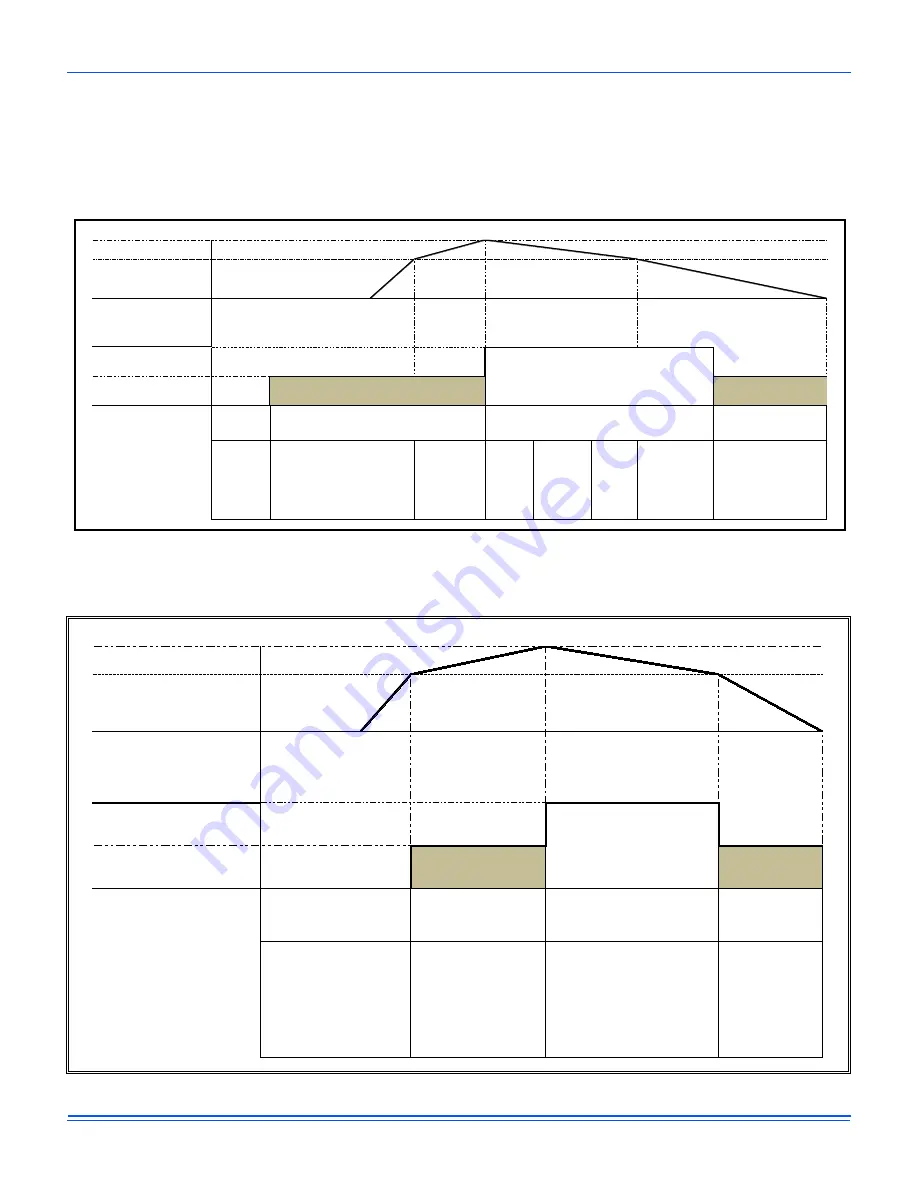
1133391-YIM-A-1014
48
Johnson Controls Unitary Products
Indoor blower operation is initiated upon a call for first stage
cooling, second stage cooling or dehumidification.
Anytime there is a call for a second stage of cooling, the unit will
not operate in the reheat mode, even if there is still a call for
dehumidification at terminal RAT.
The unit will not operate in the reheat mode if there is any call
for heating.
All safety devices function as previously described.
Figure 29: Dehumidification With No Y1 Call For Cooling
Figure 30: Dehumidification With A Y1 Call For Cooling
Y2
Temperature High calling
for cooling
1
Y
1
Y
Temperature
ƐĂƟƐĮĞĚ
Compressor On, No Reheat
Compressor On, Reheat
Compressor
Kī
No Reheat
ĞŚƵŵŝĚŝĮĐĂƟŽŶ
w/Reheat
Y1 Call for
Cooling is
ƐĂƟƐĮĞĚ
Y1 Call for Cooling ,
ĞŚƵŵŝĚŝƐƚĂƚ
Calling
Y2 Call for
Cooling
De-
ŚƵŵŝĚŝƐƚĂƚ
calling or not
calling
Y2 Call for
Cooling is
ƐĂƟƐĮĞĚ
Y1 is Calling for
Cooling,
ĞŚƵŵŝĚŝƐƚĂƚ
is
not
calling
Y1
is
Calling
for
Cooling,
De-
ŚƵŵŝĚŝƐƚĂƚ
is calling
ĞŚƵŵŝĚŝĮĐĂƟŽŶ
w/Reheat
De-
ŚƵŵŝĚŝƐƚĂƚ
calling,
,ƵŵŝĚŝƚLJ
ƌĞĚƵĐƟŽŶ
with no Sensible Cooling
No Reheat
Operational Sequence Of the 3-5 Ton Hot Gas Reheat Unit
Y2 Setpoint is 2
ĚĞŐƌĞĞƐ
above
Y1 Setpoint
Y2
Temperature High calling
for cooling
Y1
Y1
Temperature sa
Ɵ
s
Į
ed
Compressor On, No Reheat
Compressor On, Reheat
Compressor O
ī
Y2 Setpoint is 2
degrees above Y1
Operational Sequence Of the 3-5 Ton Hot Gas Reheat Unit
Y1 Call for Cooling is Sa
Ɵ
s
Į
ed
Y1 is Calling for Cooling,
De-humidistat is calling
Y2 is Calling for Cooling,
De-humidistat is calling
or not calling
Y1 is Calling
for Cooling,
De-humidistat is
calling
No Reheat
Dehumidi
Į
ca
Ɵ
on w/Reheat
No Reheat
Dehumidi
Į
ca
Ɵ
on
w/Reheat