.
During the dilution operation, the solu-
tion circulation pump, solution spray
pump, and refrigerant pump operate.
• Once the dilution operation is complete, the solu-
tion circulation pump, solution spray pump, and
refrigerant pump stop.
• Then, the chilled / hot water pump, the cooling
water pump, and the cooling tower stop.
INTERLOCK PROCEDURE
Operating the chiller-heater in cooling mode without
the air conditioner running can cause the chilled water
to freeze. If the unit contains only one air conditioner,
secure the air conditioner interlock.