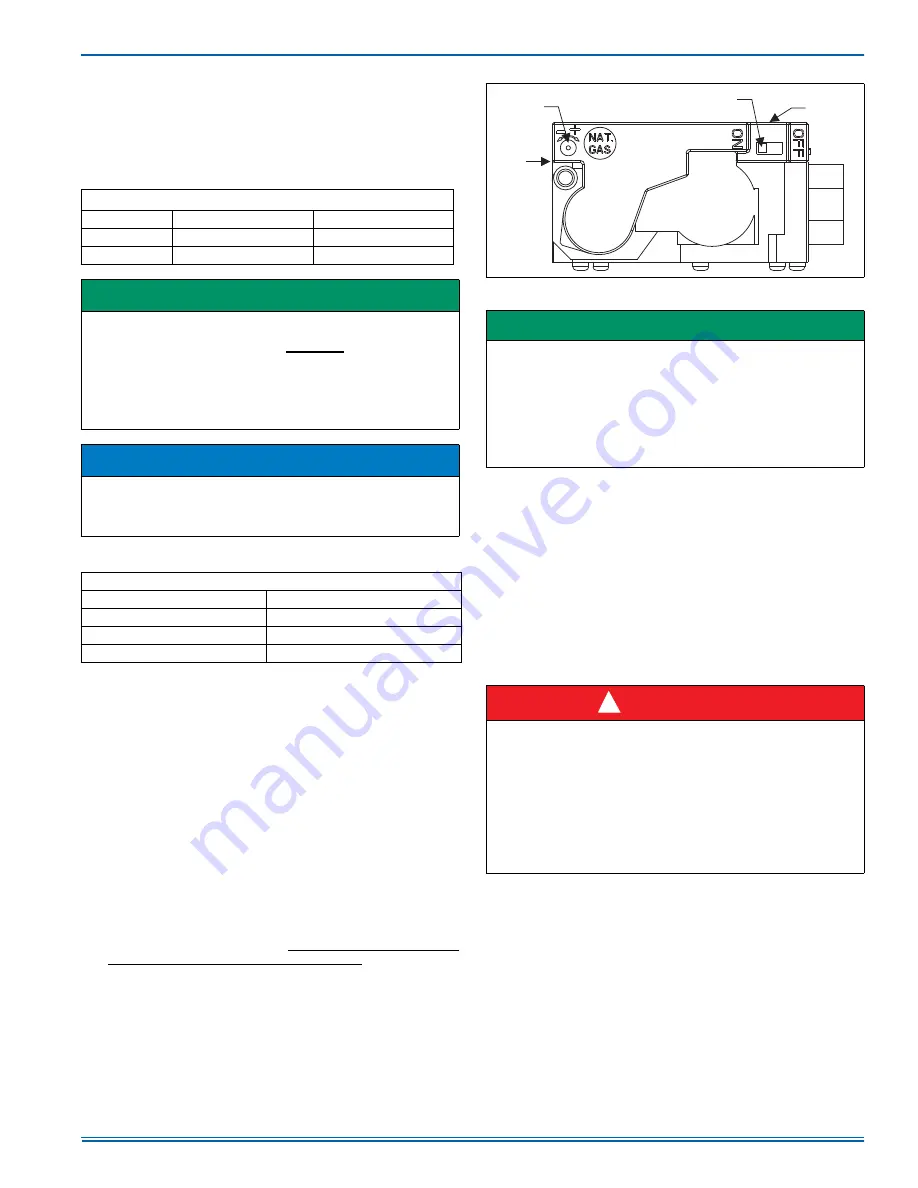
1083293-UIM-D-1116
Johnson Controls Unitary Products
35
ADJUSTMENT OF MANIFOLD GAS PRESSURE
Inlet and manifold gas pressure may be measured by connecting the
“U” tube manometer to the gas valve with a piece of tubing. Follow the
appropriate section in the instructions below. Refer to Figure 40 for the
locations of the pressure ports on the gas valve.
Turn gas off at the ball valve or gas cock on gas supply line
before the gas valve. Find the pressure ports on the gas
valve marked Out P and In P.
1.
The manifold pressure must be taken at the port marked OUT P.
2.
The inlet gas line pressure must be taken at the port marked IN P.
3.
Using a 3/16” allen wrench, remove the plugs from the inlet and
outlet pressure ports. Connect a 1/8” UPT barbed hose fitting to
each pressure port.
4.
Refer to Figure 40 for location of pressure regulator adjustment
screw on main gas valve.
5.
Turn gas and electrical supplies on and follow the operating
instructions to place the unit back in operation.
6.
Use a small slotted screwdriver to turn the regulator adjustment
screw. Adjust the pressure by turning the screw one click at a time
until desired pressure is reached. Wait a few seconds after each
adjustment to allow the pressure to stabilize before making addi-
tional adjustments. This is an electronic adjustment screw that
does not require very much force. Application of excessive force to
the adjustment screw will damage the gas valve.
7.
After the manifold pressure has been adjusted, re-calculate the
furnace input to make sure you have not exceeded the specified
input on the rating plate. Refer to "CALCULATING THE FURNACE
INPUT (NAT. GAS)".
8.
Once the correct BTU (kW) input has been established, turn the
gas valve to OFF and turn the electrical supply switch to OFF; then
remove the flexible tubing and fittings from the gas valve pressure
tap replace the pressure tap plugs.
9.
Turn the electrical and gas supplies back on, and with the burners
in operation, check for gas leakage around the gas valve pressure
port for leakage using an approved gas detector, a non-corrosive
leak detection fluid, or other leak detection methods.
ADJUSTMENT OF TEMPERATURE RISE
After about 5 minutes of operation, determine the furnace temperature
rise. Take temperature readings of both the return air and the heated air
in the ducts about six feet away from the furnace, where they will not be
affected by radiant heat. Increase or decrease the temperature rise by
changing the ATR jumper on the furnace control board. The jumper is
factory-set to deliver an air temperature rise near the midpoint of the
nameplate temperature rise range. If more air is desired (lower tem-
perature rise), move the jumper to the -10 position. If less air is desired
(higher temperature rise), move the jumper to the +10 position.
Do not move the motor wires to different positions on the
furnace control board!
Table 15:
Inlet Gas Pressure Range
INLET GAS PRESSURE RANGE
Natural Gas
Propane (LP)
Minimum*
4.5” w.c. (1.12 kPa)
8.0” w.c. (1.99 kPa)
Maximum
10.5” w.c. (2.61 kPa)
13.0” w.c. (3.24 kPa)
IMPORTANT
The inlet gas pressure operating range table specifies what the mini-
mum and maximum gas line pressures must be for the furnace to
operate safely. The gas line pressure MUST BE a minimum of:
•
7” w.c. (1.74 kPA) for Natural Gas
•
11” w.c. (2.74 kPA) for Propane (LP) Gas
in order to obtain the BTU input specified on the rating plate and/or
the nominal manifold pressure specified in these instructions and on
the rating plate.
NOTICE
The regulated outlet pressure has been calibrated at the factory.
Additional pressure adjustment should not be necessary. If adjust-
ment is necessary, set to the following specifications. After adjust-
ment, check for gas leakage.
TABLE 16:
Nominal Manifold Pressure
NOMINAL MANIFOLD PRESSURE
Natural Gas (Max)
3.5" w.c. (0.87 kPa)
Natural Gas (Min)
0.5" w.c. (0.15 kPa)
Propane (LP) Gas (Max)
10.0" w.c. (2.49 kPa)
Propane (LP) Gas (Min)
1.6" w.c. (0.40 kPa)
FIGURE 40:
Gas Valve
IMPORTANT
If gas valve regulator is turned clockwise, manifold pressure is
increased. If screw is turned counterclockwise, manifold pressure will
decrease.
The adjustment screw has a range of 16 clicks (about ±0.5” manifold
pressure). There is not a hard stop at the ends of the adjustment
range. When the limit of the adjustment range is reached, the next
click will start over at the other end of the range. For instance, if you
are increasing pressure and reach the upper limit of adjustment the
next click will drop the pressure to the lower limit.
DANGER
The temperature rise, or temperature difference between the return
air and the supply (heated) air from the furnace, must be within the
range shown on the furnace rating plate and within the application
limitations shown in Table 6.
The supply air temperature cannot exceed the “Maximum Supply
Air Temperature” specified in these instructions and on the furnace
rating plate. Under NO circumstances can the furnace be allowed to
operate above the Maximum Supply Air Temperature. Operating the
furnace above the Maximum Supply Air Temperature will cause pre-
mature heat exchanger failure, high levels of Carbon Monoxide, a fire
hazard, personal injury, property damage, and/or death.
Inlet
Pressure
Tap
Outlet
Pressure
Tap
On/Off
Switch
Main
Regulator
Adjustment
!