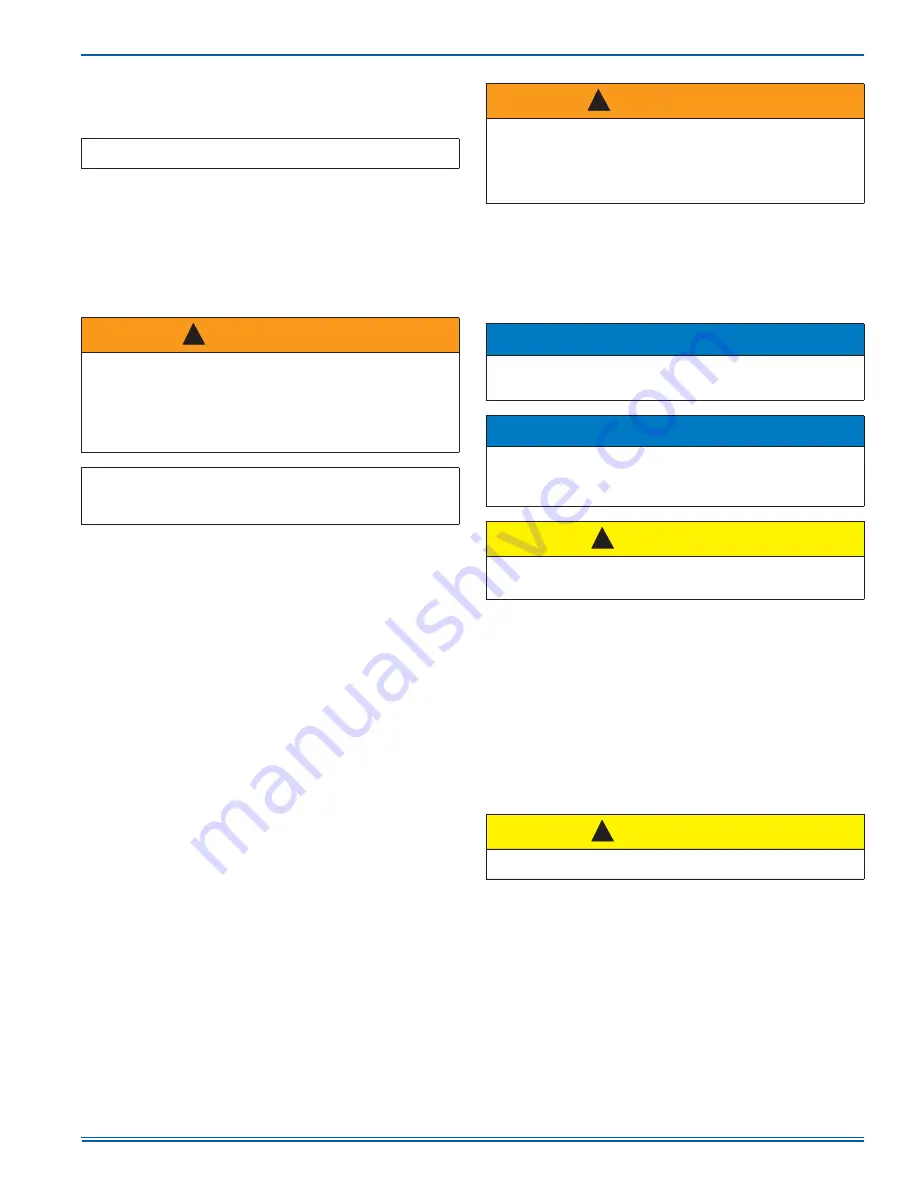
5715184-BIM-A-0519
Johnson Controls Ducted Systems
25
SECTION VIII: START-UP AND CHECKS
The initial start-up of the furnace requires the following additional proce-
dures:
When the gas supply is initially connected to the furnace, the gas piping
may be full of air. In order to purge this air, it is recommended that the
ground union be loosened until the odor of gas is detected. When gas is
detected, immediately retighten the union and check for leaks. Allow
five minutes for any gas to dissipate before continuing with the start-up
procedure. Be sure proper ventilation is available to dilute and carry
away any vented gas.
GAS PIPING LEAK CHECK
It is recommended that when the gas supply is first connected to the
furnace, the ground union be loosened until the odor of gas is detected.
When gas is detected, immediately tighten the union and check for gas
leaks. Allow five minutes for any gas to dissipate before continuing with
the startup procedure. Be sure that proper ventilation is available to
dilute and carry away any vented gas.
With furnace in operation, check all of the pipe joints, gas valve connec-
tions and manual valve connections for leakage using an approved gas
detector, a non-corrosive leak detection fluid or other leak detection
methods. Take appropriate action to stop any leak. If a leak persists,
replace the faulty component.
The furnace and its equipment shutoff valve must be disconnected from
the gas supply during any pressure testing of that system at test pres-
sures in excess of 1/2 PSI (3.45 kPa).
The furnace must be isolated from the gas supply piping system by
closing the equipment shutoff valve during any pressure testing of the
gas supply system.
CALCULATING THE FURNACE INPUT
(NATURAL GAS)
Burner orifices are sized to provide proper input rate using natural gas
with a heating value of 1030 BTU/Ft
3
(38.4 MJ/m
3
). If the heating value
of your gas is significantly different, it may be necessary to replace the
orifices.
Verify natural gas input rate by clocking meter.
1.
Turn off all other gas appliances and pilots.
2.
Run furnace for a minimum of 3 minutes in heating operation.
3.
Measure time (in sec) for gas meter to complete 1 revolution and
note reading. The 2 cubic ft dial provides a more accurate measure-
ment of gas flow.
4.
Refer to Table 14 for cubic ft of gas per hour.
5.
Multiply cubic ft per hour by heating valve (BTU/cu ft) to obtain
input.
If clocked rate does not match the input rate from the unit nameplate,
follow steps in next section to adjust the manifold pressure. Repeat
steps 2 to 5 until correct input is achieved.
IMPORTANT:
All electrical connections made in the field and in the
factory must be checked for proper tightness.
WARNING
FIRE OR EXPLOSION HAZARD
Failure to follow the safety warnings exactly could result in serious
injury, death or property damage.
Never test for gas leaks with an open flame. Use a commercially
available soap solution made specifically for the detection of leaks
to check all connections. A fire or explosion may result causing
property damage, personal injury or loss of life.
IMPORTANT:
Burner ignition may not be satisfactory on first
startup due to residual air in the gas line or until gas manifold pres-
sure is adjusted. The ignition control makes three attempts to light
before locking out.
!
WARNING
HOT SURFACE IGNITION SYSTEM
Do not attempt to light this furnace by hand (with a match or
any other means). There may be a potential shock hazard from
the components of the hot surface ignition system. The fur-
nace can only be lit automatically by its hot surface ignition
system.
NOTICE
DO NOT set manifold pressure less than 3.2 in. W.C. or more than
3.8 in. W.C. for natural gas at sea level. If manifold pressure is out-
side this range, change main burner orifices.
NOTICE
If orifice hole appears damaged or it is suspected to have been
redrilled, check orifice hole with a numbered drill bit of correct size.
Never redrill an orifice. A burr-free and squarely aligned orifice hole
is essential for proper flame characteristics.
CAUTION
DO NOT bottom out gas valve regulator adjusting screw. This can
result in unregulated manifold pressure and result in excess over-
fire and heat exchanger failures.
CAUTION
Be sure to relight any gas appliances that were turned off at the
start of this input check.
!
!
!