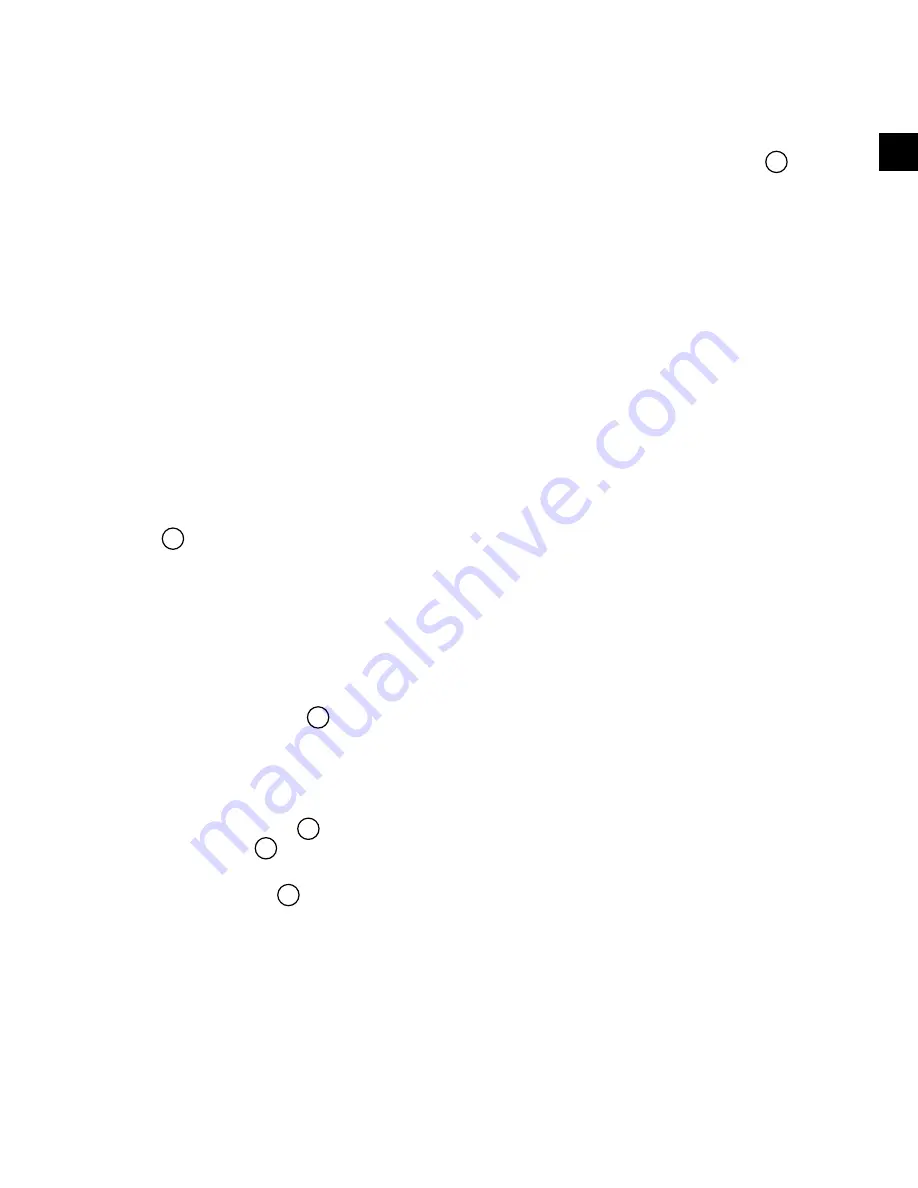
JOHNSON CONTROLS
13
Form 160.00-N6
Issue date: 08/27/2021
2
General
These details specify procedures that must be followed
by the customers' contractor when installing the indus-
trial drive and motor systems. In order to better un-
derstand the reasons for many of the practices that are
recommended, it is helpful to segregate these practices
into two separate categories as follows:
• To protect against the risk of electrical shock or
burn.
•
To protect the equipment from fire or other dam
-
age due to ground faults or lightning strikes.
These practices must be followed by the contractor in
compliance with NEC and other code requirements.
Equipment grounding
• All metal building structures such as columns,
floor beams, and similar structures, must be
grounded by an interconnecting heavy ground ca-
ble 5 in accordance with recommended building
practices and local codes.
• All electrical joints and connections to the build-
ing structures must be brazed or exothermic weld-
ed to ensure that the required good electrical and
mechanical properties do
not
deteriorate with the
passage of time.
• All panels must be grounded at least one point us-
ing a heavy safety cable 7 . Panels greater than
15 ft long must be grounded at both ends. The
ground cable needs to be at least 1/0 AWG for me-
chanical reasons and need not be greater than 500
MCM. This cable is usually non-insulated.
• The safety ground cable 7 must be brazed or exo-
thermic welded 7A to a building steel structure
that is closest to the panel, preferably within 25 ft.
• The equipment end 7B must be bolted or brazed
to a ground termination point on the panel.
• The equipment grounding terminal is a copper
ground bus or stub bus bonded to the panel enclo-
sure using brazing or bolting in such manner that
the conducting path has a resistance of 0.1 ohm
or less.
• The grounding conductors must be capable of
handling anticipated ground fault currents.
• There must be a jumper cable 11 across the
ground bus floor sill between any shipping splits
and sized the same as the safety ground unless
otherwise specified.
• The protective grounding described previously
for power conversion and control cabinets is also
required for motors, transformers, and reactors.
Each of these must have its own grounding con-
ductor going directly to the building ground grid.
Grounding procedure needed to ensure
electrical noise immunity
• Installation on a concrete housekeeping pad:
The majority of installations have the MVVSD
positioned on a concrete housekeeping pad. This
pad must be level within 1/4 in. end-to-end to pre-
vent flexing of the cabinet sections. It is also criti-
cal that the heavy transformer inside rests equally
on all four corners of the cabinet structure below
it. A dedicated grounding conductor is required
between the upstream feeder and the input power
lugs in the drive. A dedicated grounding conduc-
tor likewise is required from the output lugs in
the drive to the chiller motor. There is an internal
grounding bus within the drive which joins these
input and output grounding conductors along with
all cabinet sections of the drive.
•
Installation on steel leveling beams or metal floor
-
ing or decking:
•
Leveling beams, steel mesh, galvanized
floor, decking, and similar structures, must
be installed before placing the equipment.
These must be connected to the building
ground system using a brazing or exothermic
welding process.
• Grounding leveling beams are not an abso-
lute necessity for satisfactory operation on
new construction where such beams can be
provided with little difficulty. For existing
construction, it usually is more difficult, in
which case the leveling beams may be dis-
pensed with, provided other grounded struc-
tures such as columns and floor beams are
within 10 ft of the equipment.
Section 2 - Equipment grounding